Zhaojian Li, Heng Gu, Lili Qian, Xudong Ren. Thermodynamic Behavior of Gaussian / Flat‑Top Laser Powder Bed Fusion[J]. Chinese Journal of Lasers, 2025, 52(12): 1202304

Search by keywords or author
- Chinese Journal of Lasers
- Vol. 52, Issue 12, 1202304 (2025)

Fig. 1. Energy distribution patterns. (a) Gaussian laser beam (140 μm); (b) flat-top laser beam (140 μm)

Fig. 2. Dimensions and meshing of single-pass and multi-pass geometric models. (a) Geometry dimension of single-pass model; (b) single-pass model mesh; (c) geometry dimension of multi-pass model; (d) multi-pass model mesh
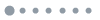
Fig. 3. Thermophysical parameters and mechanical properties of the material. (a) Density; (b) thermal conductivity; (c) specific heat capacity; (d) thermal expansion coefficient; (e) Young’s modulus; (f) yield strength
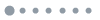
Fig. 4. Surface topography of the melt track under different laser powers for single-pass forming with a flat-top laser beam at a scanning speed of 360 mm/s
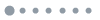
Fig. 5. Scanning strategy and the positions of monitoring points node 1 and node 2
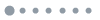
Fig. 6. Cross-section comparison of molten-pools for flat-top laser beam. (a) Experimental molten-pool size; (b) simulated molten-pool size and temperature field
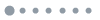
Fig. 7. Temperature evolution of Gaussian and flat-top laser beams under unidirectional scanning strategy with scanning speed of 700 mm/s and hatch distance of 0.112 mm. (a) Temperature distribution of Gaussian laser beam; (b) temperature distribution of flat-top laser beam; (c) temperature gradient distribution of Gaussian laser beam; (d) temperature gradient distribution of flat-top laser beam
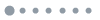
Fig. 8. Temperature evolution of Gaussian and flat-top laser beams under unidirectional scanning strategy with scanning speed of 700 mm/s and hatch distance of 0.112 mm. (a) Temperature variation at node 1; (b) temperature variation at node 2; (c) temperature change rate at node 1; (d) temperature change rate at node 2
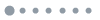
Fig. 9. Variation of temperature peaks at node 1 and node 2 with scanning speed and laser power for Gaussian and flat-top laser beams. (a) (b) Temperature peak at node 1; (c) (d) temperature peak at node 2
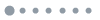
Fig. 10. Equivalent stress variation for node 1 and node 2 during the 100 s LPBF forming process. (a) Node 1; (b) node 2
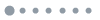
Fig. 11. Overall residual stress distributions and directional stress distributions generated by Gaussian and flat-top laser beams at the end of 100 s LPBF forming. (a)(b) Equivalent stress distributions; (c)‒(e) directional stress distributions
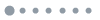
Fig. 12. Maximum stress versus scanning speed (left) and laser power (right) for Gaussian and flat-top laser beams at a scanning spacing of 0.112 mm
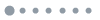
Fig. 13. Overall residual stress distributions and directional stress distributions generated by high-energy density Gaussian and flat-top laser beams at the end of 100 s LPBF forming. (a)(b) Equivalent stress distribution maps; (c)‒(e) directional stress distribution maps
|
Table 1. Composition of 316L stainless steel[34]
|
Table 2. Parameters for numerical simulation

Set citation alerts for the article
Please enter your email address