
- High Power Laser Science and Engineering
- Vol. 2, Issue 2, 02000e13 (2014)
Abstract
1. Introduction
Laser-driven inertial fusion energy is one of the most promising approaches for the sustainable generation of electrical power. Research on laser-driven inertial confinement fusion (ICF) has resulted in the world’s largest laser systems, such as NIF and LMJ [:YAG gain medium based concept for a
DPSSL amplifier that could potentially be scaled to the kJ regime[
In this paper, we examine the predicted performance of a kJ-class HiLASE laser which is based on a gas-cooled slab-stack architecture. It uses multiple thin slabs of :YAG gain medium, face-cooled with high-pressure streaming helium gas[
2. Energetics modeling
To quantitatively assess energy storage and amplified spontaneous emission (ASE) losses within the laser active material in multi-slab geometry, a numerical model has been developed[
Sign up for High Power Laser Science and Engineering TOC. Get the latest issue of High Power Laser Science and Engineering delivered right to you!Sign up now
Based on the excited ion density, the spontaneously emitted photons are generated in the form of rays. Each ray is traced through the slab and the number of photons is changed after the ray undergoes amplification or absorption. At the same time, the excited ion density in appropriate cells is also recalculated. Photons that are not absorbed in the cladding propagate up to the side edge of the slab. The probability of reflection at the edge is calculated from the Fresnel equations for the incident angle of the ray. If photons are reflected back, they pass through the absorptive layer again and, if they are not absorbed, they propagate back to the gain medium and decrease the stored energy[
3. Amplifier concept and simulations
For our kJ-class HiLASE laser, we have chosen to model an amplifier with the characteristics derived from the previous ASE and thermal study[:YAG slabs with transverse dimensions of 14 cm
14 cm. A 2 cm wide
:YAG absorptive cladding (
at 1030 nm) around the edge of each slab was also included to further suppress ASE and prevent unwanted parasitic oscillations. The edges of the cladding were modeled as roughened surfaces which scatter rays. The optimized doping concentrations for the eight-slab amplifier were 0.29, 0.38, 0.56, and 0.85 at.%. The super-Gaussian pump dimensions were kept at 14 cm
14 cm which corresponded to a total pump area of 196
. The operating temperature was allowed to vary between 160 and 240 K. Two different beamline concepts are considered here. In the first concept, the output from a low-energy preamplifier (0.2–5 J) is sent to the main kJ amplifier consisting of two identical heads (Figure
In the second design, the laser beam is preamplified up to a 100 J level and then sent to a single kJ laser head (Figure
To find out how the energy is stored in the amplifier, a time-resolved calculation was conducted. In this case, the two-head design was considered. Figures
Large values of the ASE saturate the gain and the pump duration of 1 ms is too long for effective energy storage at low temperatures (see Figure :YAG (energy needed for the gain medium to stay transparent). The extractable energy as a function of temperature was calculated for different pump intensities for a single amplifier head (Figure
The storage efficiency was calculated as the ratio between the absorbed energy and the extractable energy (Figure
Based on the previous results, an operating temperature of 200 K and a pump duration of 1 ms were selected. The following figures give an indication of the evolution of the energy generated after each pass through the pair of amplifiers (Figures
It is noted that an output energy of 0.92 kJ can be reached in the single-head design with reasonably low values of optical losses (10%) and an operating temperature of 200 K. In this case, the input beam can be provided by next-generation high-energy-class (HEC)-DPSSL facilities with output energies in the range of 100–150 J[
4. Beam propagation
In order to carry out fundamental calculations on how a HiLASE kJ laser would operate, a MIRO model has been constructed for the two-head configuration. These calculations are based on previous modeling results for the two-head design for a 100 J-class HiLASE amplifier[) for the lenses and windows of the spatial filters, DKDP (
) for the Pockels cell,
:YAG (
) for the laser slabs, and sapphire (
) for the amplifier head windows. The internal transmission is assumed to be 100% for the lenses, windows, and slabs and 99% for the DKDP Pockels cells. The graphical representation of the MIRO model is shown in Figure
The quality of each component corresponded to at 1030 nm. The calculation was run with a spatial resolution of
and a temporal resolution of 30 ps. The MIRO model included only thermal aberrations. The aim of the calculation was to optimize the input pulse shape as well as to evaluate diffraction and non-linear phase accumulation (breakup integral) in the beam. The initial modeling concentrated on achieving a top-hat temporal output pulse profile. The input pulse profile was obtained by an iteration method. At each step, the input pulse was multiplied by the ratio between the output pulse and the desired output pulse. The optimized input and output temporal profiles of the MIRO model are shown in Figure
Advanced temporal pulse shaping is therefore required on the front end seed source to achieve the desired top-hat pulse profile. Two B integral types are calculated with MIRÓ. The first B integral is reset to zero in each spatial filter where the beam passes through. The second is the accumulated B integral which is the sum of B integrals in all sections between spatial filters. For an input pulse energy of 4 J and a pump intensity of , the evolution of the B integral and the accumulated B integral is shown in Figure
Figures
The diffraction pattern in the beam is caused by shift of the beam due to large aberrations in the system and clipping of the beam. This can be remedied by decreasing the beam size considerably or by adding wavefront correction after each pass by implementing a DM in the laser chain (like NIF and LMJ). An optimized MIRO model which also includes the manufacturing defects of the optical components will be required in the future to provide a detailed understanding of the operational parameters of an optimized HiLASE laser design.
5. Thermal modeling
Substantial analysis has been performed in order to optimize the Yb:YAG gain medium size, coolant flow rates, arrangement of pumped and unpumped regions, and absorbing materials for properly designed (doping/width) cladding. The laser slabs are cooled by forced flow of He gas with a temperature of 190 K and a pressure of 5 bar. The model assumes that the energy deposition is the same for all slabs, which is a fair approximation given the stepped doping profile. A 3D finite-element method (FEM) using Comsol Multiphysics software was chosen to model the thermal effects in the amplifiers and the fluid dynamics of the helium flow. The calculation takes into account the temperature changes of the material parameters[
It is found that the thermal OPD and average depolarization can be substantially reduced by increasing the size of the cladding, and even more drastically by inserting a thin layer of undoped YAG around the gain medium[:YAG cladding. The geometry and zone layout used for heat deposition modeling in the HiLASE amplifier (single and double clad configurations) are shown in Figure
Table
Geometry | Undoped/ | Absorption | ||
---|---|---|---|---|
unpumped | coefficient | |||
Single clad | 140 | 0 | ![]() | ![]() |
Enlarged single clad | 140 | 0 | ![]() | ![]() |
Double clad | 140 | 3 | ![]() | ![]() |
Table 1. The Gain Medium and Cladding Dimensions used for Simulation of HiLASE Square Amplifiers.
Single clad | Enlarged single clad | Double clad | |
---|---|---|---|
![]() | 213.4 | 203.5 | 199.3 |
![]() | 202.1 | 197.5 | 196.1 |
![]() | 36.3 | 3.20 | 0.079 |
OPD (![]() | 8.96 | 2.97 | 1.54 |
OPD w/o TD (![]() | 6.85 | 2.31 | 0.49 |
Table 2. Thermal Results for HiLASE Square Amplifiers (Single, Enlarged Single, and Double Clad).
Figure
Table , the average temperature,
, the total depolarization loss,
, due to eight slabs (one amplifier head), the peak-to-valley (P-V) value of the OPD due to eight slabs, and the total eight-slab OPD with tilt and defocus subtracted.
The double clad geometry showed the minimum depolarization losses and OPD values. It should be noted that the tilted OPD profile in the double clad geometry is due to the helium gas flow which generates a transverse dependence of the heat transfer coefficient. However, the magnitude of the aberrations is well within the correction capability of the current DMs used for adaptive optics (AO)[
6. Wavefront correction
The calculated wavefront of the beam at the output of the laser system (see Figure to
. The numerical model for wavefront correction calculates influence functions from a plate equation describing bending of the thin face sheet for each individual actuator of the DM. Figure
ratio and stroke of the DM.
The deformation of the mirror is computed as a superposition of influence functions and the algorithm minimizes the OPD rms value. Figure and
actuators.
It is noted that the residual rms value after correction is more influenced by the ratio than by the actuator density. Therefore, optimization of the DM requires large-area actuators outside the active region, i.e. large
values rather than high actuator density. It should be noted that the larger the stroke is, the smaller the dynamic range used by the AO system will be. The DM is able to achieve numerical correction of the initial aberrations, as shown in Figure
,
). The OPD after subtraction of defocus and tilt and the OPD corrected by the DM are shown in Figure
The corresponding far-field images before and after wavefront correction are shown in Figures
7. Frequency conversion
Frequency conversion of the fundamental wavelength at 1030 nm to the second and third harmonic wavelengths of 515 and 343 nm allows for more efficient absorption of laser energy by the deuterium–tritium target. In this section, we present the modeling results for the second harmonic generation (SHG) and third harmonic generation (THG) conversion efficiency. It is proposed to use LBO crystal for frequency conversion due to its excellent nonlinear properties and recently demonstrated large crystal sizes[ points was used for the 3D simulations. The spatial profile was assumed to be square shaped with dimensions of
. The intensity profile in the simulations was assumed to be ideal, i.e., to be defined by a super-Gaussian function of the 20th order for the spatial profile and of the eighth order for the temporal profile. To accommodate such a laser beam comfortably, the aperture of the LBO crystal was set to
. Since the shape of the pulse ideally ensures uniform intensity distribution in time and space, very high conversion efficiencies are easily achievable if significant wavefront distortions are absent. Figure
-plane,
. We have assumed a fundamental wavelength pulse energy of 1 kJ, which corresponds to
peak intensity.
As can be seen from Figure 5 mm) with
60% efficiency. Then the pulses of both the first harmonic (FH) and the second harmonic are mixed in a second LBO crystal (type-II, o
e
o) for sum-frequency generation (SFG). The second LBO crystal was oriented for type-II nonlinear interaction,
plane,
. The total THG conversion efficiency is shown in Figure
63% SHG conversion.
Angular and temperature acceptance are important parameters in the case of high energy and high average power operation. In the case of LBO type-I SHG at 1030 nm, we have calculated the angular acceptance using the Sellmeier equations to be 3.42 mrad cm (which yields 2.63 mrad for 13 mm crystal). For the THG via SFG in the given conditions, the angular acceptance was calculated to be 3.09 mrad cm (2.38 mrad for 13 mm crystal). For the temperature acceptance calculation, we currently rely on values provided by SNLO software, recalculated for the full width at half maximum (FWHM) of the function: 6.36 K cm for SHG and 3.19 K cm for THG (for 13 mm crystal 4.89 and 2.45 K accordingly). The acceptance values calculated above are useful for the comparison of different nonlinear crystals. However, in order to evaluate the actual angular tolerance of the crystal for a given pulse, we have also performed a numerical full 3D simulation for a set of angles in the vicinity of optimal phase matching. The simulation shows that the crystal detuning tolerance in this case is 0.93 mrad. We define this number as the FWHM level for the conversion efficiency function. The same simulation was performed for the second LBO crystal of 11.5 mm length, in which the third harmonic was generated via SFG, and it was shown that the crystal detuning tolerance in this case was 1.57 mrad. These simulations show that the output efficiency is more sensitive to angular detuning in the case of high efficiency of the frequency conversion processes and fundamental pulse depletion, in comparison to angular acceptance values calculated from the Sellmeier equations. It is noted that when phase and amplitude distortions become significant, the efficiency of the nonlinear process is expected to decrease. A more extensive model of the frequency convertor which includes amplitude or phase noise will be developed.
References
[2] J. Ebrardt, J. M. Chaput. J. Phys. Conf. Ser., 244, 032017(2010).
[6] M. Sawicka, M. Divoky, A. Lucianetti, T. Mocek. Laser Part. Beams, 31, 553(2013).
[8] T. Novo, D. Albach, B. Vincent, M. Arzakantsyan, J.-C. Chanteloup. Opt. Express, 21, 855(2013).
[14] R. L. Aggarwal, D. J. Ripin, J. R. Ochoa, T. Y. Fan. J. Appl. Phys., 98(2005).
[15] H. Yagi, K. Takaichi, K. Ueda, Y. Yamasaki, T. Yanagitani, A. A. Kaminskii. Las. Phys., 15, 1338(2005).
[16] K. Ueda, J.-F. Bisson, H. Yagi, K. Takaichi, A. Shirakawa, T. Yanagitani, A. A. Kaminskii. Las. Phys., 15, 927(2005).
[19] Z. Hu, Y. Zhao, Y. Yue, X. Hu. J. Cryst. Growth, 335, 133(2011).
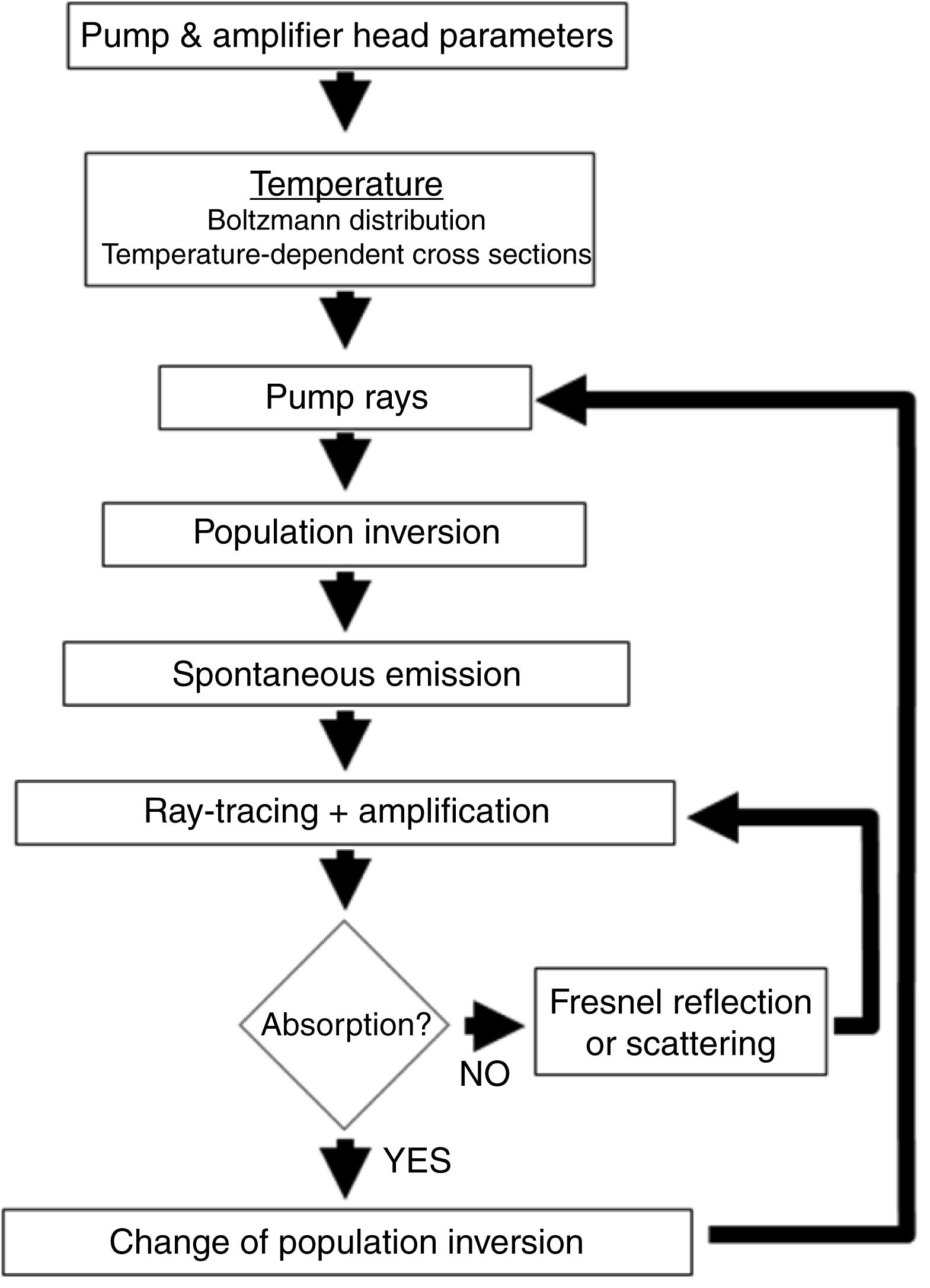
Set citation alerts for the article
Please enter your email address