
- Journal of Inorganic Materials
- Vol. 36, Issue 5, 535 (2021)
Abstract
With the development of communication and radar systems, the microwave dielectric materials have been extended to millimeter wave range, which requires that the dielectric ceramics possess low dielectric constant (<20, usually) to avoid the delay of electronic transition[
By comparison, Si3N4 ceramics are known for its superior mechanical properties[
According to the Lichtenecker’s logarithmic law of mixing, the introduction of particles with high dielectric constant could be an efficient strategy to enhance and tailor the dielectric constant of Si3N4 ceramics. Among the various ferroelectrics with high dielectric constant, BaTiO3 possesses the advantages of high insulation, high permittivity, high thermal stability, low cost, wide application and so on[
Hence, BaTiO3 particles was adopted to enhance the dielectric property of Si3N4 ceramics in this investigation. In order to achieve higher density and reduce the impact of pores on the dielectric loss, which is difficult to be overcome in the pressureless sintered and gas pressure sintered Si3N4 ceramics, hot pressing was used for the densification of Si3N4 ceramics. Meanwhile, considering the low melting point (1625 ℃) of BaTiO3, Al2O3-Nd2O3 instead of conventional Al2O3-Y2O3 were used as sintering additives to lower the sintering temperature so as to avoid or decrease the volatilization of BaTiO3. 5wt%-20wt% BaTiO3 was added to improve the dielectric constant of Si3N4 ceramics. The flexural strength, fracture toughness and Vickers’ hardness were measured to evaluate the effect of BaTiO3 addition on the mechanical properties of Si3N4 ceramics. The dielectric constant and dielectric loss were measured to study the effect of BaTiO3 addition on the dielectric properties of Si3N4 ceramics.
1 Experimental procedure
1.1 Materials preparation
α-Si3N4 (0.5 μm, purity>99.9%, ANSM New Energy Technology Co., Ltd., Jiangsu, China) and BaTiO3 (2 μm, purity>99.9%, Qinhuangdao ENO High-Tech Material Development CO., Ltd., Hebei, China) were used as the starting materials. Al2O3 (0.4 μm, purity>99.9%, Fenghe Ceramic Co., Ltd., Shanghai, China) and Nd2O3 (2 μm, purity>99.9%, Qinhuangdao ENO High-Tech Material Development CO., Ltd., Hebei, China) were added as sintering additives.
Specimen powders were prepared by a conventional wet chemical method. Initially, four batches of powder mixtures consisting of Si3N4 powder, 3.68wt% Al2O3, 6.32wt% Nd2O3 and 5wt%-20wt% BaTiO3 were homogenized in ethanol by ball milling at 300 r/min for 4 h. Subsequently, the resulting slurries were dried at 70 ℃ for 12 h. The dried powders were screened by a 149 μm (100 mesh) stainless steel sieve. The as-received powders were placed into a graphite die and then hot pressed at 1680 ℃ for 2 h in a graphite furnace under flowing N2 atmosphere. A uniaxial pressure of 20 MPa was applied through top graphite plungers. The obtained compacts were machined into rectangular bars with a size of 36 mm × 4 mm × 3 mm for mechanical tests and disks with the size of φ15 mm × 2 mm for dielectric tests.
1.2 Materials characterization
The apparent density (ρ) was measured by the Archimedes method. The flexural strength was measured by a three-point bending method with a span of 30 mm at a cross-head speed of 0.5 mm/min, using an Instron universal testing machine (Model 5566). Hardness was measured by Vickers’ indentation applying a load of 49 N for 10 s on a polished section. The fracture toughness was estimated from the crack length generated by indents using the Evans and Davis’s equation[
The dielectric constant (ɛ) and dielectric loss (tanδ) of the specimens were measured by RF impedance/material analyzer (Model 4291B, Agilent, USA) in the frequency range from 100 MHz to 1 GHz at room temperature.
The phase compositions of the specimens were determined using X-ray diffraction (D8 ADVANCE, Bruker, Germany) with Cu Kα radiation. The diffraction data were collected within 10°-80° of 2θ range at a scanning step of 2 (°)/min. The morphologies of the polished and etched surfaces were observed by scanning electron microscope (Magellan 400, FEI, USA).
2 Results and discussion
2.1 Phase composition and microstructure
Fig. 1 shows the XRD patterns of the hot-pressed Si3N4 ceramics with 5wt%-20wt% BaTiO3 addition. Obviously, regardless of the addition of BaTiO3, the major phase was β-Si3N4, indicating that the α-Si3N4 were transformed to β-Si3N4 due to the enhanced liquid phase flowing promoted by the external pressure during the hot pressing process, which facilitated the solution-precipitation process of Si3N4. No diffraction peaks of BaTiO3 were detected, instead, diffraction peaks of TiN (JCPDS 65-0414) could be detected in these four specimens. In addition, diffraction peaks of Ba5Al2O8 (JCPDS 28-0120) appeared when the amount of BaTiO3 increased to 15wt%. The diffraction peaks of TiN and Ba5Al2O8 intensified with the increase of BaTiO3 content, indicating the continuous formation of TiN and Ba5Al2O8. It has been reported that BaTiO3 may decompose into BaO and TiO2 during the sintering process[
Figure 1.XRD patterns of the hot-pressed Si3N4 ceramics with 5wt%-20wt% BaTiO3
Fig. 2 reveals the microstructures of the Si3N4 specimens with 5wt%-20wt% BaTiO3. Obviously, all these specimens were highly densified without visible voids or microcracks. The microstructure consisted of dark Si3N4 phase with elongated and equiaxed shapes, and bright grain boundary phase composed of the sintering additives and BaTiO3- related reaction products. On the other hand, the grain size and amount of elongated Si3N4 grains decreased with the increase of BaTiO3 content, due to the grain refinement effect of liquid phase which increased with more BaTiO3 addition.
Figure 2.Microstructure images of the Si3N4 specimens sintered with (a) 5wt%, (b) 10wt%, (c) 15wt% and (d) 20wt% BaTiO3
2.2 Densification and mechanical properties
Fig. 3 illustrates the dependence of relative density and flexural strength of the Si3N4 ceramics on the BaTiO3 content. Clearly, the relative density could reach as high as 96% without the addition of BaTiO3, which was attributed to the fact that the uniaxial pressure was beneficial for the densification of ceramics by improving the fluidity of the liquid phase and elastic deformation of the grains. Nevertheless, the relative density exhibited slight decrease with the increase of BaTiO3 content, which demonstrated that the liquid phase formed by the sintering additives (Al2O3 and Nd2O3) was already enough to promote the densification. Therefore, the additional liquid phase formed by the BaTiO3-related products did not further improve the densification under hot pressing. Moreover, the redundant liquid phase would be squeezed out from the specimens due to the external pressure. Consistent with the trend of relative density, the flexural strength decreased obviously with the addition of BaTiO3. The flexural strength of sample without BaTiO3 was as high as (767.6±32.9) MPa. However, the flexural strength decreased to (752.3±41.1) MPa, (728.8±59.7) MPa, (681.2±63.2) MPa and (637.8±53.5) MPa with the BaTiO3 addition of 5wt%, 10wt%, 15wt% and 20wt%, respectively.
Figure 3.Relative densities and flexural strength of the hot-pressed Si3N4 ceramics varying with the addition of BaTiO3
On the one hand, the degradation of flexural strength is attributed to the addition of BaTiO3 which has lower flexural strength inherently. On the other hand, the grain size and amount of elongated Si3N4 grains both decreased with the increase of BaTiO3 addition. It is well acknowledged that the excellent mechanical property of Si3N4 ceramic is endowed by its unique microstructure of interlocked rod-like grains[
The influence of BaTiO3 addition on the indentation fracture toughness and Vickers’ hardness is shown in Fig. 4. The fracture toughness of Si3N4 ceramics without BaTiO3 was (4.92±0.24) MPa·m1/2. When 5wt% BaTiO3 was added into the Si3N4 ceramics, the fracture toughness increased to (5.72±0.22) MPa·m1/2. With the further increase of BaTiO3 content to 20wt%, the fracture toughness increased continuously to (7.26±0.14) MPa·m1/2, which was 47.6% higher than that of the Si3N4 ceramics without BaTiO3, indicating that the addition of BaTiO3 was indeed beneficial for the improvement of fracture toughness. The reason for the increase of fracture toughness could be found from the crack propagation path induced by indentation tests. As shown in Fig. 5, in addition to the crack deflection induced by the elongated Si3N4 grains which endows Si3N4 ceramics with high fracture toughness in essence, the addition of BaTiO3 introduced extra toughening mechanisms such as crack deflection, branching and bridging into the Si3N4 matrix due to the thermal expansion coefficient (TEC) mismatch between Si3N4 (3.0×10-6 K-1)[
Figure 4.Influence of BaTiO3 addition on the indentation fracture toughness and Vickers’ hardness of the hot-pressed Si3N4 ceramics
Figure 5.Toughening mechanisms induced by the addition of BaTiO3 to the hot-pressed Si3N4 ceramics(a) 5wt%; (b) 10wt%; (c) 15wt%; (d) 20 wt%
On the contrary, the Vickers’ hardness decreased with the increase of BaTiO3 content. It can be seen that the slope of line ab (as labeled in Fig. 4) was steeper than that of line b-e, indicating the Vickers’ hardness of Si3N4 ceramics dropped more sharply when the addition of BaTiO3 increased from 0 to 5wt%. This demonstrated that the addition of BaTiO3 dominated the mechanism of hardness decrease. Quite understandably, this was attributed to the fact that the Vickers’ hardness of ceramics meet the rule of the mixture. Because the hardness of BaTiO3-related reaction products is much lower than that of β-Si3N4 (14-16 GPa), it is reasonable that the Vickers’ hardness decreases continuously with the addition of BaTiO3 increasing.
The hardness of ceramics also strongly depends on its porosity according to Eq. (4):
where H represents the hardness, H0 is the hardness without pores, b is a pre-exponential constant (which ranges from 2 to 8 relying on the ceramic investigated), and, P is the porosity of the ceramic[
Obviously, the porosity intensively reduces the resistance of the microstructure against the applied loads[
2.3 Dielectric properties
The dielectric constant is defined as the ratio between the absolute permittivity of material and the absolute permittivity of vacuum. The higher the dielectric constant, the stronger the ability to bind charge. For the dielectric substrate application, higher dielectric constant is favored for the miniaturization of resonator. The dielectric constant of hot-pressed Si3N4 ceramic without BaTiO3 was 7.56. Fig. 6 summarizes the dielectric constant (ε) and dielectric loss (tanδ) of specimens with 5wt%-20wt% BaTiO3 frequency. Obviously, the dielectric constant increased monotonically from 9.26 to 11.50 for the Si3N4 ceramics blended with BaTiO3 content increasing, which increased by 23.5%-53.3% compared to the Si3N4 ceramics without BaTiO3. Considering the fact that the dielectric constant of the composites obeys the logarithmic law[
Figure 6.Change of dielectric constant and dielectric loss with frequency for the hot-pressed Si3N4 ceramics with different BaTiO3 additions
3 Conclusions
In the present work, the mechanical and dielectric properties of hot-pressed Si3N4 ceramics with the addition of 5wt%-20wt% BaTiO3 have been investigated. While the relative density, flexural strength, Vickers’ hardness and dielectric constant decreased with the increase of BaTiO3 addition, the fracture toughness increased. The flexural strength of these Si3N4 ceramics exceeded 600 MPa, much higher than those of traditional microwave dielectric ceramics. The dielectric constant of hot-pressed Si3N4 ceramics could be improved by the addition of BaTiO3. The dielectric loss was at the level of 10-3, which is tolerable for application.
References
[1] XUN YE, WEN LEI, WEN-ZHONG LU. Microwave dielectric characteristics of Nb2O5-added 0.9Al2O3-0.1TiO2 ceramics. Ceramics International, 35, 2131-2134(2009).
[2] YING DAI, TENG GUO, XIN-MEI PEI et al. Effects of MCAS glass additives on dielectric properties of Al2O3-TiO2 ceramics. Materials Sciences and Engineering A, 475, 76-80(2008).
[3] JIN-MIN CHEN, HUAN-PING WANG, SI-QIAO FENG et al. Effects of CaSiO3 addition on sintering behavior and microwave dielectric properties of Al2O3 ceramics. Ceramics International, 37, 989-993(2011).
[4] KAI-XIN SONG, SHU-YA WU, XIANG-MING CHEN. Effects of Y2O3 addition on microwave dielectric characteristics of Al2O3 ceramics. Materials Letters, 61, 3357-3360(2007).
[5] Y MIYAUCHI, Y OHISHI, S MIYAKE et al. Improvement of the dielectric properties of rutile-doped Al2O3 ceramics by annealing treatment. Journal of the European Ceramic Society, 26, 2093-2096(2006).
[6] A KUMAR, A GOKHALE, S GHOSH et al. Effect of nano-sized sintering additives on microstructure and mechanical properties of Si3N4 ceramics. Materials Sciences and Engineering A, 750, 132-140(2019).
[7] XIAO-MING DUAN, DE-CHANG JIA, JIE DENG et al. Mechanical and dielectric properties of gelcasted Si3N4 porous ceramic using CaHPO4 as an additive. Ceramics International, 38, 4363-4367(2012).
[16] A G EVANS. Fracture Toughness: The Role of Indentation Techniques. In Fracture Mechanics Applied to Brittle Materials (Freiman, W., ed.). ASTM STP 678. West Conshohocken, PA, 112-135(1979).
[18] WEI-MING GUO, JUN-JIE YU, HUA-TAI LIN. A Equiaxial-Grain β-Si3N4+TiN+O-Sialon Composite and Its Preparation Method. Chinese, Patent: 201610279603.9, 09, 21(2016).
[19] L M KOVBA, L N LYKOVA, E V ANTIPOV et al. Double oxides of barium and aluminum. Russian Journal of Inorganic Chemistry, 32, 301-302(1987).
[22] XIAO-QI SHI. Preparation and Properties of TiN-Al2O3 Composites. Xi'an: Dissertation of Xi'an University of Architecture and Technology(2007).
[24] F J PANETO, J L PEREIRA, J O LIMA et al. Effect of porosity on hardness of Al2O3-Y3Al5O12 ceramic composite. International Journal of Refractory Metals and Hard Materials, 45, 365-368(2015).
[25] J DUSZA, T ESCHNER, K RUNDGREN. Hardness anisotropy in bimodal grained gas pressure sintered Si3N4. Journal of Materials Science Letter, 16, 1664-1667(1997).
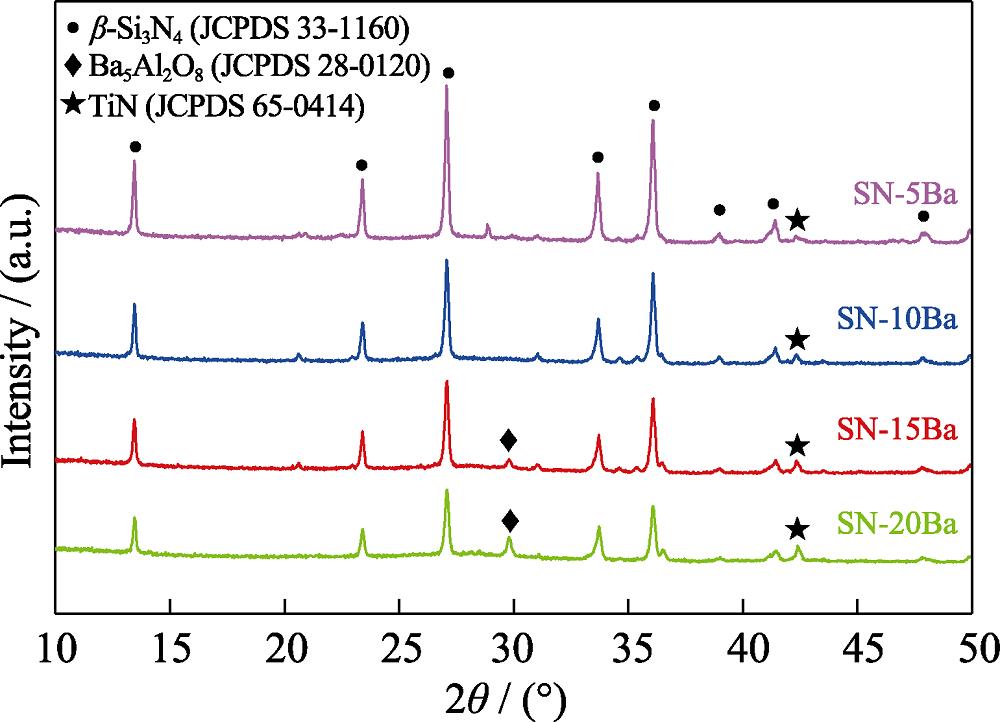
Set citation alerts for the article
Please enter your email address