Yang ZHANG, Yipin SU, Yongkang LU, Junqing LI, Qihang CHEN, Ruidi YAN, Wei LIU. Prediction and compensation of thermal offset in tooling ERS points under non-uniform temperature fields (invited)[J]. Infrared and Laser Engineering, 2025, 54(3): 20240623

Search by keywords or author
- Infrared and Laser Engineering
- Vol. 54, Issue 3, 20240623 (2025)

Fig. 1. The overall framework for the prediction and compensation of thermal offset in tooling ERS points under non-uniform temperature fields

Fig. 2. Logic diagram for determining the global trend of the tooling temperature field using LOOCV
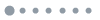
Fig. 3. Schematic of global temperature field reconstruction
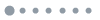
Fig. 4. Logic diagram of the approach for selecting virtual temperature measurement points based on multi-objective optimization
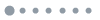
Fig. 5. Flowchart of the adaptive dynamic local search prairie dog optimization
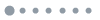
Fig. 6. Comparison of temperature field reconstruction by GPR-GTFR and Kriging methods
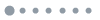
Fig. 7. Schematic of the model simplification process
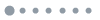
Fig. 8. Schematic of model meshing and constraint settings
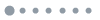
Fig. 9. Experimental configuration
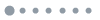
Fig. 10. Experimental scenario
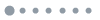
Fig. 11. Temperature sensor data recording curve
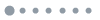
Fig. 12. Prediction curves of thermal offset for ERS points under uniform temperature change
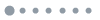
Fig. 13. Prediction curves of thermal offset for a ERS point under varying temperature changes
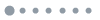
Fig. 14. Station transfer errors before and after compensation
|
Table 1. Material properties of the tooling
|
Table 2. Prediction error analysis of thermal offset for reference points (Unit: mm)
|
Table 3. RMSE comparison of station transfer errors in X , Y , and Z directions before and after compensation (Unit: mm)

Set citation alerts for the article
Please enter your email address