Daihua Li, Weifeng He, Xiangfan Nie, Yuhang Wu, Jile Pan. Enhancing Ultra-High Cycle Fatigue Properties of GH4169 Alloy Using Microscale Laser Shock Peening[J]. Chinese Journal of Lasers, 2025, 52(12): 1202201

Search by keywords or author
- Chinese Journal of Lasers
- Vol. 52, Issue 12, 1202201 (2025)

Fig. 1. Metallographic structure of GH4169 with EDS analysis results of phase indicated by arrow shown in inset

Fig. 2. Schematic diagram of ultra-high cycle fatigue specimen (unit: mm)
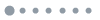
Fig. 3. Microscale laser shock peening treatment. (a) Microscale laser shock peening diagram; (b) microscale laser shock peening area and scanning path of microscale laser shock peening
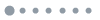
Fig. 4. S-N curves of different samples
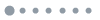
Fig. 5. Ultra-high cycle fatigue fracture of untreated specimen (σa=425 MPa, Nf=1.56×107). (a) General view of fatigue fracture; (b) crack growth region and crack initiation region; (c) enlarged view of crack initiation region
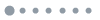
Fig. 6. Ultra-high cycle fatigue fracture of 62 mJ&1 time specimen (σa=425 MPa, Nf=1.21×108). (a) General view of fatigue fracture; (b) general view of crack initiation region; (c) edge of crack initiation region; (d) enlarged view of crack initiation region
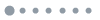
Fig. 7. Ultra-high cycle fatigue fracture of 62 mJ&3 times specimen (σa=425 MPa, Nf=7.88×108). (a) General view of fatigue fracture;(b) general view of crack initiation region; (c) facet morphology;(d) edge of crack initiation region with carbon element distribution in inclusion shown in inset
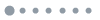
Fig. 8. Ultra-high cycle fatigue fracture of 82 mJ&1 time specimen (σa=425 MPa, Nf=4.32×108). (a) General view of fatigue fracture; (b) crack initiation region; (c) facet morphology
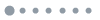
Fig. 9. Three-dimensional morphologies of specimens. (a) Untreated; (b) 62 mJ&1 time; (c) 62 mJ&3 times; (d) 82 mJ&1 time
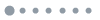
Fig. 10. Surface roughness values of specimens
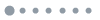
Fig. 11. Residual stress distributions of treated specimens in gradient direction
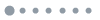
Fig. 12. Inverse pole figures and KAM diagrams of surfaces along gradient direction. (a)(b) Untreated; (c)(d) 62 mJ&1 time; (e)(f) 62 mJ&3 times; (g)(h) 82 mJ&1 time
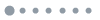
Fig. 13. Grain size distributions of surface layer after microscale laser shock peening
|
Table 1. Chemical compositions of GH4169 (mass fraction, %)
|
Table 2. Mechanical properties of GH4169
|
Table 3. Process parameters of microscale laser shock peening
|
Table 4. GND density distributions of surface layers after microscale laser shock peening under different parameters and average GND densities

Set citation alerts for the article
Please enter your email address