Abstract
We report on the modification of the wettability of stainless steel by picosecond laser surface microstructuring in this paper. Compared with traditional methods, picosecond laser-induced surface modification provides a fast and facile method for surface modification without chemical damage and environmental pollution. As a result of treatment by 100 ps laser pulses, microstructures are fabricated on the stainless steel sample surface, contributing to the increase of the contact angle from 88° to 105°, which realizes a transformation from hydrophilicity to hydrophobicity. The morphological features of fabricated microstructures are characterized by scanning electron microscopy and optical microscopy.1. INTRODUCTION
The wettability of materials is one of the key characteristics in materials science and engineering. As its application has bearing in many areas such as machinery lubrication, friction, fabric dyeing, and painting, research on modification of the wettability of material surfaces has received much attention. Previous studies indicate that the wettability of material surfaces depends on the chemical composition and micro-geometry on the surface [1]. Thus, the modification of wettability can be realized by changing the surface morphology or forming microstructures on the surface. There are several methods that can modify surface wettability, such as phase disengagement [2], chemical vapor deposition [3], soft etching [4], anode oxidation [5], and electrodeposition [6].
Compared with these methods, laser-induced surface modification provides a fast and facile approach for surface modification without chemical damage or environmental pollution [7–11]. Many researchers have explored how the different parameters affect the result, and explain the mechanism of the interaction between the laser pulses and the materials [12–15]. It is well known that, for laser-induced surface modification, besides the thermal and optical properties of materials, laser pulse duration is a very key parameter that may affect the results. Micromachining of metals with nanosecond laser pulses was studied by Knowles et al., who found that, with the appropriate choice of laser parameters and processing strategies, high-quality micromachined structures could be fabricated [16]. However, with nanosecond laser pulses, the absorption occurs on a time scale that is longer than the time scale for energy transfer to the lattice, resulting in heating of the lattice. According to the two-temperature model [17], these thermal effects cannot be ignored when nanosecond laser pulses irradiate metals. While the thermal effect can be ignored in femtosecond laser processing of metals [18], it is difficult to use this technology in industry because of the high cost. Recently, picosecond lasers have come into industrial applications because they are easier to operate and they are more cost effective compared to femtosecond lasers.
In this work, we perform a study of surface modification of AISI 304 and AISI 316 stainless steel induced by 100 ps laser pulses, focusing on evolution of the contact angle and morphological characteristics. Even though the thermal effect cannot be ignored with 100 ps laser processing of stainless steel, a critical advantage of using picosecond laser pulses is that picosecond laser technology is already being applied for industrial micromachining, thus making the industrialization of laser-induced surface modification of metal possible.
Sign up for Photonics Research TOC. Get the latest issue of Photonics Research delivered right to you!Sign up now
2. EXPERIMENTAL
In this work, we uses a picosecond laser (Fianium) that generates 532 nm, 100 ps laser pulses at a repetition rate of 500 kHz. The average power is 0.62 W. The laser beam was focused onto the cleaned and polished stainless steel surface using a 0.3 NA objective lens, forming a spot with a 16 μm radius. The stainless steel sample is on a 3D linear translation stage. While the 3D linear translation stage scans at a preset speed, the laser forms a micro-groove in the direction on the stainless steel surface. With a shift of the stage at a constant distance interval in the direction, the laser generates a second micro-groove parallel to the first micro-groove on the sample surface. This process was repeated to produce an extended array of micro-grooves with an area of on the stainless steel surface. By tuning the scanning speed and distance intervals between two adjacent micro-grooves, we produced a series of fabricated stainless steel surfaces by using the picosecond laser.
After fabrication by the picosecond laser pulses, we wiped the stainless steel surface with ethanol to clean up the ablation debris. To measure the wettability of steels, we performed a study on the static contact angle measured with a contact angle measurement system (SL200B) using the sessile drop method. A micro-syringe was used to gently drop a 2 μL distilled water droplet on the surface. The images of the water droplet were captured using a CCD camera, and the images were used to measure the contact angle formed at the water–solid interface. We measured the contact angle three times on the same area to make sure the deviation was as small as possible, ensuring that the uncertainty of the contact angle was within . The time interval between two adjacent measurements was 2 min to allow the water droplet to evaporate completely. To identify the morphological features, we examined each area under optical microscopy (OM) and scanning electron microscopy (SEM).
3. RESULTS AND DISCUSSION
Figure 1 shows the image of the treated areas on an AISI 304 stainless steel sample captured by a digital camera. There are eight treated areas on the sample. The sample is adhered to one glass slide by double-sided adhesive so that the surface of the steel is as flat as possible. On the treated areas, from left to right, the scanning speed and interval are varied. The scanning speed and interval of the first area are 400 μm/s and 20 μm, respectively. On the second area, they are 1000 μm/s and 40 μm, respectively. From the third to the eighth areas, the scanning speed and the interval are gradually increased in 1000 μm/s and 20 μm steps. We define that the untreated area has the parameters of scanning speed 0 μm/s and interval 0 μm. As can be seen, in the first area, by absorbing the picosecond laser energies, we make AISI 304 stainless steel highly absorptive, presenting a black appearance, while the following areas turn gray gradually [19].

Figure 1.Image of the treated areas under different parameters. From the first to the eighth areas, scanning speeds and intervals are 400 μm/s and 20 μm, 1000 μm/s and 40 μm, 2000 μm/s and 60 μm, 3000 μm/s and 80 μm, 4000 μm/s and 100 μm, 5000 μm/s and 120 μm, 6000 μm/s and 140 μm, 7000 μm/s and 160 μm, respectively.
Figures 2 and 3 show the surface microstructures observed by OM and SEM, respectively. As can be seen from Figs. 2 and 3, treatment by picosecond laser pulses results in micro-groove-like microstructures being formed on the surface. Figure 2(a) shows the microstructures with the parameters of scanning speed 1000 μm/s and interval 40 μm, while Figs. 2(b), 2(c) and 2(d) have different parameters in accordance with the step sizes above. Figure 3(c) shows that the cavities and mastoids on the surface are fabricated. Figure 3(d) shows the low spatial frequency picosecond laser-induced periodic surface structures (LSFLs) [20,21], which have a period of 473 nm, below the output laser wavelength of 532 nm.
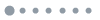
Figure 2.OM images of the treated AISI 304 stainless steels under different parameters: (a) 1000 μm/s scanning speed and 40 μm scanning interval, (b) 2000 μm/s scanning speed and 60 μm scanning interval, (c) 3000 μm/s scanning speed and 80 μm scanning interval, and (d) 4000 μm/s scanning speed and 100 μm scanning interval.
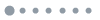
Figure 3.(a) SEM image of the treated AISI 304 stainless steel under 2000 μm/s scanning speed and 60 μm scanning interval with four periods of microstructures, (b) SEM image of the treated AISI 304 stainless steel with two periods of microstructures, (c) SEM image of the cavities and mastoids fabricated on the surface, and (d) SEM image of the low spatial frequency picosecond laser-induced periodic surface structures.
To investigate the relationship between the wetting behaviors of AISI 304 stainless steel and different processing parameters, we put a 2 μL water droplet on the surface, and then perform a study on the static contact angle. As Fig. 4 presents, alteration of the static contact angle goes with different scanning intervals and different scanning speeds. From Fig. 4 we can see that the contact angle regularly decreases with increasing scanning interval and increasing scanning speed. The singular point where the scanning interval is 0 μm and the scanning speed is 0 μm/s stands for the contact angle of the untreated AISI 304 stainless steel whose contact angle has an approximate value of 88°. As is well known, metal materials such as the AISI 304 stainless steel have a high surface energy resulting in hydrophilicity. After irradiation by picosecond laser pulses, some microstructures on the surface are fabricated, contributing to the contact angle increasing from 88° to 105°. This suggests a transformation from hydrophilicity to hydrophobicity. According to the Wenzel model [22], the contact angle will increase with increasing roughness of a hydrophobic surface while the contact angle will decrease with increasing roughness of a hydrophilic surface. Thus, the Wenzel model cannot explain this transformation. A more likely explanation is given by the Cassie–Baxter model [23]. Upon irradiation by the picosecond laser pulses, a stable composite interface in such a manner that air is trapped in the cavities of a rough surface is formed. This results in a composite solid–air–liquid interface contributing to the evolution of the wetting behaviors. When the scanning speed increases, the laser energies per unit time per unit area that are absorbed by the stainless steel decrease, leading to a shallower cavity than before. Since the cavity is shallower and the scanning interval between two adjacent micro-grooves is larger, less air volume is trapped in the cavities of the surface, causing the contact angle to decrease, as depicted in Fig. 4. We also can observe that the contact angles of treated areas have a rapid decrease within the scanning speeds from 400 to 2000 μm/s and the intervals from 20 to 60 μm, while the contact angles tend to be stable gradually within the scanning speeds from 3000 to 7000 μm/s and the intervals from 80 to 160 μm.
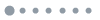
Figure 4.Alteration of static contact angle under different scanning intervals and different scanning speeds when processing AISI 304 stainless steel.
To identify whether this model is in accord with situations when processing other kinds of stainless steel, we also tried to fabricate microstructures by the picosecond laser pulse irradiating AISI 316 stainless steel, which has an origin contact angle of about 74°, which is less than the origin contact angle of AISI 304. We investigate the effects of scanning speed and interval on the contact angle, respectively. The other parameters are the same as those used to process AISI 304 stainless steel. Figure 5(a) shows the change in the contact angle with different scanning intervals when the scanning speed is 1200 μm/s, while Fig. 5(b) shows the contact angle change with different scanning speeds when the scanning interval is 40 μm. Although the contact angle before fabrication by the picosecond laser pulses is different from that in Fig. 4, the contact angles after irradiation in Figs. 5(a) and 5(b) both increase at different levels, which have the same trends as those in Fig. 4, exactly corresponding with the Cassie–Baxter model. From Fig. 5, we can see that when the scanning interval varies from 20 to 100 μm, the contact angle decreases from 95° to 76°, while when scanning speed varies from 400 to 2000 μm/s, the contact angle decreases from 87° to 75°. Therefore, we can conclude that both the scanning speed and the scanning interval are the important parameters when processing stainless steels.
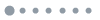
Figure 5.Alteration of static contact angle under different scanning intervals and different scanning speeds when processing AISI 316 stainless steel, respectively.
4. CONCLUSIONS
In summary, we have demonstrated modification of wettability by picosecond laser surface microstructuring. By varying the scanning interval and the scanning speed, we change the wetting behaviors of the AISI 304 stainless steel surface with contact angles increasing from 88° to 105°, realizing a transformation from hydrophilicity to hydrophobicity. This transformation has tremendous potential in various technological applications. We also conclude that the mechanism of contact angle on the stainless steel is the same when processing different kinds of stainless steels. Compared with nanosecond and femtosecond laser pulses, picosecond laser pulse induced surface modification has its unique advantages, making this technology industrialization possible.
References
[1] D. Bonn, J. Eggers, J. Indekeu, J. Meunier, E. Rolley. Wetting and spreading. Rev. Mod. Phys., 81, 739-805(2009).
[2] A. Nakajima, K. Abe, K. Hashimoto, T. Watanable. Preparation of hard super-hydrophobic films with visible light transmission. Thin Solid Films, 376, 140-143(2000).
[3] K. Teshima, H. Sugimura, Y. Inoue, O. Takai. Wettability of poly(ethylene terephthalate) substrates modified by a two-step plasma process: ultra water-repellent surface fabrication. Chem. Vap. Deposition, 10, 295-297(2004).
[4] Y. N. Xia, J. A. Rogers, K. E. Paul, G. M. Whitesides. Unconventional methods for fabricating and patterning nanostructures. Chem. Rev., 99, 1823-1848(1999).
[5] S. Shibuichi, T. Yamamoto, T. Onda, K. Tsujii. Super water- and oil-repellent surfaces resulting from fractal structure. J. Colloid Interface Sci., 208, 287-294(1998).
[6] Y. K. Lai, Z. Q. Lin, Z. Chen, J. Y. Huang, C. J. Lin. Fabrication of patterned CdS/TiO2 heterojunction by wettability template-assisted electrodeposition. Mater. Lett., 64, 1309-1312(2010).
[7] M. Zhou, H. F. Yang, B. J. Li, J. Dai, J. K. Di, E. L. Zhao, L. Cai. Forming mechanisms and wettability of double-scale structures fabricated by femtosecond laser. Appl. Phys. A, 94, 571-576(2009).
[8] L. L. Ran, S. L. Qu. Structure formation on the surface of alloys irradiated by femtosecond laser pulses. Appl. Surf. Sci., 256, 2315-2318(2010).
[9] S. S. Mao, F. Quere, S. Guizard, X. Mao, R. E. Russo, G. Petite, P. Martin. Dynamics of femtosecond laser interactions with dielectrics. Appl. Phys. A, 79, 1695-1709(2004).
[10] M. Couillard, A. Borowiec, H. K. Haugen, J. S. Preston, E. M. Griswold, G. A. Botton. Subsurface modifications in indium phosphide induced by single and multiple femtosecond laser pulses: a study on the formation of periodic ripples. J. Appl. Phys., 101, 033519(2007).
[11] Y. Shen, D. Liu, W. Zhang, G. Dearden, K. Watkins. Ultrafast laser surface wettability modification on alumina surface. Chin. Opt. Lett., 11, S21403(2013).
[12] Y. Y. Dong, P. Molian. Coulomb explosion-induced formation of highly oriented nanoparticles on thin films of 3C–SiC by the femtosecond pulsed laser. Appl. Phys. Lett., 84, 10-12(2004).
[13] Q. H. Wu, Y. R. Ma, R. C. Fang, Y. Liao, Q. X. Yu, X. L. Chen, K. Wang. Femtosecond laser-induced periodic surface structure on diamond film. Appl. Phys. Lett., 82, 1703-1705(2003).
[14] T. Q. Jia, H. X. Chen, M. Huang, F. L. Zhao, J. R. Qiu, R. X. Li, Z. Z. Xu, X. K. He, J. Zhang, H. Kuroda. Formation of nanogratings on the surface of a ZnSe crystal irradiated by femtosecond laser pulses. Phys. Rev. B, 72, 125429(2005).
[15] Y. Shimotsuma, P. G. Kazansky, J. R. Qiu, K. Hirao. Self-organized nanogratings in glass irradiated by ultrashort light pulses. Phys. Rev. Lett., 91, 247405(2003).
[16] M. R. H. Knowles, G. Rutterford, D. Karnakis, A. Ferguson. Micro-machining of metals, ceramics and polymers using nanosecond lasers. Int. J. Adv. Manuf. Technol., 33, 95-102(2007).
[17] J. G. Fujimoto, J. M. Liu, E. P. Ippen, N. Bloembergen. Femtosecond laser interaction with metallic tungsten and nonequilibrium electron and lattice temperatures. Phys. Rev. Lett., 53, 1837-1840(1984).
[18] B. N. Chichkov, C. Momma, S. Nolte, F. von Alvensleben, A. Tünnermann. Femtosecond, picosecond and nanosecond laser ablation of solids. Appl. Phys. A, 63, 109-115(1996).
[19] A. Y. Vorobyev, C. L. Guo. Colorizing metals with femtosecond laser pulses. Appl. Phys. Lett., 92, 041914(2008).
[20] D. Dufft, A. Rosenfeld, S. K. Das, R. Grunwald, J. Bonse. Femtosecond laser-induced periodic surface structures revisited: a comparative study on ZnO. J. Appl. Phys., 105, 034908(2009).
[21] V. S. Mitko, G. R. B. E. Römer, A. J. HuisintVeld, J. Z. P. Skolski, J. V. Obona, V. Ocelík, J. T. M. DeHossond. Properties of high-frequency sub-wavelength ripples on stainless steel 304L under ultra short pulse laser irradiation. Phys. Procedia, 12, 99-104(2011).
[22] R. N. Wenzel. Resistance of solid surfaces to wetting by water. Ind. Eng. Chem., 28, 988-994(1936).
[23] A. B. D. Cassie, S. Baxter. Wettability of porous surfaces. Trans. Faraday Soc., 40, 546-551(1944).