
- Opto-Electronic Advances
- Vol. 4, Issue 4, 210008-1 (2021)
Abstract
Keywords
Introduction
Many species in nature, such as plants
Inspiration from natural functional structures, especially famous water repellent plant leaves, like lotus leaves, a variety of artificial superhydrophobic surfaces with liquid-repellent properties have been designed and fabricated through the uniquely constructed geometrical micro/nanostructures and the chemical composition of the surface
Compared with traditional surfaces with hydrophobic property, the manufacture of superhydrophobic surfaces with unique versatility has broad applications and has become a hot topic in the field of surface technology. Constructing functional superhydrophobic surfaces with high stability, versatility, flexibility, and universality have a high practical value
In this work, the directional transportation directivity of the bionic snake scale-like superhydrophobic surface has been reported for the first time. It was inspired from the unique superhydrophobicity and frictional anisotropy properties of the snake scales, which are promising for a wide range of scientific fields
Materials and methods
Material
The experiment is performed on 316L stainless steel substrates with a thickness of 2 mm. Before laser ablation, the 316L stainless steel plates (50 mm × 50 mm) are polished using 800# abrasive papers and ultrasonically cleaned in deionized water to remove oxide layers and impurities.
Laser ablation
The polished samples are ablated by a Q-switched DPSS laser (Model: AVIA LX 355-20-50, Coherent) with a wavelength of 355 nm, pulse duration of 10 ns, and repetition rate up to 50 kHz. The output power can be continuously tuned with a variable attenuator. A 3D galvanometric scanner is employed to move the laser beam along X-, Y- and, Z-directions over a sample surface. The laser is focused normally and obliquely incident (45°) onto the sample surfaces through an f-theta lens, producing a focal spot diameter of about 30 µm. Programmable patterns including snake scale structures textures, randomly distributed nanoparticles, and periodic inclined cone-shaped structures are generated on the pretreated plate surfaces by laser with different laser powers (4.2 W, 0.5 W, and 0.5 W), different repetition rates (50 kHz, 30 kHz, and 30 kHz), different scanning times (1000 times, 1 time, and 1 time), and different scanning speeds (50 mm/s, 1 mm/s, and 1 mm/s) by different steps of the laser processing, respectively. Moreover, the scanning space of the second and third steps are both 30 μm. Then, the textured substrates are ultrasonically cleaned in deionized water for 10 min to remove the floating steel powder on the surface and put in the ambient air for a long time without any chemical modification treatment.
Results and discussion
Stainless steel, which is one of the most commonly used materials in today’s society, is chosen as a substrate material for superhydrophobic surface fabrication due to its outstanding properties, such as thermal stability, chemical resistance, nontoxicity, and high mechanical strength. Laser precision engineering, which has already been proved as a valuable, versatile, and reliable technique in the fabrication of biomimetic structures and devices that feature natural materials due to its advantages of rapid, mask-free, chemical-free, and large-area micro-nanofabrication
Figure 1.
To quantificationally investigate the influence of the three-level hierarchical structures of the snake scale-like surfaces on directional superhydrophobicity, liquid-repellent property measurement has been carried out for the laser fabricated snake scale-like surfaces with different hierarchical structures, and the sliding property of the as-prepared surfaces has been tested both along and against the snake scale direction. Each measured value is averaged over three locations. As shown in Fig. 2, the SEM images of micro/nanostructured snake scale-like surfaces with different hierarchical structures at different amplified scales have been shown. It can be seen that the overall surfaces are periodic arrangement of snake scales and oblique grooves with different hierarchical structures by one step, two steps, and three steps of the laser precision engineering, respectively (Figs. 2(a), 2(d) and 2(g)). Enlarged images demonstrate that the surface roughness of the as-prepared samples becomes larger with the increase of processing steps (Figs. 2(b), 2(e) and 2(h)), and through the three steps of the laser processing, the microscale inclined cone-shaped structures are created on each unit of the snake scale-like structure array. As shown in Figs. 2(c), 2(f) and 2(i), the surface is gradually adhered by more and more particulate melt protrusions with the increase in processing steps, and the size of particulate melt protrusions getting smaller and smaller to the nanoscale. These results indicate that the as-prepared surface by the three steps of the laser processing have similar three-level hierarchical micro/nanostructures with those on the real snake scale. The surfaces with different hierarchical structures exhibit different wetting properties, and the CA (5 µL water droplet) measured parallel to surfaces with different hierarchical structures are about 73°, 133°, and 159° as shown in the bottom-left corner of Figs. 2(a), 2(d) and 2(g), respectively. Considering the fact that the CA of the pristine stainless steel with a flat surface is only about 72°, the IBLA fabricated hierarchical micro/nanostructures are considered to be an essential factor to gain the hydrophobicity. Figure 2(j) depicts the time-dependence of CAs for the as-prepared surfaces with different hierarchical structures by different steps of the laser processing when they are exposed to air. Before the laser treatment, all the bare stainless steel surfaces were hydrophilic. Once ablated by laser, the fresh stainless steel surfaces immediately exhibit hydrophilic or even superhydrophilic behavior, and the water droplet can even fully spread out when it touches the laser-induced rough surface. It is unable to acquire a CA value as the droplet is almost completely penetrated into the grooves. This phenomenon is well pronounced within 10 days after the laser ablation. According to the Wenzel theory, the increase of surface roughness leads to an amplification effect of surface wettability
Figure 2.
where r > 1 is surface roughness parameter; θf and θw represent CAs for the flat and rough surfaces, respectively. Equation (1) reveals that with the enhancement of surface roughness, a hydrophilic surface becomes more hydrophilic and a hydrophobic surface becomes more hydrophobic. Therefore, at early stage of CA evolution, the fresh stainless steel surfaces exhibit very small contact angles due to the increment of roughness. Another reason for the observed superhydrophilicity is the change of surface chemical compositions before/after the laser ablation, which will be explained in detail in the mechanism section later. Observing contact angle curve in Fig. 2(j), it is noted that when the laser ablated surfaces are exposed to air, their surface hydrophilicity decreases and the CA increases over time. Between Day 11 and Day 30, the CA of surfaces by the two steps and three steps of laser processing witnessed a sharp increase from 0° to 127° and 0° to 139°, respectively. It is noted that fresh surfaces reach hydrophobic behaviors. With the time exposed to air increases, only the surface CA by the three steps of laser processing exceeds 150°, and the CA of 159° is obtained when the three steps laser-induced surface is exposed to ambient air for 40 days. Then, CA gradually remains in a relatively stable state of 159 ± 2°, which can be characterized as a typical superhydrophobic surface. Thus, it can be concluded that after the laser ablation and exposure to air, only the three steps laser-induced three-level hierarchical micro/nanostructured surface shows superhydrophobicity. Additionally, as shown in Fig. 2(k), the as-prepared surface by the three steps of laser processing retains superhydrophobicity for a long time (at least 30 hours) in contact with water until the droplets on the surface evaporate. Meanwhile, the superhydrophobicity is also maintained by re-measurement at the location where the droplets evaporate.
Like the snake skin, such a snake scale-like three-level hierarchical micro/nanostructured surface displays superhydrophobic anisotropic sliding. As shown in Fig. 2(l) and Movie S1 (see Supplementary information), in the negative direction (CA = 159° ± 1.5°, SA = 81° ± 1.5°, measured parallel to the surfaces), SA is larger than that in the positive direction (CA = 159° ± 1.5°, SA = 7° ± 1.5°, measured parallel to the surfaces), positive direction and negative direction are the measured directions as labeled in Figs. 2(a), 2(d) and 2(g). These results demonstrate that anisotropic superhydrophobic and directional sliding states can be realized by this snake scale-like three-level hierarchical micro/nanostructured surface. Herein, the surface chemical modification has not been utilized in the preparation, which means that the unique three-level hierarchical micro/nanostructures mainly induce the directional wetting performance.
To evaluate the directional control of the water-sliding ability, the sliding process is monitored in real time, the positive and negative directions sliding states of the snake scale-like surface are measured (Fig. 3 and Movies S2 to S5, Supplementary information). As shown in Fig. 3(a), the sample is first tilted 30° along the positive direction, droplets (about 20 µL) are randomly added at different locations, all the droplets instantaneously rolling off the as-prepared surface along the positive direction. Then, the sample turns 180° to the negative direction and it still tilted at 30°. All the added droplets are adhered on it. The motion of water flowing along the positive and negative directions is also studied when the as-prepared surface is tilted at the same angle. Under the action of gravity force, the water flow is accelerated at the moment leaving the syringe and falls to the as-prepared surface. In the experiment, the surface is tilted 30°. Figure 3(b) shows the motion of water flow on the anisotropic surface at different time. Water flows smoothly along the positive direction of the superhydrophobic surface. Under the same conditions, only when the water accumulates and the gravitational potential energy exceeds the adhesion, the water begins to flow along the negative direction of the superhydrophobic surface. Moreover, when the gravitational potential energy drops smaller than the adhesion force by lowering the height of water flow, instead of flowing down along the negative direction of the as-prepared surface, most of the water flow is guided horizontally to both sides by the surface until it exceeds the superhydrophobic surface boundary. More details of the droplets and water flow moving along the two directions are shown in Movies S2 to S5. In these Movies, it is easy to observe the difference between the droplets/flow sliding along the positive and negative directions of the as-prepared surface. The experimental result shows that the adhesion of the liquid sliding against the positive direction is larger than that along the positive direction. Therefore, it can be concluded that different droplet transportation paths can be achieved by using the snake scale-like three-level hierarchical micro/nanostructures to control the water-sliding directivity. Furthermore, it needs to be stressed that droplet transportation just represents one function, the surface with such an ability can be easily extended to other microstructure-dependent functional applications, such as pipeline transportation, vehicle acceleration, and other fluidic devices.
Figure 3.
From the above experimental results, it can be seen that the hierarchies of surface micro/nanostructures (three-level hierarchical snake scale-like micro/nanostructures) and suitable arrangement of the micro/nanostructures (tilted cross stacked arrangement) are important for the smart wetting performance, which can be explained as follows. As a three-level hierarchical structure, the snake scale-like structure consists of large snake scale structures in sub-millimeter scale and inclined cone-shaped structures in microscale, decorated with nanoparticles (Fig. 4). First of all, at the nanoscale (Fig. 4(a)), pulsed laser ablation produces active magnetite (Fe3O4−σ with 0<σ<1) on the surface of stainless steel, which has been identified as an environment capable of dissociating and absorbing carbon dioxide
Figure 4.
where
Moreover, based on theoretical analyses, the rolling movement of water droplets along the positive and negative directions of the snake scale surface under the action of gravity force is simulated. Simulation of the flowfield is performed using a VOF method with ANSYS Fluent, which is a numerical technique used to track the fluid-fluid interface in computational fluid dynamics
Figure 5.
Based on both the excellent superhydrophobicity and high directional performance of the snake scale-like structure surface, it is highly expected that coupling this structure with ship surfaces to form a “ship skin” could further realize directional reducing/increasing friction. The dynamic response between the solid and liquid interfaces under continuous water flow is studied. In particular, stainless steel plates textured with snake scale-like structures are designed as skins covered both sides of a ship model to study the directional movement, the water circulation system provides a continuous water flow, and friction force occurs when the surface of the ship moves under the continuous water flow (Fig. 6(a)). As shown in Fig. 6(b) and Movie S8 (see Supplementary information), the ship moves rapidly under the continuous water flow along the positive direction of the as-prepared surface, which is mostly attributed to the directional superhydrophobicity caused by the inclined hierarchical snake scale-like structures. As the water flow is along the positive direction, it is difficult for the water to enter the grooves because of the existence of the scales and the inclined grooves. Additionally, the moving states of the ship can be manipulated by rotating the ship 180 degrees (Fig. 6(c)). The results show that when other conditions are the same as that before the ship rotates, the ship hardly moves with the flow of water, it is because the friction force of the as-prepared surface in the negative direction is larger than that in the positive direction, and the air pockets at the interface are broken by the water flow, which causes the increase of surface adhesion force, as explained before. The snapshots of the movement of the ship confirm that the directional superhydrophobic behaviors are achieved by the snake scale-like structures fabricated by the laser processing.
Figure 6.
Conclusions
In conclusion, we present a novel bionic snake scale-like three-level hierarchical micro/nanostructured surface to realize superhydrophobicity and directional water sliding. To demonstrate the unique directional superhydrophobicity controlling, a stainless steel surface with snake scale-like three-level hierarchical micro/nanostructures is fabricated by laser ablation. Experimental results reveal that the CA can be achieved as high as 159°. Moreover, the adhesion force and the SA show strong dependence on the direction of the structures of the surface, giving the possibility of controllable superhydrophobic states along the positive and negative directions. Based on these unique properties, a “ship skin” for directional movement study is proposed. This work can provide new understandings toward solving the problems of superhydrophobic surfaces with directional wettability, and control the water mobility for a wide range of potential applications, such as water harvesting, droplet manipulation, pipeline transportation, and vehicle acceleration.
References
[1] L Feng, S Li, Y Li, H Li, L Zhang et al. Super-hydrophobic surfaces: from natural to artificial. Adv Mater, 14, 1857-1860(2002).
[2] XJ Feng, L Jiang. Design and creation of superwetting/antiwetting surfaces. Adv Mater, 18, 3063-3078(2006).
[3] V Zorba, E Stratakis, M Barberoglou, E Spanakis, P Tzanetakis et al. Biomimetic artificial surfaces quantitatively reproduce the water repellency of a lotus leaf. Adv Mater, 20, 4049-4054(2008).
[4] C Sanchez, H Arribart, MMG Guille. Biomimetism and bioinspiration as tools for the design of innovative materials and systems. Nat Mater, 4, 277-288(2005).
[5] XF Gao, L Jiang. Water-repellent legs of water striders. Nature, 432, 36(2004).
[6] YM Zheng, H Bai, ZB Huang, XL Tian, FQ Nie et al. Directional water collection on wetted spider silk. Nature, 463, 640-643(2010).
[7] DS Zhang, B Ranjan, T Tanaka, K Sugioka. Carbonized hybrid micro/nanostructured metasurfaces produced by femtosecond laser ablation in organic solvents for biomimetic antireflective surfaces. ACS Appl Nano Mater, 3, 1855-1871(2020).
[8] S Lou, XM Guo, TX Fan, D Zhang. Butterflies: inspiration for solar cells and sunlight water-splitting catalysts. Energy Environ Sci, 5, 9195-9216(2012).
[9] AJ Parnell, JE Bradford, EV Curran, AL Washington, G Adams et al. Wing scale ultrastructure underlying convergent and divergent iridescent colours in mimetic
[10] M Spinner, SN Gorb, A Balmert, H Bleckmann, G Westhoff. Non-contaminating camouflage: multifunctional skin microornamentation in the west african gaboon viper (
[11] L Zheng, YH Zhong, YH Gao, JY Li, ZH Zhang et al. Coupling effect of morphology and mechanical properties contributes to the tribological behaviors of snake scales. J Bionic Eng, 15, 481-493(2018).
[12] P Ball. Engineering shark skin and other solutions. Nature, 400, 507-509(1999).
[13] Y Lu, S Sathasivam, JL Song, CR Crick, CJ Carmalt et al. Robust self-cleaning surfaces that function when exposed to either air or oil. Science, 347, 1132-1135(2015).
[14] DM Zang, RW Zhu, W Zhang, XQ Yu, L Lin et al. Corrosion-resistant superhydrophobic coatings on mg alloy surfaces inspired by lotus seedpod. Adv Funct Mater, 27, 1605446(2017).
[15] FZ Chen, Y Lu, X Liu, JL Song, GJ He et al. Table salt as a template to prepare reusable porous PVDF–MWCNT foam for separation of immiscible oils/organic solvents and corrosive aqueous solutions. Adv Funct Mater, 27, 1702926(2017).
[16] K Golovin, A Dhyani, MD Thouless, A Tuteja. Low-interfacial toughness materials for effective large-scale deicing. Science, 364, 371-375(2019).
[17] YK Lai, JY Huang, ZQ Cui, MZ Ge, KQ Zhang et al. Recent advances in TiO2‐based nanostructured surfaces with controllable wettability and adhesion. Small, 12, 2203-2224(2016).
[18] YB Liu, HM Gu, Y Jia, J Liu, H Zhang et al. Design and preparation of biomimetic polydimethylsiloxane (PDMS) films with superhydrophobic, self-healing and drag reduction properties via replication of shark skin and SI-ATRP. Chem Eng J, 356, 318-328(2019).
[19] AY Zhuang, RJ Liao, Y Lu, SC Dixon, A Jiamprasertboon et al. Transforming a simple commercial glue into highly robust superhydrophobic surfaces via aerosol-assisted chemical vapor deposition. ACS Appl Mater Interfaces, 9, 42327-42335(2017).
[20] YZ Zhu, JL Wang, F Zhang, SJ Gao, AQ Wang et al. Zwitterionic nanohydrogel grafted PVDF membranes with comprehensive antifouling property and superior cycle stability for oil‐in‐water emulsion separation. Adv Funct Mater, 28, 1804121(2018).
[21] K Ellinas, M Chatzipetrou, I Zergioti, A Tserepi, E Gogolides. Superamphiphobic polymeric surfaces sustaining ultrahigh impact pressures of aqueous high‐ and low‐surface‐tension mixtures, tested with laser‐induced forward transfer of drops. Adv Mater, 27, 2231-2235(2015).
[22] M Tang, MH Hong, YS Choo, Z Tang, DHC Chua. Super-hydrophobic transparent surface by femtosecond laser micro-patterned catalyst thin film for carbon nanotube cluster growth. Appl Phys A, 101, 503-508(2010).
[23] M Tang, V Shim, ZY Pan, YS Choo, MH Hong. Laser ablation of metal substrates for super-hydrophobic effect. J Laser Micro/Nanoeng, 6, 6-9(2011).
[24] R Zhou, SD Lin, F Shen, SY Khew, MH Hong. A universal copper mesh with on-demand wettability fabricated by pulsed laser ablation for oil/water separation. Surf Coat Technol, 348, 73-80(2018).
[25] HP Yan, MRBA Rashid, SY Khew, FP Li, MH Hong. Wettability transition of laser textured brass surfaces inside different mediums. Appl Surf Sci, 427, 369-375(2018).
[26] DH Wang, QQ Sun, MJ Hokkanen, CL Zhang, FY Lin et al. Design of robust superhydrophobic surfaces. Nature, 582, 55-59(2020).
[27] WT Cao, W Feng, YY Jiang, C Ma, ZF Zhou et al. Two-dimensional MXene-reinforced robust surface superhydrophobicity with self-cleaning and photothermal-actuating binary effects. Mater Horiz, 6, 1057-1065(2019).
[28] JL Song, FS Guan, WH Pan, ZA Liu, J Sun et al. Droplet-based self-propelled miniboat. Adv Funct Mater, 30, 1910778(2020).
[29] JN Wang, YQ Liu, YL Zhang, J Feng, H Wang et al. Wearable superhydrophobic elastomer skin with switchable wettability. Adv Funct Mater, 28, 1800625(2018).
[30] I Paradisanos, C Fotakis, SH Anastasiadis, E Stratakis. Gradient induced liquid motion on laser structured black Si surfaces. Appl Phys Lett, 107, 111603(2015).
[31] SV Kirner, U Hermens, A Mimidis, E Skoulas, C Florian et al. Mimicking bug-like surface structures and their fluid transport produced by ultrashort laser pulse irradiation of steel. Appl Phys A, 123, 754(2017).
[32] D Wu, Z Zhang, YY Zhang, YL Jiao, SJ Jiang et al. High-performance unidirectional manipulation of microdroplets by horizontal vibration on femtosecond laser-induced slant microwall arrays. Adv Mater, 32, 2005039(2020).
[33] XQ Liu, BF Bai, QD Chen, HB Sun. Etching-assisted femtosecond laser modification of hard materials. Opto-Electron Adv, 2, 190021(2019).
[34] WZ Ma, DS Zhao, RM Liu, TS Wang, Q Yuan et al. Observation and optimization of 2 μm mode-locked pulses in all-fiber net anomalous dispersion laser cavity. Opto-Electron Adv, 3, 200001(2020).
[35] Y Li, MH Hong. Parallel laser micro/Nano-processing for functional device fabrication. Laser Photonics Rev, 14, 1900062(2020).
[36] N Livakas, E Skoulas, E Stratakis. Omnidirectional iridescence via cylindrically-polarized femtosecond laser processing. Opto-Electron Adv, 3, 190035(2020).
[37] YC Jia, SX Wang, F Chen. Femtosecond laser direct writing of flexibly configured waveguide geometries in optical crystals: fabrication and application. Opto-Electron Adv, 3, 190042(2020).
[38] E Stratakis, J Bonse, J Heitz, J Siegel, GD Tsibidis et al. Laser engineering of biomimetic surfaces. Mat Sci Eng: R: Rep, 141, 100562(2020).
[39] RN Wenzel. Resistance of solid surfaces to wetting by water. Ind Eng Chem, 28, 988-994(1936).
[40] Y Tamaura, M Tahata. Complete reduction of carbon dioxide to carbon using cation-excess magnetite. Nature, 346, 255-256(1990).
[41] CL Zhang, S Li, LJ Wang, TH Wu, SY Peng. Studies on the decomposing carbon dioxide into carbon with oxygen-deficient magnetite: II. The effects of properties of magnetite on activity of decomposition CO2 and mechanism of the reaction. Mater Chem Phys, 62, 52-61(2000).
[42] CL Zhang, S Li, LJ Wang, TH Wu, SY Peng. Studies on the decomposition of carbon dioxide into carbon with oxygen-deficient magnetite: I. Preparation, characterization of magnetite, and its activity of decomposing carbon dioxide. Mater Chem Phys, 62, 44-51(2000).
[43] KKS Lau, J Bico, KBK Teo, M Chhowalla, GAJ Amaratunga et al. Superhydrophobic carbon nanotube forests. Nano Lett, 3, 1701-1705(2003).
[44] ABD Cassie, S Baxter. Wettability of porous surfaces. Trans Faraday Soc, 40, 546-551(1944).
[45] Molecular Theory of Capillarity (Clarendon Press, Oxford, Oxfordshire, 1982).
[46] VT Nguyen, WG Park. A free surface flow solver for complex three-dimensional water impact problems based on the VOF method. Int J Numer Methods Fluids, 82, 3-34(2016).
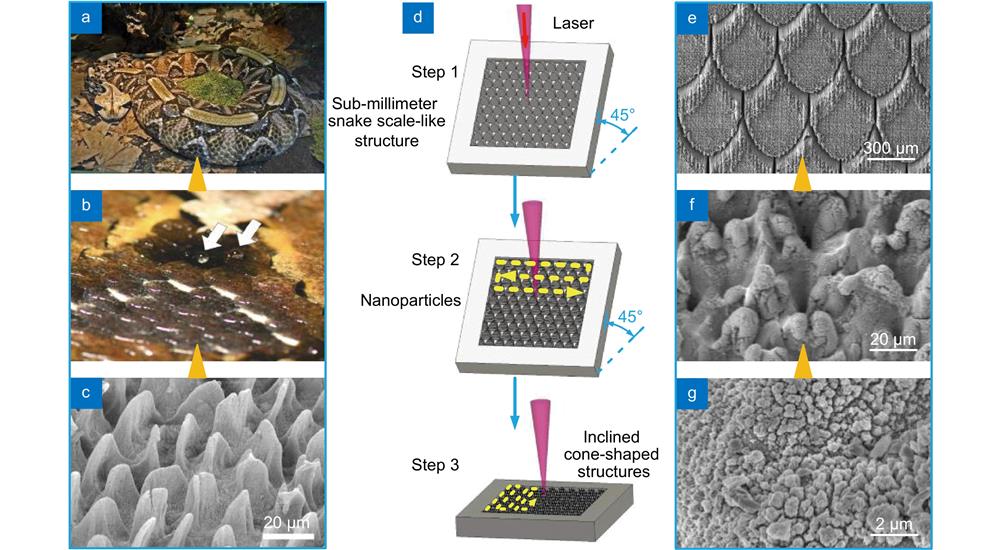
Set citation alerts for the article
Please enter your email address