Peng Zhao, Shouren Wang, Gaoqi Wang, Zhen Xiao, Shaoping Gao, Xiaoping Liu. Microstructure and Wear Resistance of Laser Cladding Al-Si-Ni-WC Coating on Aluminum Brake Disc Surfaces[J]. Chinese Journal of Lasers, 2023, 50(20): 2002203

Search by keywords or author
- Chinese Journal of Lasers
- Vol. 50, Issue 20, 2002203 (2023)
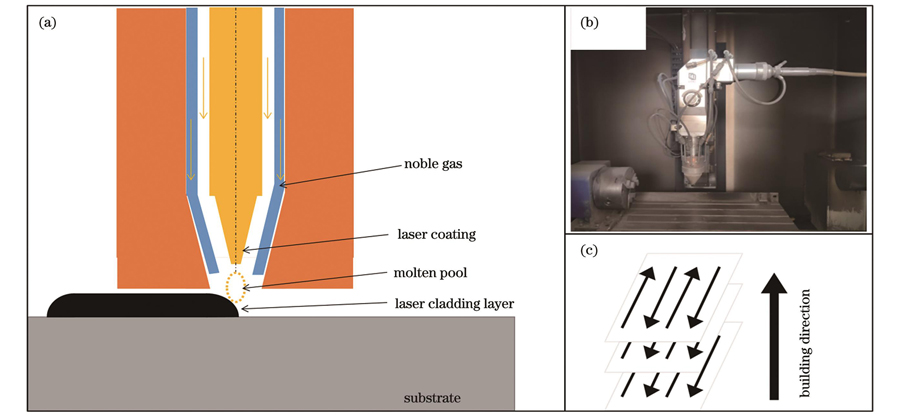
Fig. 1. Laser cladding equipment and processing principle. (a) Principle diagram of processing; (b) laser; (c) cladding molding route
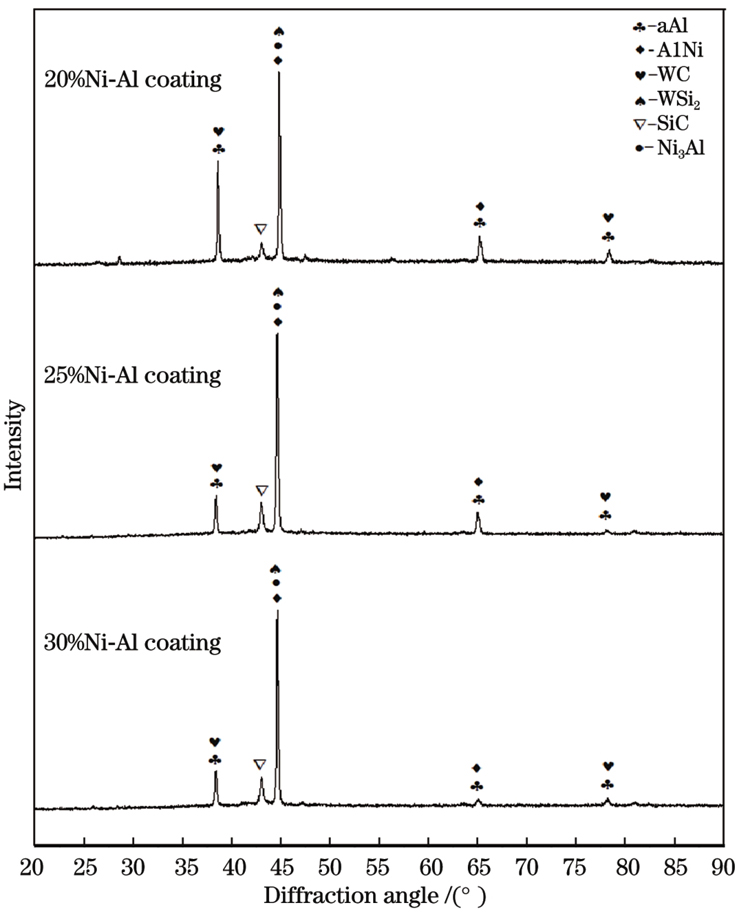
Fig. 2. XRD patterns of alloy coatings under different Ni mass fractions
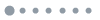
Fig. 3. SEM images of coatings under different Ni mass fractions. (a) 20%; (b) 25%; (c) 30%; (d) 35%
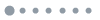
Fig. 4. EDS images of coating when Ni mass fraction is 30%. (a1)-(a8) EDS images near WC; (b1)-(b8) EDS images in middle of coating
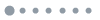
Fig. 5. Microhardness of coating cross section and SEM images of bonding surface. (a) Microhardness; (b) SEM image of bonding surface; (c) partial enlarged view of Fig. 5(b)
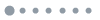
Fig. 6. Friction coefficients of substrate and coating under different temperatures. (a) Friction coefficient curves; (b) average friction coefficient
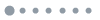
Fig. 7. Wear volumes of matrix and coating. (a) Wear volumes of substrate and coating under different Ni mass fractions; (b) wear volumes of substrate and coating when Ni mass fraction is 30% at different temperatures
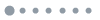
Fig. 8. Wear depths of substrate and alloy coatings under different Ni mass fractions. (a) Substrate; (b) 20%; (c) 25%; (d) 30%
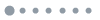
Fig. 9. Abrasion morphologies of substrate and cladding coating at different temperatures. (a) Substrate, normal temperature; (b) substrate, 100 ℃; (c) coating, normal temperature; (d) coating, 100 ℃
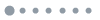
Fig. 10. Schematics of wear mechanism. (a) Early wear; (b) abrasive wear; (c) adhesive wear; (d) oxidative wear
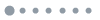
Fig. 11. Electrochemical polarization curves of substrate and alloy coating
|
Table 1. Chemical element compositions of ZL108 aluminum alloy matrix
|
Table 2. Chemical element compositions of cladding alloy powder
|
Table 3. Process parameters of laser cladding experiment
|
Table 4. Electrochemical calculation results of substrate and coating
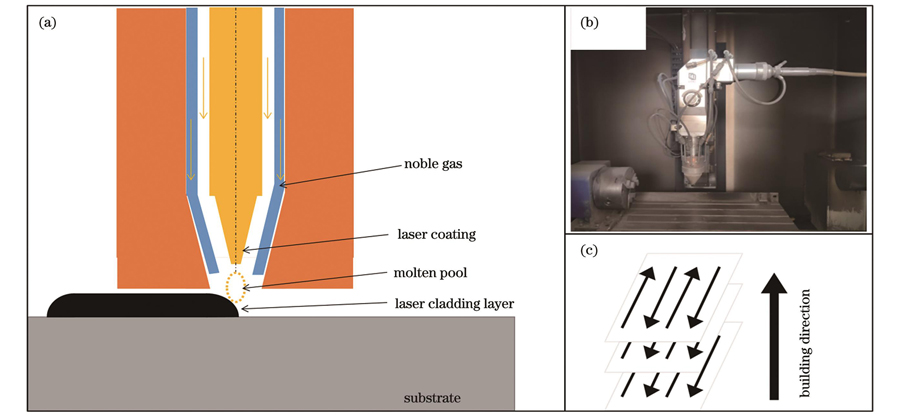
Set citation alerts for the article
Please enter your email address