Exian Liu, Jianjun Liu, "Quasiperiodic photonic crystal fiber [Invited]," Chin. Opt. Lett. 21, 060603 (2023)

Search by keywords or author
- Chinese Optics Letters
- Vol. 21, Issue 6, 060603 (2023)
![(a) Five-fold Penrose lattice tiling pattern[5]. (b) Diffraction pattern of the five-fold Penrose-type PQ structure[5]. (c) 1D Fibonacci sequence generated by the 2D PQ lattice using the cut-and-project method[5]. (d) Fabricated silica-based twelve-fold symmetric quasicrystals[23]. (e) Multiple diffracted beams from the entrance face of the twelve-fold symmetric quasicrystals[23]. (f) and (g) Fabricated Si-based twelve-fold PQ and Sunflower-type PQ structures by E-beam lithography system[64].](/richHtml/col/2023/21/6/060603/img_001.jpg)
Fig. 1. (a) Five-fold Penrose lattice tiling pattern[5]. (b) Diffraction pattern of the five-fold Penrose-type PQ structure[5]. (c) 1D Fibonacci sequence generated by the 2D PQ lattice using the cut-and-project method[5]. (d) Fabricated silica-based twelve-fold symmetric quasicrystals[23]. (e) Multiple diffracted beams from the entrance face of the twelve-fold symmetric quasicrystals[23]. (f) and (g) Fabricated Si-based twelve-fold PQ and Sunflower-type PQ structures by E-beam lithography system[64].
![Upper circular diagram showing the potential technological applications with the optical properties optimized using the structure and material manipulation based on a PQF. The bottom arrow indicates the PQF evolution from the first fabricated PCF[67] to the first reported PQ structure[16], to the first proposed PQF[68], to the hollow-core PQF[72], to the Ge-doped PQF[99], to the OAM-supported PQF[95], and to the PQF-based sensor[96].](/richHtml/col/2023/21/6/060603/img_002.jpg)
Fig. 2. Upper circular diagram showing the potential technological applications with the optical properties optimized using the structure and material manipulation based on a PQF. The bottom arrow indicates the PQF evolution from the first fabricated PCF[67] to the first reported PQ structure[16], to the first proposed PQF[68], to the hollow-core PQF[72], to the Ge-doped PQF[99], to the OAM-supported PQF[95], and to the PQF-based sensor[96].
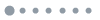
Fig. 3. The upper row shows the Stampfli-type PQF. (a) The first-order PQF, (b) the second-order PQF, and (c) the second-order PQF with a π/6 rotation of the near-core ring of the air holes. The middle row shows the Penrose-type PQF. (d) The eight-fold PQF, (e) the ten-fold PQF, and (f) the twelve-fold PQF. The bottom row shows the Sunflower-type PQF. (g) The six-fold PQF, (h) the seven-fold PQF, and (i) the eight-fold PQF.
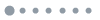
Fig. 4. (a) Index-guiding solid-core PQF. (b) The air-guiding hollow-core PQF.
![(a) Phase diagram of the second-order mode for the eight-air-hole-ring square and the triangular PCFs[100]. (b) The normalized V parameter for the Stampfli-type PQF[68]. (c) The normalized V parameter for the Sunflower-type PQF[85].](/Images/icon/loading.gif)
Fig. 5. (a) Phase diagram of the second-order mode for the eight-air-hole-ring square and the triangular PCFs[100]. (b) The normalized V parameter for the Stampfli-type PQF[68]. (c) The normalized V parameter for the Sunflower-type PQF[85].
![Negative dispersion for the different PQF designs: (a) the small outer core[69], (b) the large outer core[110], and (c) the doped inner core[111]. (d) The normal dispersion for the Ge-doped PQF design[73]: the electric field distribution in the inner core and outer core at 1.06 µm and the obtained normal dispersion.](/Images/icon/loading.gif)
Fig. 6. Negative dispersion for the different PQF designs: (a) the small outer core[69], (b) the large outer core[110], and (c) the doped inner core[111]. (d) The normal dispersion for the Ge-doped PQF design[73]: the electric field distribution in the inner core and outer core at 1.06 µm and the obtained normal dispersion.
![High birefringence silica-based PQF at 1.55 µm obtained by breaking the structure symmetry. (a) The Penrose-type PQF with a birefringence of 1.4207 × 10-2[114]. (b) The Stampfli-type PQF with a birefringence of 3.86 × 10-2[71].](/Images/icon/loading.gif)
Fig. 7. High birefringence silica-based PQF at 1.55 µm obtained by breaking the structure symmetry. (a) The Penrose-type PQF with a birefringence of 1.4207 × 10-2[114]. (b) The Stampfli-type PQF with a birefringence of 3.86 × 10-2[71].
![(a)–(d) Large mode area PQF and (e)–(f) highly nonlinear PQF. (a) The large-core PQF[116]. (b) The Yb-doped large pitch PQF[75]. (c) The gradient-diameter Sunflower-type PQF [with a large effective mode area and a low bending loss shown in (d)][91]. (e) The twin bow-tie silica-based PQF[76]. (f) The annular core Stampfli-type PQF[109]. (g) The tellurite elliptical core PQF [with high nonlinearity shown in (h)][117].](/Images/icon/loading.gif)
Fig. 8. (a)–(d) Large mode area PQF and (e)–(f) highly nonlinear PQF. (a) The large-core PQF[116]. (b) The Yb-doped large pitch PQF[75]. (c) The gradient-diameter Sunflower-type PQF [with a large effective mode area and a low bending loss shown in (d)][91]. (e) The twin bow-tie silica-based PQF[76]. (f) The annular core Stampfli-type PQF[109]. (g) The tellurite elliptical core PQF [with high nonlinearity shown in (h)][117].
![OAM-supported PQF. (a) The dual-cladding Stampfli-type PQF, and the electric field distribution and the helix phase[95]. (b) The dual-core dispersion compensation of the Sunflower-type PQF, and the electric field distribution[122]. (c) The GeO2-doped Sunflower-type PQF, and the electric field distribution[123]. (d) The GeO2-doped Sunflower-type PQF, and the electric field distribution and the helix phase[124].](/Images/icon/loading.gif)
Fig. 9. OAM-supported PQF. (a) The dual-cladding Stampfli-type PQF, and the electric field distribution and the helix phase[95]. (b) The dual-core dispersion compensation of the Sunflower-type PQF, and the electric field distribution[122]. (c) The GeO2-doped Sunflower-type PQF, and the electric field distribution[123]. (d) The GeO2-doped Sunflower-type PQF, and the electric field distribution and the helix phase[124].
![(a) The SEM image of the fabricated ring-core PQF[88]. (b) The measured CCD images of the OAM with l = 1 (top) and l = 2 (bottom) output signals and with (left) intensities and (right) phases.](/Images/icon/loading.gif)
Fig. 10. (a) The SEM image of the fabricated ring-core PQF[88]. (b) The measured CCD images of the OAM with l = 1 (top) and l = 2 (bottom) output signals and with (left) intensities and (right) phases.
![PQF-based sensor. (a) The dual-core PQF (left), and the interference spectrum used for sensing the external temperature (right)[126].(b) The mechanism of the surface plasmon resonance PQF sensor. When the sensor is put in the target analyte, the coupling loss peak shifts. (c) The Stampfli-type PQF with a surface-coated ITO layer[128]. (d) The Penrose-type PQF with a D-shaped analyte channel[89]. (e) The U-shaped Stampfli-type PQF[90]. (f) The hybrid-size air hole PQF with a micro D-shaped analyte channel[129].](/Images/icon/loading.gif)
Fig. 11. PQF-based sensor. (a) The dual-core PQF (left), and the interference spectrum used for sensing the external temperature (right)[126].(b) The mechanism of the surface plasmon resonance PQF sensor. When the sensor is put in the target analyte, the coupling loss peak shifts. (c) The Stampfli-type PQF with a surface-coated ITO layer[128]. (d) The Penrose-type PQF with a D-shaped analyte channel[89]. (e) The U-shaped Stampfli-type PQF[90]. (f) The hybrid-size air hole PQF with a micro D-shaped analyte channel[129].
![(a) Profile of the OAM-SPR photonic quasi-crystal fiber sensor[131]. The figure outlined with the red rectangular dotted line shows the coupling field distribution. (b) Basic setup of the proposed fiber sensor for refractive index sensing.](/Images/icon/loading.gif)
Fig. 12. (a) Profile of the OAM-SPR photonic quasi-crystal fiber sensor[131]. The figure outlined with the red rectangular dotted line shows the coupling field distribution. (b) Basic setup of the proposed fiber sensor for refractive index sensing.
![Supercontinuum generation based on the highly nonlinear PQF. (a) The silica-based Sunflower-type PQFs with a defect-core[132]. (b) The As2Se3-based Stampfli-type PQF[83]. (c) The Ge15Sb15Se70-based Sunflower-type PQF[135]. (d) The Ge11.5As24Se64.5-based Stampfli-type PQF[82].](/Images/icon/loading.gif)
Fig. 13. Supercontinuum generation based on the highly nonlinear PQF. (a) The silica-based Sunflower-type PQFs with a defect-core[132]. (b) The As2Se3-based Stampfli-type PQF[83]. (c) The Ge15Sb15Se70-based Sunflower-type PQF[135]. (d) The Ge11.5As24Se64.5-based Stampfli-type PQF[82].
![(a)–(d) Cross-sectional images of the sol–gel-derived microstructure fibers[139] and the 3D printing of PCF[141]. (a) The endlessly single-mode design. (b) The high delta, highly nonlinear fiber. (c) The dual-core structure. (d) The circular-core PCF. (e) The PCF polarization beam splitter enabled by the 3D printing of the PCF designs. A beam with an arbitrary polarization (yellow beam) is split into its horizontal (red beam) and vertical (green beam) polarization components. (f) The helically twisted coreless PCF. (g) The PBG hollow-core PCF. (h) The anti-resonant hollow-core PCF. (i) The fractal ring-core PCF.](/Images/icon/loading.gif)
Fig. 14. (a)–(d) Cross-sectional images of the sol–gel-derived microstructure fibers[139] and the 3D printing of PCF[141]. (a) The endlessly single-mode design. (b) The high delta, highly nonlinear fiber. (c) The dual-core structure. (d) The circular-core PCF. (e) The PCF polarization beam splitter enabled by the 3D printing of the PCF designs. A beam with an arbitrary polarization (yellow beam) is split into its horizontal (red beam) and vertical (green beam) polarization components. (f) The helically twisted coreless PCF. (g) The PBG hollow-core PCF. (h) The anti-resonant hollow-core PCF. (i) The fractal ring-core PCF.
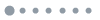
Fig. 15. Description of a potential preparation process of a PQF using the sol–gel method.
|
Table 1. Flattened and Near-Zero Dispersion Based on the PQF Structure
|
Table 2. Performance Parameters of the PQF-Based Sensors
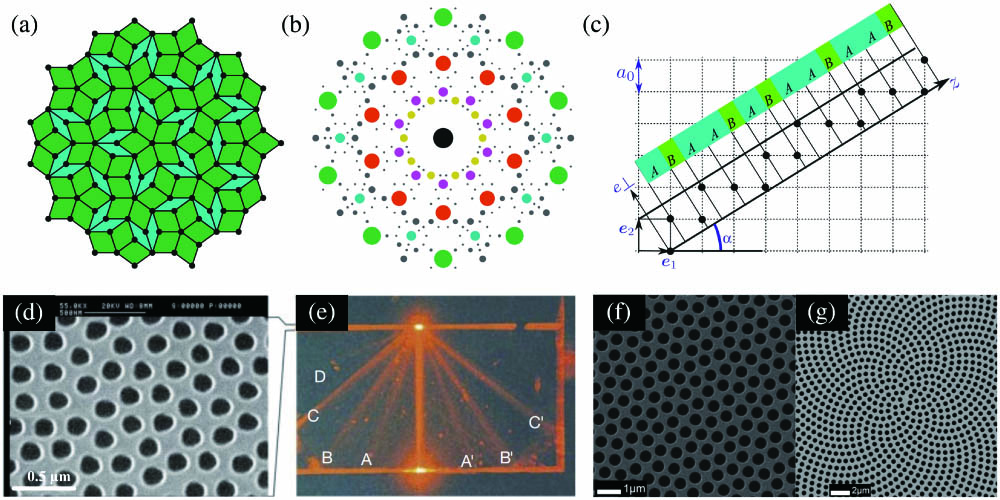
Set citation alerts for the article
Please enter your email address