
- Matter and Radiation at Extremes
- Vol. 6, Issue 2, 025901 (2021)
Abstract
I. INTRODUCTION
A variety of physical experiments, such as central hotspot ignition,
To fabricate deuterated polymer microspheres meeting the physical requirements for ICF experiments, deuterated polystyrene (DPS) has been synthesized by radical polymerization and purified to remove hydrophilic substances.
A new type of solid deuterated polymer microsphere with a carbon hydrogen–carbon deuterium (CH-CD) multilayer has been designed to investigate the kinetic effects arising in the interpenetration layer between the corona plasma of the compressed bead and the plasma produced by the laser and the inner wall of the hohlraum because the solid CH bead can suppress implosion neutron and hydrodynamic instabilities, while the CD layer can produce a measurable D–D neutron yield.
II. EXPERIMENTAL
A. Materials
PS was purchased from Acros Organics, Inc., and PAMS was obtained from Southwest University of Science Technology, China.
Figure 1.GPC results for (a) PS and (b) PAMS materials.
Sample | |||
---|---|---|---|
PS | 222 000 | 118 000 | 1.9 |
PAMS | 441 000 | 410 000 | 1.1 |
Table 1. Weight-average molecular weight
B. Preparation of CH-CD multilayer polymer microspheres
The solid CH-CD multilayer polymer microspheres were prepared by a microfluidic technique and plasma polymerization (
Figure 2.Schematic illustration of CH-CD multilayer polymer microspheres.
C. Characterization
The thermal stabilities of the materials and corresponding beads were measured by thermogravimetric analysis (TGA) at 10 °C/min from 50 °C to 600 °C. The flow rate of the nitrogen atmosphere was 40 ml/min. The glass transition temperature was measured by differential scanning calorimetry (DSC) at 10 °C/min from 50 °C to 220 °C. The flow rate of the nitrogen atmosphere was also 40 ml/min. A second scan was also run to eliminate the thermal history after an initial scan that was followed by cooling. The pyrolysis products of the materials and the beads were characterized by pyrolysis–gas chromatography–mass spectrometry (PY-GC-MS) at 500 °C for 30 s. Both the O droplets (which were composed of polymer solution) and the resulting shells were characterized by a digital microscope. The surfaces of the polymer microspheres and their cross-sectional morphologies were characterized by scanning electron microscopy (SEM). The beads were broken in liquid nitrogen, and the fractured surfaces before the SEM characterization were sputter-coated with gold under argon for 1 min. The polymer microspheres were also characterized by a computed tomography technique to observe the locations of vacuoles.
The diameters of the microspheres were measured by a measuring microscope. From the experimental results for the diameter, the out-of-roundness δOOR, defined as half the difference between the maximum and minimum outer diameters of a torus projected from the microsphere in six directions, was used to characterize the sphericity. The surface roughness was measured by both a white light interferometer and a sphere mapper. From the results of the white light interferometry, the average roughness Ra, root-mean-squared roughness Rq, and maximum height roughness Rt were calculated over the entire measured array as follows:
III. RESULTS AND DISCUSSION
A. Fabrication of solid CH beads
To obtain solid CH beads meeting the physical design requirements, an elaborate fabrication scheme was devised. The diameter of the CH beads was required to be 480 µm in this work, and so, according to conservation of mass, the average diameter of the corresponding droplets was calculated to be 1128 µm when the polymer mass fraction of the oil phase was 8.0%.
Figure 3.(a) Diameter distributions of solid PAMS beads (purple bars) and PS beads (green bars). (b) Optical micrograph of PAMS beads of 484
The sphericity, surface roughness, and residual solvent of the solid CH beads were determined to investigate the effect of the PS and PAMS materials on the quality of the beads. For both PS and PAMS beads, all the δOOR values were less than 1.0 µm, which meant that the sphericity was higher than 99.6%, i.e., all the beads had good sphericity. The PS beads showed better sphericity than the PAMS beads [
Figure 4.Effect of PS and PAMS materials on the quality of solid CH beads: (a) sphericity; (b) power spectrum; (c) surface roughness; (d) thermal properties.
The differences in sphericity and surface roughness are probably due to the different molecular weights and molecular structures of PS and PAMS. The viscosity of the PAMS solution is higher than that of the PS solution, and the PAMS chain length is greater, because the weight-average molecular weight of the PAMS is higher. Generally, the initial droplets are not ideal spheres, and they take some time to become spherical. Owing to the higher viscosity, the time to reach a spherical shape is shorter for PAMS droplets, and their ability to regain ideal sphericity is also weaker, which is unfavorable for improving sphericity. The higher viscosity also makes the rearrangement of PAMS chains more difficult. Moreover, there is one more side group (a methyl group) in the PAMS chain compared with the PS chain, which imposes more restrictions on the torsion about σ bonds in the backbone of the chain, and so the steric exclusion increases and the PAMS backbone becomes less flexible.
Moreover, our previous work has confirmed that complete removal of the FB remaining in the beads is a challenging task. The amount of residual solvent can be evaluated by TGA.
Sample | PS | PS beads | PAMS | PAMS beads |
---|---|---|---|---|
Weight loss percentage at 200 °C (%) | 0 | 5.0 | 2.5 | 7.3 |
Table 2. Weight loss percentage of PS material, PS beads, PAMS material, and PAMS beads at 200 °C.
Figure 5.Pyrolysis products of PAMS material at 500 °C for 30 s: (a) GC plot; (b) mass spectrum for
B. Fabrication of solid CH-CD multilayer polymer microspheres
To fabricate solid CH-CD multilayer polymer microspheres, a CD layer was deposited on the polymer beads by plasma polymerization with a working pressure of 10 Pa, a power of 15 W, and a D2/CD4 gas flow of 2/1. The average diameter of the PAMS-CD multilayer microspheres was 516 µm, and the variation coefficient of the diameter was less than 1.0%. Thus, the average wall thickness of the CD layer was 16.0 µm. The CD deposition rate v can be calculated by
Figure 6.Micrographs of solid CH-CD multilayer polymer microspheres: (a) optical micrography; (b) cross-sectional SEM images; (c) computed tomography image of PS-CD microspheres from two directions.
As shown in
Figure 7.DSC first–scan curves of the polymer materials and corresponding beads: (a) PS material and beads; (b) PAMS material and beads.
Figure 8.Effect of PS and PAMS materials on the quality of CH-CD multilayer polymer microspheres: (a) sphericity; (b) surface roughness; (c) SEM micrographs of microsphere surface.
IV. CONCLUSION
Solid CH-CD multilayer polymer microspheres were successfully prepared by a microfluidic technique and plasma polymerization. The diameter variation of the beads and the variation coefficient in each batch were less than 5 µm and 1.0%, respectively, indicating good monodispersity. The diameter of the solid CH beads and the wall thickness of the CD layer were controlled by the size of the corresponding droplets, as well as the CD deposition rate and deposition time, respectively. The effects of the PS and PAMS materials on the qualities of both the solid CH beads and the resulting CH-CD multilayer polymer microspheres were investigated. The PS and PAMS beads showed no significant differences in monodispersity and amount of residual solvent, but the PS beads had better sphericity and a smoother surface, probably owing to the differences in molecular structure and molecular weight between the PS and PAMS. Many vacuoles with 5 µm–30 µm diameter appeared in the central region of the PS-CD multilayer microspheres, because the glass transition temperature of the PS beads was lower than the temperature of plasma polymerization and there was some FB remaining in the beads. Therefore, the PAMS beads are more suitable for use as a mandrel for fabricating CH-CD multilayer polymer microspheres. The surface quality was reduced after coating with the CD layer. Further work is therefore necessary to find ways to improve the quality of solid CH-CD multilayer polymer microspheres.
References
[1] D. A. Callahan, D. T. Caseyspc, O. A. Hurricane et al. Fuel gain exceeding unity in an inertially confined fusion implosion. Nature, 506, 343-348(2014).
[2] M. E. Glinsky, J. Hammer, M. Tabak et al. Ignition and high gain with ultrapowerful lasers. Phys. Plasmas, 1, 1626-1634(1994).
[3] K. S. Anderson, R. Betti, C. D. Zhou et al. Shock ignition of thermonuclear fuel with high areal density. Phys. Rev. Lett., 98, 155001(2007).
[4] J. Liu, G. Ren, J. Yan et al. Neutron generation by laser-driven spherically convergent plasma fusion. Phys. Rev. Lett., 118, 165001(2017).
[5] M. Berg, D. L. Wilcox. Microsphere fabrication and applications: An overview. MRS Proc., 372, 3(1994).
[6] C.-H. Brachais, L. Guillot, C. Lattaud et al. Influence of a density mismatch on TMPTMA shells nonconcentricity. J. Appl. Polym. Sci., 124, 4882-4888(2012).
[7] A. A. Akunets, V. A. Davankov, A. V. Pastukhov et al. Hollow poly(alpha-methylstyrene) shells for inertial confinement fusion targets. J. Phys.: Conf. Ser., 907, 012020(2017).
[8] M. J. Bonino, D. R. Harding, W. Sweet et al. Properties of vapor-deposited and solution-processed targets for laser-driven inertial confinement fusion experiments. Matter Radiat. Extremes, 3, 312-321(2018).
[9] J. Biener, D. D. Ho, C. Wild et al. Diamond spheres for inertial confinement fusion. Nucl. Fusion, 49, 112001(2009).
[10] H.-b. Cai, X. T. He, S.-z. Wu et al. Physical studies of fast ignition in China. Plasma Phys. Controlled Fusion, 57, 064003(2015).
[11] K. Ishii, Y. Mori, Y. Nishimura et al. 1-Hz Bead-Pellet injection system for fusion reaction engaged by a laser HAMA using ultra-intense counter beams. Fusion Sci. Technol., 75, 36-48(2019).
[12] H. B. Cai, L. Q. Shan, W. S. Zhang et al. Experimental evidence of kinetic effects in indirect-drive inertial confinement fusion hohlraums. Phys. Rev. Lett., 120, 195001(2018).
[13] R. Hu, W. T. Kan, X. L. Xiong et al. Preparation of a deuterated polymer: Simulating to produce a solid tritium radioactive source. J. Nucl. Mater., 492, 171-177(2017).
[14] T. Norimatsu, M. Takagi, T. Yamanaka et al. Development of deuterated polystyrene shells for laser fusion by means of a density-matched emulsion method. J. Vac. Sci. Technol., A, 9, 2145-2148(1991).
[15] K. Nagai, T. Norimatsu, H. Yang et al. Fabrication of aerogel capsule, bromine-doped capsule, and modified gold cone in modified target for the fast ignition realization experiment (FIREX) project. Nucl. Fusion, 49, 095028(2009).
[16] S. F. Chen, Y. W. Huang, M. F. Liu et al. Progress and challenges in the fabrication of DPS shells for ICF. Matter Radiat. Extremes, 4, 018401(2019).
[17] Q. Chen, M. F. Liu, Y. Q. Zheng et al. Controllable production of deuterated polymer beads for ICF. J. Nucl. Mater., 535, 152159(2020).
[18] S. F. Chen, M. F. Liu, X. B. Qi et al. Improvement of wall thickness uniformity of thick-walled polystyrene shells by density matching. Chem. Eng. J., 241, 466-476(2014).
[19] R. Cook, R. Stephens, M. Takagi et al. Decreasing out-of-round in poly(a-methystyrene)mandrels by increasing interfacial tension. Fusion technology, 38, 46-49(2000).
[20] S. Bhandarkar, F. Elsner, R. Paguio et al. Understanding the critical parameters of the PAMS mandrel fabrication process. Fusion Sci. Technol., 70, 127-136(2016).
[21] H. B. Cai, F. Zhang, W. M. Zhou et al. Enhanced energy coupling for indirect-drive fast-ignition fusion targets. Nat. Phys., 16, 810-814(2020).
[22] H. B. Cai, L. Q. Shan, Z. Q. Yuan et al. Study of the kinetic effects in indirect-drive inertial confinement fusion hohlraums. High Energy Density Phys., 36, 100756(2020).
[23] Y. W. Huang, M. F. Liu, X. N. Wei et al.
[24] R. C. Cook, A. Nikroo.
[25] K. L. Ngai, D. J. Plazek. Physical Properties of Polymers Handbook(2007).
[26] H. Kim, L. Lurio, A. Rühm et al. Surface tension and surface roughness of supported polystyrene films. Macromolecules, 36, 5704-5709(2003).
[27] Y. Huang, M. Liu, L. Ye et al. Effects of molecular weight on thermal degradation of poly(α-methyl styrene) in nitrogen. J. Macromol. Sci., Part B., 54, 1479-1494(2015).
[28] Z. B. He, H. Liu, J. J. Wei et al. Chemical structure and mechanical properties of glow discharge polymer films and deuterated glow discharge polymer films. High Power Laser Particle Beams, 27, 032028(2015).
[29] X. Ai, X.-S. He, J.-L. Huang et al. The effect of axial ion parameters on the properties of glow discharge polymer in T2B/H2 plasma. J. Phys. D: Appl. Phys., 51, 095604(2018).
[30] J. E. G. Lipson, S. T. Milner. Multiple glass transitions and local composition effects on polymer solvent mixtures. J. Polym. Sci., Part B, 44, 3528-3545(2006).
[31] R. Bergman, H. Jansson, J. Swenson. Role of solvent for the dynamics and the glass transition of proteins. J. Phys. Chem. B, 115, 4099-4109(2011).
[32] J. Barnouin, C. Chicanne, M. Theobald et al. Gas etching to obtain germanium doped CHx microshells compatible with the laser megajoule target specifications. Fusion Sci. Technol., 49, 757-763(2006).
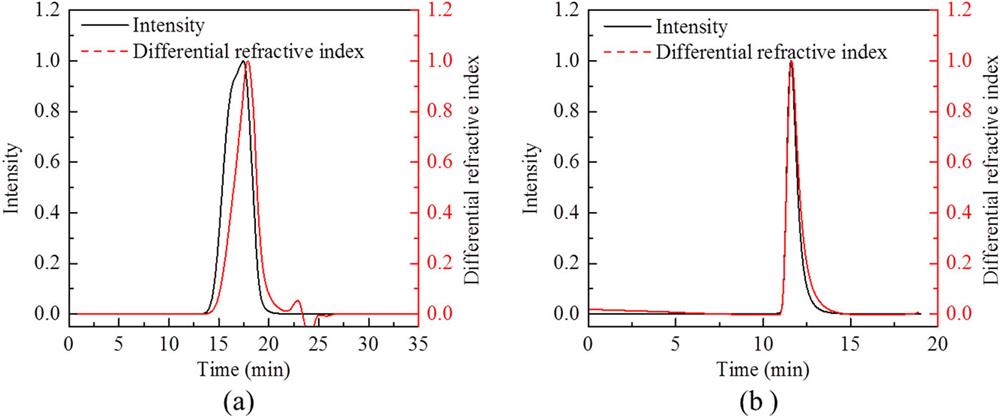
Set citation alerts for the article
Please enter your email address