Hongmao Zhang, Wurikaixi Aiyiti, Yutao Zhang. Study on Process Optimization and Mechanical Properties of Tantalum Formed by Selective Laser Melting[J]. Chinese Journal of Lasers, 2025, 52(12): 1202310

Search by keywords or author
- Chinese Journal of Lasers
- Vol. 52, Issue 12, 1202310 (2025)

Fig. 1. Tantalum power. (a) Morphology of tantalum powder; (b) particle size distribution of tantalum powder

Fig. 2. Schematics of process test. (a) SLM process; (b) scanning mode
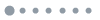
Fig. 3. Surface morphologies of samples under different scanning speeds at laser power of 350 W. (a) 350 mm/s; (b) 450 mm/s;
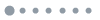
Fig. 4. Surface morphologies of samples under different laser powers at scanning speed of 650 mm/s. (a) 150 W; (b) 200 W; (c) 250 W;(d)300 W; (e) 350 W; (f) 400 W
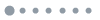
Fig. 5. Lateral section morphologies of samples under different scanning speeds at laser power of 350 W. (a) 350 mm/s; (b) 450 mm/s; (c) 550 mm/s; (d) 650 mm/s; (e) 750 mm/s; (f) 850 mm/s
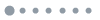
Fig. 6. Lateral section morphologies of samples under different laser powers at scanning speed of 650 mm/s. (a) 150 W; (b) 200 W;
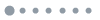
Fig. 7. Effects of energy density and scanning speed on relative density. (a) Relationship between energy density and relative density; (b) relationship between scanning speed and relative density
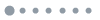
Fig. 8. Effects of process parameters on microhardness. (a) Relationship between scanning speed and microhardness at laser power of 350 W; (b) relationship between laser power and microhardness at scanning speed of 650 mm/s
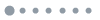
Fig. 9. Microstructures of tantalum samples. (a) Microstructure characterization; (b) full view; (c) low magnification; (d) high magnification
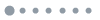
Fig. 10. EBSD data of samples prepared under optimum process parameters. (a) Grain and grain boundary; (b) orientation angle distribution; (c) pole figure; (d) inverse pole figure; (e) grain distribution; (f) grain boundary distribution
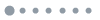
Fig. 11. Tensile properties. (a) Stress-strain curves of tantalum samples formed by SLM; (b) relationship between tensile strength and elongation of tantalum samples prepared by different processes
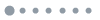
Fig. 12. Fracture morphologies. (a) Macroscopic morphology; (b) low magnification image; (c) local magnification image
|
Table 1. Chemical compositions of pure tantalum powder
|
Table 2. Process parameters
|
Table 3. Mechanical properties of tantalum samples under different forming processes

Set citation alerts for the article
Please enter your email address