Lingyu Sun, Changchao Liu, Mingshun Jiang, Lei Zhang, Faye Zhang, Qingmei Sui, Lei Jia. Fatigue Crack Prediction Method for Aluminum Alloy Based on Fiber Bragg Grating Array[J]. Chinese Journal of Lasers, 2021, 48(13): 1306003

Search by keywords or author
- Chinese Journal of Lasers
- Vol. 48, Issue 13, 1306003 (2021)
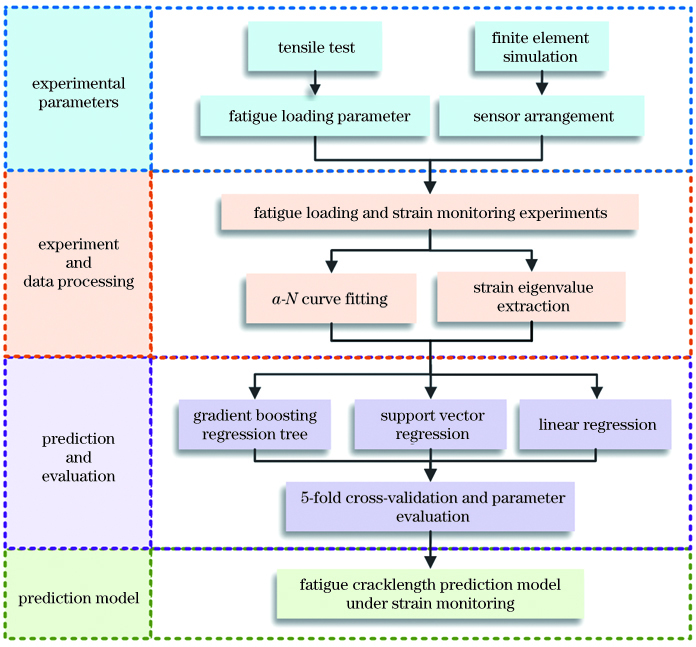
Fig. 1. Flow chart of fatigue crack prediction based on FBG
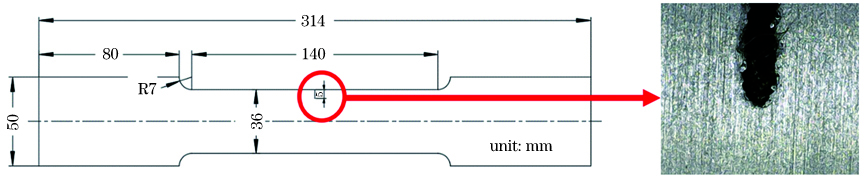
Fig. 2. Component size diagram
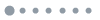
Fig. 3. Strain field nephograms at different stages of crack propagation. (a) Crack initiation; (b) initial crack propagation; (c) steady crack propagation; (d) crack approaching failure
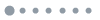
Fig. 4. Fatigue crack growth monitoring experimental system based on FBG
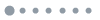
Fig. 5. Overall schematic diagram of FBG demodulation system
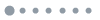
Fig. 6. Fatigue tensile results of samples 1--4
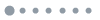
Fig. 7. Schematic diagram of FBG sensor array
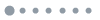
Fig. 8. Actual pasting position of FBG sensor array
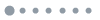
Fig. 9. Fitting result of fatigue extension a-N curve
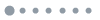
Fig. 10. Wavelength change measured by sensor FBG1
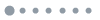
Fig. 11. Relationship between peak-to-peak wavelength and cyclic loading times
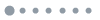
Fig. 12. Relationship between peak-to-peak wavelength and crack length
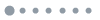
Fig. 13. Tensile results of aluminum alloy sample 5
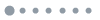
Fig. 14. Principle diagram of GBRT
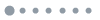
Fig. 15. Principle of 5-fold cross-verification
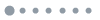
Fig. 16. Prediction result of GBRT algorithm
|
Table 1. Material properties of simulation experiment
|
Table 2. Results of fatigue tensile test
|
Table 3. Evaluation indexes of fitting curve
|
Table 4. 5-fold cross-validation results of GBRT model
|
Table 5. Regression performance evaluation results of GBRT model
|
Table 6. Regression performance evaluation results of model
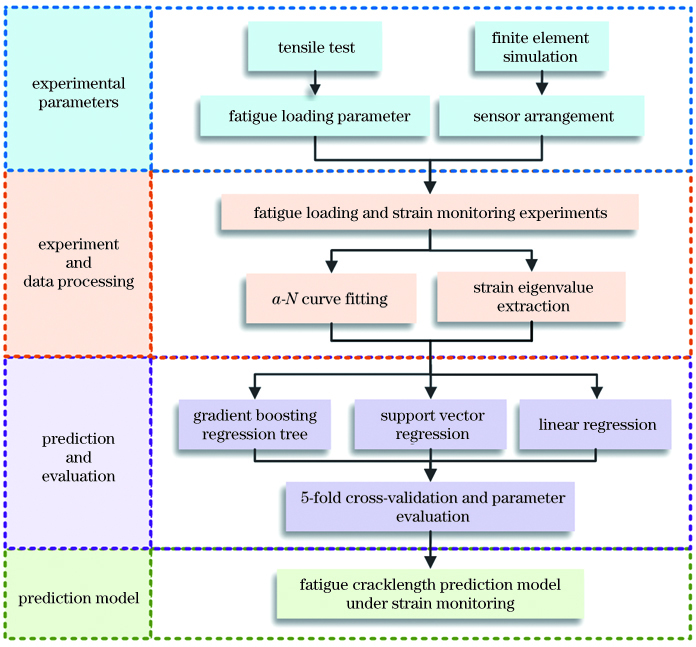
Set citation alerts for the article
Please enter your email address