Yu Wang, Leshi Shu, Shaoning Geng, Bin Li, Chunming Wang, ping Jiang. Status and Development Trend of Laser Welding Technology for Automotive Body[J]. Chinese Journal of Lasers, 2022, 49(12): 1202004

Search by keywords or author
- Chinese Journal of Lasers
- Vol. 49, Issue 12, 1202004 (2022)
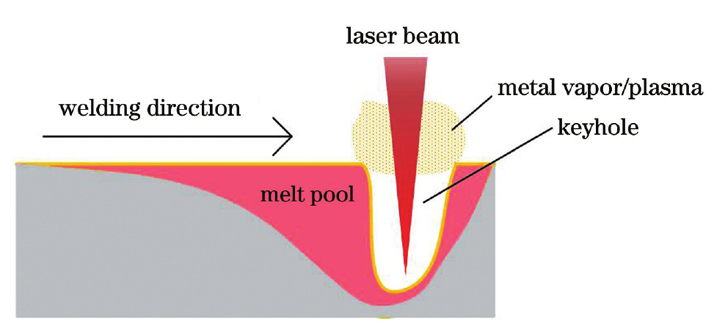
Fig. 1. Schematic of laser deep penetration welding process
![Overall tensile strength versus heat input[26]](/richHtml/zgjg/2022/49/12/1202004/img_02.jpg)
Fig. 2. Overall tensile strength versus heat input[26]
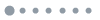
Fig. 3. Schematic of laser filler welding process
![Application of laser brazing in automotive industry[33]. (a) Laser joining of hatchback parts; (b) principle diagram of laser brazing](/Images/icon/loading.gif)
Fig. 4. Application of laser brazing in automotive industry[33]. (a) Laser joining of hatchback parts; (b) principle diagram of laser brazing
![Principle diagram of trifocal laser brazing[39]](/Images/icon/loading.gif)
Fig. 5. Principle diagram of trifocal laser brazing[39]
![Thermal imaging in brazing process[39]. (a) Monofocal brazing; (b) trifocal brazing](/Images/icon/loading.gif)
Fig. 6. Thermal imaging in brazing process[39]. (a) Monofocal brazing; (b) trifocal brazing
![Microstructures at selected regions for joints obtained with different filler metals[43] . (a)-(c) Pure Al; (d)-(f) AlSi5; (g)-(i) AlSi12](/Images/icon/loading.gif)
Fig. 7. Microstructures at selected regions for joints obtained with different filler metals[43] . (a)-(c) Pure Al; (d)-(f) AlSi5; (g)-(i) AlSi12
![Schematic of laser-arc hybrid welding process[45]](/Images/icon/loading.gif)
Fig. 8. Schematic of laser-arc hybrid welding process[45]
![Weld morphologies under different welding schemes[46] . (a) Laser guided arc; (b) arc guided laser](/Images/icon/loading.gif)
Fig. 9. Weld morphologies under different welding schemes[46] . (a) Laser guided arc; (b) arc guided laser
![Formation of laser-dominated region and laser-MIG hybrid-dominated region[48]. (a) Laser-dominated region in laser welding process; (b) MIG-dominated region in MIG welding process; (c) laser-MIG hybrid-dominated region in laser-MIG hybrid welding process](/Images/icon/loading.gif)
Fig. 10. Formation of laser-dominated region and laser-MIG hybrid-dominated region[48]. (a) Laser-dominated region in laser welding process; (b) MIG-dominated region in MIG welding process; (c) laser-MIG hybrid-dominated region in laser-MIG hybrid welding process
![Weld appearance and microstructures for laser-MIG hybrid welding[48]. (a) Weld appearance; (b) fine dendrite in laser-MIG hybrid-dominated region; (c)-(e) morphologies of fusion line between laser-MIG hybrid-dominated region and laser-dominated region; (f) coarse dendrite in laser-dominated region](/Images/icon/loading.gif)
Fig. 11. Weld appearance and microstructures for laser-MIG hybrid welding[48]. (a) Weld appearance; (b) fine dendrite in laser-MIG hybrid-dominated region; (c)-(e) morphologies of fusion line between laser-MIG hybrid-dominated region and laser-dominated region; (f) coarse dendrite in laser-dominated region
![Schematic for detection-compensation-tracking of weld seam [56]](/Images/icon/loading.gif)
Fig. 12. Schematic for detection-compensation-tracking of weld seam [56]
![DIGI-LAS/MDL system used for roof welding[58]](/Images/icon/loading.gif)
Fig. 13. DIGI-LAS/MDL system used for roof welding[58]
![Relationship model between keyhole-induced porosity and multi-sensing signals[61]. (a) Relationship between keyhole depth variation and porosity; (b) CNN-based porosity detection with keyhole opening morphological characteristics](/Images/icon/loading.gif)
Fig. 14. Relationship model between keyhole-induced porosity and multi-sensing signals[61]. (a) Relationship between keyhole depth variation and porosity; (b) CNN-based porosity detection with keyhole opening morphological characteristics
![Schematic for detection of laser welding defects based on laser vision[65]](/Images/icon/loading.gif)
Fig. 15. Schematic for detection of laser welding defects based on laser vision[65]
|
Table 1. Metal materials commonly used for automotive body
|
Table 2. Laser welding processes commonly used for automotive body
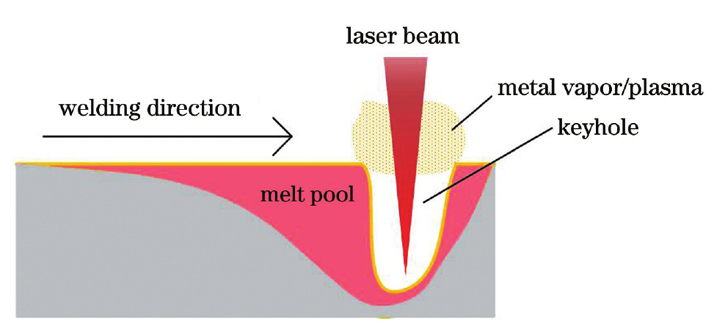
Set citation alerts for the article
Please enter your email address