
- Journal of Inorganic Materials
- Vol. 35, Issue 6, 729 (2020)
Abstract
Keywords
As a core component, Ag-based electrical contact is widely used in the low-voltage switching devices, such as contactors, circuit breakers, and relays[
Recently, MAX phase materials (chemical formula of Mn+1AXn, where M is early transition metal, A is mainly group A element, X is C or N), with combined properties of both metal and ceramic, received great attention from academia and industry[
There are two key points need to be paid attention in the studying of Ag/TAC composites. First, the impure phases affect the density, structure, interface, and properties of the composites. Thus, preparing high-purity Ti2AlC powder is particularly important before studying the Ag/TAC composite electrical contact materials. The synthesis of Ti2AlC bulk and powder by using hot pressing (HP)[
The purpose of this work is to synthesize the high-purity Ti2AlC powder by using pressureless technique, and study the effect of process parameters on the purity and microstructure of Ti2AlC. Then the wettability, microstructure, mechanical properties, electrical properties, and arc erosion resistance of Ag/TAC composites were studied, and its application potential were also discussed.
1 Experimental
1.1 Synthesis of Ti2AlC powder
Powders of TiC (~5 μm, 99.0%), Ti (~50 μm, 99.99%), and Al (~50 μm, 99.7%) were weighed according to stoichiometric ratio and then were totally homogenized in the three-dimensional mixer (Turbula T2F, WAB, Switzerland) for 24 h. Mixture powders were directly heated to the setting temperature for 1 h at a heating rate of 10 ℃/min under the protection of flowing Ar gas (99.999% purity).
1.2 Wetting test of Ag/Ti2AlC
Ti2AlC bulk (a relative density of 99.6%) was prepared by using SPS (heated to 1300 ℃ at a heating rate of 50 ℃/min and held for 20 min with a applied pressure of 50 MPa). The prepared composite bulk was cut into small disc (10 mm diameter) with a polished surface. Ag rod (99.99% purity, 2 mm in diameter, 2 mm in length) was placed with the disc into the high temperature contact instrument (OCA25HTV, Dataphysics, Germany), then was heated to 1120 ℃ for 10 min at a heating rate of 8 ℃/min. The wetting angle data of molten Ag on the surface of Ti2AlC were recorded by the software (SCA20).
1.3 Preparation of Ag/Ti2AlC composite
Powders of Ag (~10 μm, 99.99%) and Ti2AlC (~20 μm, 99.2%) were weighed with a mass ratio of 9:1. Mixture powders were wet ball milled for 0.5 h with the medium of alcohol. Dried mixture were cold-pressed at 800 MPa into green body (15 mm in diameter, 3 mm in thickness). Samples were heated to 800 ℃ for 2 h in a tube furnace with a heating rate of 5 ℃/min.
1.4 Arc erosion experiment
Ag/TAC bulk was cut into the contacts (1.5 mm in thickness, 7 mm in diameter), then these contacts were welded with copper bases, finally were installed into a commercial contactor (CJX-50, China). The electric arc discharging experiment was carried out at the low voltage electrical apparatus test center of Shanghai Electrical Research Institute. The arc erosion resistance of Ag/TAC contacts were tested with the following experimental parameter (set according to the national standard GB14048.4-2010): AC-3 inductive load, 400 V voltage, 100 A circuit, 50 Hz coil frequency, 600 cycles/h operation frequency.
1.5 Characterizations
The phases were characterized by X-ray diffraction (XRD) (Bruker-AXS D8, Germany) with a scan rate of 10 (°)/min. The morphologies of Ti2AlC powder and Ag/10TAC composites were obtained by a field-emission scanning electron microscopy (FE-SEM) (Sirion 200, FEI/Fhilips, Netherlands), and their chemical component were tested and analyzed by the energy dispersed X-ray spectrometer (EDS) (AZtes X-MAX 80, Germany). The density of Ag/10TAC bulk was directly tested with the densimeter (DH-300, China, 0.001 g/cm3 accuracy). The hardness of Ag/10TAC composite was measured by the Vickers microhardness tester (FM-700, Japan, 1 kg pressure, holding time of 5 s). The resistance of Ag/10TAC bulk was obtained by using the instrument (METRAHIT 27 I, Germany, 0.001 mΩ accuracy), and then its resistivity was calculated according to the four probe principle. Mass loss of the Ag/TAC contact after arc erosion was obtained by using the electronic balance (BT25S, Sartorius, Germany, 0.01 mg accuracy). Area loss of the contact after arc erosion was calculated with the metallographic microscope analysis software (LAS V4.8, Leica, Germany).
2 Results and discussion
2.1 High-purity Ti2AlC powders
During the preparation of Ti2AlC, Al first melts due to its low melting point and provides a liquid environment for the subsequent reactions. Vaporization of Al at high temperature leads to the loss of Al in the raw materials. Therefore, appropriate increase of Al content is the premise to ensure the chemical reaction according to the stoichiometric ratio of raw powder. In Table 1, the content of TiC and Ti in the raw materials remains unchanged, excessive Al are added to the raw materials to study the effect of Al content on the purity of Ti2AlC powder.
Sample | Composition, | Purity/% |
---|---|---|
S1 | 1.05 | 77.5 |
S2 | 1.10 | 57.9 |
S3 | 1.15 | 41.4 |
S4 | 1.20 | 31.5 |
Table 1.
Molar ratio of raw material powder TiC/Ti/xAl
X-ray diffraction was carried out to identify the phase composition of the as-prepared Ti2AlC powder. As shown in Fig. 1, peaks of Ti2AlC were detected in all four samples, however, some impure phases like Ti3AlC2 and TiC were also detected in the final sample. Diffraction peak of the impure phase increases with the increase of the Al content in the raw materials. The purity of Ti2AlC in the four samples are calculated according to the integral area of the main peak of the main phase[
Figure .XRD patterns of samples with different Al contents
Based on the Sample S1, the contents of Ti and Al in the raw materials remain unchanged, while the content of C reduces gradually. Four samples (Table 2) were designed to study the effect of C-deficiency in the raw material on the purity of Ti2AlC powder. As shown in Fig. 2, XRD result shows that Ti3AlC2 and TiC phases are hardly detected in Sample S5, and the purity of Ti2AlC powder was calculated as 99.2% (Table 2), indicating that the C-deficiency in the raw materials facilitates the generation of more Ti2AlC phase. However, the further increase of C content in the raw material in turn leads to the decomposition of Ti2AlC into TiC and Ti-Al compound (Sample S6, S7). In addition, little Ti3AlC2 is also detected in the final samples. The purities of both Sample 6 and Sample 7 are less than 93%, which indicates that the severe shortage of C in the raw material deteriorates the purity of Ti2AlC powder.
Sample | Composition, | Purity/% |
---|---|---|
S1 | 1.00 | 77.5 |
S5 | 1.05 | 99.2 |
S6 | 1.10 | 92.3 |
S7 | 1.15 | 91.7 |
Table 2.
Molar ratio of raw material powder (2-x)TiC/xTi/1.05Al
Figure .XRD patterns of samples with different C contents
The morphologies of samples with different C contents are displayed in Fig. 3. The powders of Sample S1, S6 and S7 exhibit irregular shape and its surface were covered by many adherent particles with a small size of 0.2-0.8 μm (Fig. 3(a-b, e-h). It is reported that the existence of two M layers in every two A layers leads to the formation of layered crystal structure of 211MAX phase[
Figure .SEM images of samples with different C contents
Sintering temperature is another important factor for the phase transition and morphology evolution of the Ti2AlC powder during the synthesizing process. Raw powder with the composition of 0.95TiC/1.05Ti/1.05Al is heated to different temperatures, as shown in Table 3. XRD result shows that the final powder contains a large amount of TiC and Ti-Al compounds due to the insufficient reaction when synthestic temperature is below 1400 ℃ (Fig. 4). Once the temperature exceeds 1500 ℃, the synthesized Ti2AlC phase largely decomposes into TiC and Ti-Al compounds, and merely produces little Ti3AlC2. At 1400 ℃, the high-purity Ti2AlC is stable, and no impure phase is detected.
Sample | Temperature/℃ | Purity/% |
---|---|---|
S8 | 1200 | 16.3 |
S9 | 1300 | 35.7 |
S10 | 1400 | 99.2 |
S11 | 1500 | 81.8 |
Table 3.
Preparation of Ti2AlC powder from 0.95TiC/1.05Ti/1.05Al at different temperatures
In summary, appropriate increase of Al and slight reduction of C in the raw material facilitate the generation of Ti2AlC phase in the final powder. But excessively low and high temperature hinder the purity improvement of Ti2AlC powder. In order to obtain high-purity Ti2AlC powder, the optimal synthesis process parameters is concluded as: a raw powder with composition of 0.95TiC/1.05Ti/1.05Al, sintered at 1400 ℃ for 1 h under pressureless condition.
Figure .XRD patterns of 0.95TiC/1.05Ti/1.05Al sintered at different temperatures
2.2 Wetting behavior of Ag/Ti2AlC
In the process of heating, the contact angles and optical images of molten Ag on the Ti2AlC substrate are simultaneously recorded, as shown in Fig. 5. The poor wettability of Ag and Ti2AlC is observed at ~990 ℃ (a large contact angle of 154.6°). As temperature increases, Al atoms in Ti2AlC outward diffuse into Ag matrix, leading to the reactive wetting and hence the decrease of contact angle. When temperature rises to 1130 ℃, the contact angle stabilized at 14.1°, indicating that Ag well wets Ti2AlC. In the preparation of Ag/Ti2AlC composite, good wettability is beneficial to enhance the interface bonding between Ag and Ti2AlC, and reduce the aggregation of Ti2AlC particles. Good wettability also facilitates the viscosity improvement of the molten pool and the increases the resistance to splash of liquid Ag during the electric arc discharging.
Figure .Contact angles and optical images of Ag/Ti2AlC in the process of heating
2.3 Ag/Ti2AlC composite
XRD result of Ag/10wt%Ti2AlC (Ag/10TAC) composite is shown in Fig. 6. Except Ag and Ti2AlC, no other impure phase were detected. The SEM image of Ag/10TAC (Fig. 6(b)) shows the uniform microstructure of the composite, and the good bonding of the Ti2AlC with Ag matrix (Fig. 6(c)), which is attributed to the good wettability between the Ag and the Ti2AlC. The basic properties (density, relative density, hardness, resistivity) of Ag/10TAC composite are listed in Table 4. High relative density (~95.7%) and moderate hardness (96HV) provide good strength and machinability of the Ag/10TAC composite. Low resistivity (79.5 nΩ·m) facilitates the electric conducting of current and thus reduces contact resistivity and temperature rise of the Ag/10TAC contact.
Figure .XRD pattern of Ag/10TAC composite with insets showing (a) picture of the bulk, (b) microstructure of composite, and (c) the magnified SEM image
Density/ | Relative density/% | Hardness, HV | Resistivity/ |
---|---|---|---|
8.692 | 95.7% | 96 | 79.5 |
Table 4.
Basic properties of Ag/Ti2AlC composite
2.4 Arc erosion resistance of Ag/10TAC
Arc erosion resistance is an important index to evaluate the application potential of an electrical contact material. As shown in Fig. 7, after 5610 electric arc discharging cycles, the shape of Ag/10TAC contact remains well (inset of Fig. 7(a)). The erosion area of eroded contact surface accounts for 88.6% of the total contact area, but the mass loss is only 4.4wt%, indicating that Ag/10TAC has strong resistance to arc erosion. Fine thermal and low resistivity of Ti2AlC, good wettability between molten Ag and Ti2AlC, and the interdiffusion between Ag and Ti2AlC are responsible for the good contacting properties of the Ag/10TAC composite. After arc erosion, a few cracks, holes, and Ag spheres were observed on the surface of Ag/10TAC contact (Fig. 7(b)). The Ag matrix inside molten pool mainly exhibits cauliflower-shaped after arc erosion, as shown in inset of Fig. 7(c). In addition, some dark areas were observed on the contact surface (Fig. 7(b, d)), which mainly contains Ti, O, C, and little Al by EDS. The formation of these dark areas is attributed to the aggregation of the eroded Ti2AlC, which has been partially destroyed by high-temperature oxidation during electric arc discharging.
Figure .(a) Optical image of the Ag/10TAC contact after 5610 arc discharging cycles, with magnified SEM image in the inset; (b) SEM image of the contact surface morphology; (c) Morphology of the Ag molten pool, with magnified SEM image of cauliflower-shaped Ag particles in the inset; (d) Magnified SEM image of the aggregated eroded Ti2AlC (dark area in (b))
3 Conclusions
Pressureless synthesis was employed to study the effect of composition and sintering temperature on the purity and morphology of Ti2AlC powder. The structure and properties of the Ag/10TAC composite electrical contact material are investigated. Main conclusions are drawn as follows:
1) High-purity Ti2AlC powder (99.2%) is synthesized at 1400 ℃/h by using the raw powder with the starting composition of 0.95TiC/1.05Ti/1.05Al.
2) Contact angle decreases with temperature increasing, due to the reactive wetting between molten Ag and Ti2AlC. Small contact angle (14°) is obtained at 1130 ℃. Good wettability facilitates the preparation and improves the arc erosion resistance of Ag/Ti2AlC.
3) Ag/10TAC composite exhibits uniform structure, high density, moderate hardness, low resistivity, and favorable arc erosion resistance.
4) Ti2AlC has been proven experimentally to be a promising reinforcement for Ag-based electric contact material.
References
[1] G WINDRED. Electrical contact resistance. Journal of the Franklin Institute, 231, 547-585(1941).
[2] R HOLM, E HOLM. Electric Contacts Handbook. Berlin: Springer(1958).
[3] V COSOVIC, A COSOVIC, N TALIJAN et al. State of the art and challenges in development of electrical contact materials in the light of the RoHS directive. Science of Sintering, 44, 245-253(2012).
[4] G SLADE P. Effect of high temperature on the release of heavy metals from AgCdO and AgSnO2 contacts. IEEE Transactions on Components, Hybrids, and Manufacturing Technology, 12, 5-15(1989).
[5] H SCHRODER K. Silver-metal oxides as contact materials. IEEE Transactions on Components, Hybrids, and Manufacturing Technology, 10, 127-134(1987).
[6] P WU C, Q YI D, J LI et al. Investigation on microstructure and performance of Ag/ZnO contact material. Journal of Alloys and Compounds, 457, 565-570(2008).
[7] L ZHOU X, C CAO J, C CHEN J et al. Micro-superplastic behavior of copper oxide in AgCuO composites. Rare Metal Materials and Engineering, 42, 2242-2244(2013).
[8] D WOJCIK-GRZYBEK, K FRYDMAN, P BORKOWSKI. The influence of the microstructure on the switching properties of Ag C, Ag-WC-C and Ag-WC contact materials. Archives of Metallurgy and Materials, 58, 1059-1065(2013).
[9] P WU C, Q YI D, W WENG et al. Arc erosion behavior of Ag/Ni electrical contact materials. Materials & Design, 85, 511-519(2015).
[10] W BARSOUM M. The M
[11] M SUN Z. Progress in research and development on MAX phases: a family of layered ternary compounds. International Materials Reviews, 56, 143-166(2011).
[12] M ZHANG, B TIAN W, G ZHANG P et al. Microstructure and properties of Ag-Ti3SiC2 contact materials prepared by pressureless sintering. International Journal of Minerals, Metallurgy, and Materials, 25, 810-816(2018).
[13] X DING J, B TIAN W, G ZHANG P et al. Arc erosion behavior of Ag/Ti3AlC2 electrical contact materials. Journal of Alloys and Compounds, 740, 669-676(2018).
[14] X DING J, B TIAN W, D WANG D et al. Corrosion and degradation mechanism of Ag/Ti3AlC2 composites under dynamic electric arc discharging. Corrosion Science, 156, 147-160(2019).
[15] D WANG D, B TIAN W, B MA A et al. Anisotropic properties of Ag/Ti3AlC2 electrical contact materials prepared by equal channel angular pressing. Journal of Alloys and Compounds, 784, 431-438(2019).
[16] M LIU M, L CHEN J, H CUI et al. Ag/Ti3AlC2 composites with high hardness, high strength and high conductivity. Materials Letters, 213, 269-273(2018).
[17] X DING J, B TIAN W, G ZHANG P et al. Preparation and arc erosion properties of Ag/Ti2SnC composites under electric arc discharging. Journal of Advanced Ceramics, 8, 90-101(2019).
[18] X DING J, B TIAN W, D WANG D et al. Microstructure evolution, oxidation behavior and corrosion mechanism of Ag/Ti2SnC composite during dynamic electric arc discharging. Journal of Alloys and Compounds, 785, 1086-1096(2019).
[19] F ZHU J, Q GAO J, F YANG J et al. Synthesis and microstructure of layered-ternary Ti2AlC ceramic by high energy milling and hot pressing. Materials Science and Engineering A, 490, 62-65(2008).
[20] L BAI Y, X ZHANG H, D HE X et al. Growth morphology and microstructural characterization of nonstoichiometric Ti2AlC bulk synthesized by self-propagating high temperature combustion synthesis with pseudo hot isostatic pressing. International Journal of Refractory Metals and Hard Materials, 45, 58-63(2014).
[21] B ZHOU W, C MEI B, Q ZHU J et al. Rapid synthesis of Ti2AlC by spark plasma sintering technique. Materials Letters, 59, 131-134(2005).
[22] Y LIANG B, Z WANG M, P LI X et al. Synthesis of Ti2AlC by laser- induced self-propagating high-temperature sintering. Journal of Alloys and Compounds, 501, L1-L3(2010).
[23] W LIU, Z BO T, P XIE Z et al. Fabrication of injection moulded translucent alumina ceramics
[24] L YEH C, G SHEN Y. Combustion synthesis of Ti3AlC2 from Ti/Al/C/TiC powder compacts. Journal of Alloys and Compounds, 466, 308-313(2008).
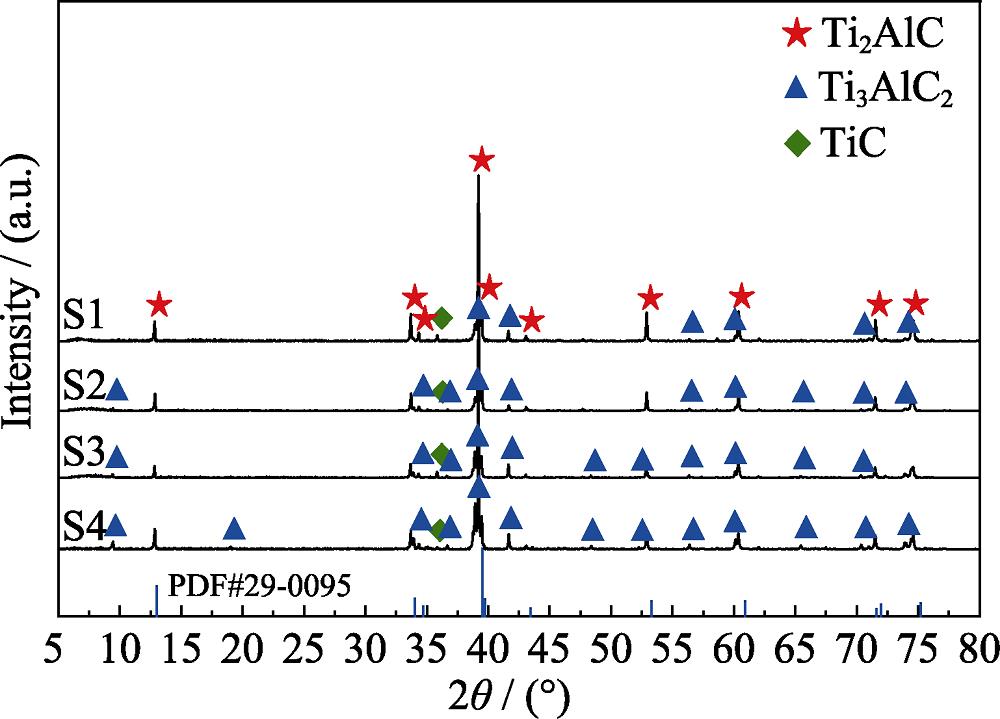
Set citation alerts for the article
Please enter your email address