Author Affiliations
1National Research Center for High-Efficiency Grinding, College of Mechanical and Vehicle Engineering, Hunan University, Changsha 410082, China2Advanced Manufacturing Laboratory of Micro-nano Optical Devices, Shenzhen Research Institute, Hunan University, Shenzhen 518000, Chinashow less
Fig. 1. Fabrication of metasurfaces by electron beam lithography (EBL). (a) Lift-off process for metallic metasurfaces fabrication and its processed (b) transmissive metallic metasurface and (c) reflective metallic metasurface; (d) Hard-mask etching process for dielectric metasurfaces fabrication and its processed (e) Si metasurface, (f) GaN achromatic metalens and (g) TiO2 holographic metasurface; (h) Conformal filling process for dielectric metasurfaces fabrication and its processed (i) TiO2 metalens and (j) Nb2O5 metasurface
Fig. 2. Fabrication of metasurfaces by focused ion beam (FIB) etching. The metallic nano-hole structures fabricated by FIB is used for (a) holographic metasurface, (b) near-field light field control and (c) structural color modulation; (d) Metallic nanopillar-type metasurface etched by FIB for vortex optical focusing; (e) Metasurface of quasi-3D structure fabricated by FIB. Non-metallic metasurface fabricated by FIB, such as (f) GST phase change material metasurface, (g) perovskite metasurface and (h) metal-dielectric multi-material laminated structure
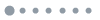
Fig. 3. Fabrication of metasurfaces by direct laser writing (DLW). (a) Polarization-controllable optical vortex modulation all-dielectric metasurface based on DLW; (b) Schematic diagram of single-step ultrafast laser interference direct writing etching process; (c) Fourier hologram based on ultrafast femtosecond laser etching technology; (d) Two terahertz metasurface with elliptic apertures fabricated by the femtosecond laser slit space control technology on the gold film; (e) 2D perovskite lens fabricated by femtosecond laser; (f) Physical image and SEM image of the new type flat lens whose performance is easy to control based on 2D perovskite nanosheets; (g) SEM images of direct and inverted photonic structure with different symmetry fabricated by two-photon polymerization 3D printing process; (h) Processing principle diagram and SEM image of the nearly perfect infrared spectrum absorption metasurface based on two-photon polymerization 3D printing process; (i) Process flow chart of computer-generated holographic projection based on two-photon polymerization 3D printing process and the schematic diagram of the hologram; (j) Schematic diagram of a Daman grating generating an N×N dot array in the far field based on two-photon polymerization 3D printing process
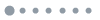
Fig. 4. Fabrication of metasurfaces by mask photolithography process. (a) Schematic of metasurface-based half-wave plate by processing directly on Si wafer (left), photograph of the fabricated 12-in Si metasurface wafer and three SEM images of Si pillar array inside the center white squares of the wafer(right); (b) Schematic of color display metasurface by adding a dielectric layer before the photolithography (left), silicon wafers and nanostructures of different sizes, the bottom left is the pattern of color display (right); (c) Flow diagram of photolithography on the transparent glass substrate (left), the fabricated wafer and the enlarged unit pattern(right); (d) Lithography process of the all-glass metasurface with opaque layer (up), the SEM images of the fabricated nanopillars and result of lens(down); (e) Schematic of the metalens by layer transfer technology on glass substrate (left), the schematic of unit structure (right); (f) SEM image of reflective metasurface with a metal layer (left), the schematic of structure of photolithography (right); (g) Schematic of the near-field lithography structure with the reflective plasmonic lens
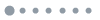
Fig. 5. Fabrication of metasurfaces by nanoimprint lithography. (a) SEM images of the two kinds of metasurface by thermal curing nanoimprint(left), schematic of the corresponding process(right); (b) Process of manufacturing with the thermal curing nanoimprint lithography and lift off (left) and the SEM image of the fabricated metasurface (right); (c) Schematic of the UV curing nanoimprint lithography process; (d) SEM image of the fabricated thermal emission metasurface by UV curing nanoimprint lithography. Top views and cross-sectional views are showed up and down and the images of before and after removing residual glue are showed left and right; (e) Cross-sectional SEM image of the asymmetric transmission metasurface processed by UV curing nanoimprint lithography; (f) Schematic of the stamp type nanoimprints: the preparation of the nanostamp, and the imprinting of the stamp and follow-up etching; (g) Process of the laser-assisted nanoimprint and the SEM image of the fabricated metasurface
Fig. 6. Fabrication of metasurfaces by other emerging processing methods. (a) Schematic diagram of the self-assembly process (top) and the micrograph of the metasurface of the processed reflector (bottom); (b) Image of the metasurface processed by the scanning probe lithography under the atomic force microscope. The coordinate axes are x, y, z coordinates
Process | Feature size | Applicable band | Precision | Process characteristics | Direct
writing technology
| Electron beam lithography | <10 nm | UV to infrared | ~1 nm | High resolution, high degree of freedom, low efficiency for large-scale or complicated pattern, subsequent pattern transfer process required | Focused ion beam etching | ~20 nm | Visible to infrared | <100 nm | High resolution, high degree of freedom, no material selectivity, ultralow efficiency | Laser direct writing | ~1 μm | Visible to terahertz | <1 μm | High degree of freedom, resolution is limited by the optical diffraction limit, subsequent pattern transfer process required | Ultrafast direct laser etching | <200 nm | <100 nm | No material selectivity, minimal thermal effect, low-damage-threshold | Two-photon (multiphoton) lithography | <200 nm | <100 nm | Higher resolution than single photon lithography, high spatial selectivity, three-dimensional structures processing | Scanning probe lithography | <10 nm | Visible to infrared | <10 nm | Simple process, low efficiency | Template transfer technology | Immersion lithography | <100 nm | Visible to infrared | <100 nm | High resolution, high alignment accuracy, high equipment cost, high requirements of processing | Plasmonic lithography | ~100 nm | Visible to infrared | <100 nm | High-resolution, high processing efficiency, short working life, poor fidelity | Hot embossing | Depend on the master | - | - | Relatively simple process, time consuming which is not suitable for mass production | UV-curable nanoimprint lithography | Nanoscale | High efficiency, material selectivity | Laser assisted direct imprint | ~10 nm | High-resolution, low heat release during processing, short processing time | Micro-contact printing | <100 nm | Low cost, suitable for large-area or simple pattern processing | Self-assembly lithography | nm - μm | - | ~1 nm | Low cost, suitable for large-area or simple pattern processing, simple process |
|
Table 1. Summary of fabrication methods of metasurfaces and their process characteristics
超构表面加工方法及其工艺特点总结