Xinlong Liao, Boyong Su, Shuo Xu, Guoran Hua, Heng Wang, Yupeng Cao. Flow Law of Plastic Deformation of TC4 Titanium Alloy by Laser Shock Peening[J]. Chinese Journal of Lasers, 2023, 50(16): 1602206

Search by keywords or author
- Chinese Journal of Lasers
- Vol. 50, Issue 16, 1602206 (2023)

Fig. 1. Schematic of LSP treatment

Fig. 2. Three dimensional finite element model after mesh division
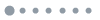
Fig. 3. Pressure-time history curves of laser shock wave
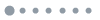
Fig. 4. Deformation diagram extracted on center line
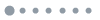
Fig. 5. Volume calculation flowchart
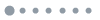
Fig. 6. Simulation result of deformation when laser power density is 3.02 GW/cm2. (a) Cloud diagram of deformation; (b) cloud diagram of deformation section; (c) detailed surface deformation distribution
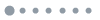
Fig. 7. Simulation results of surface residual stress when laser power density is 3.02 GW/cm2. (a) Cloud diagram of residual stress; (b) detailed distribution of residual stress
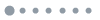
Fig. 8. Distributions of surface deformation and surface residual stress under different laser power densities. (a) Surface deformation distribution; (b) surface residual stress distribution
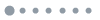
Fig. 9. Laser shock test results. (a) Micro-indention on specimen surface; (b) topography of surface micro-indention; (c) detailed surface profiles; (d) micro-indention depth, convex deformation height, and residual stress versus laser power density
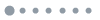
Fig. 10. Surface micro-indention depth versus laser power density
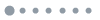
Fig. 11. Detailed deformation distributions at different depths when laser power density is 3.02 GW/cm2
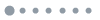
Fig. 12. Fitting curves. (a) Surface micro-indention deformation; (b) internal convex deformation
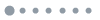
Fig. 13. Distributions of plastic deformation volume. (a) Trend in volume of each part; (b) proportion of volume of each part
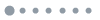
Fig. 14. TEM images of TC4 titanium alloy surface layer before and after LSP. (a) Position at 10 μm below surface before LSP; (b) micro-indention and (c) annular convex deformation areas at 10 μm below surface after LSP; (d) internal convex deformation area at 1 mm below surface after LSP
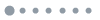
Fig. 15. Particle size distribution diagrams of TC4 titanium alloy before and after LSP. (a) Position at 10 μm below surface before LSP; (b) micro-indention and (c) annular convex deformation areas at 10 μm below surface after LSP; (d) internal convex deformation area at 1 mm below surface after LSP
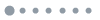
Fig. 16. Laser impact surface morphology when spot overlapping rate is 0
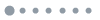
Fig. 17. Laser impact surface morphology when spot overlapping rate is 33%
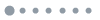
Fig. 18. Laser impact surface morphology when spot overlapping rate is 50%
|
Table 1. LSP parameters
|
Table 2. Basic material parameters of TC4 titanium alloy

Set citation alerts for the article
Please enter your email address