Author Affiliations
1State Key Laboratory of Modern Optical Instrumentation, College of Optical Science and Engineering, Zhejiang University, Hangzhou 310027, China2Research Center for Humanoid Sensing, Zhejiang Lab, Hangzhou 311121, Chinashow less
Abstract
Flexible optical sensors have been an emerging paradigm for applications in robotics, healthcare, and human–machine interfaces due to their high sensitivity, fast response, and anti-electromagnetic interference. Recently, Marques reports a bioinspired multifunctional flexible optical sensor (BioMFOS), achieving a forces sensitivity of 13.28 μN, and a spatial resolution of 0.02 mm. The BioMFOS has a small dimension (around 2 cm) and a light weight (0.8 g), making it suitable for wearable application and clothing integration. As proof-of-concept demonstrations, monitoring of finger position, trunk movements, and respiration rate are realized, implying their prominent applications in remote healthcare, intelligent robots, assistance devices teleoperation, and human-machine interfaces.Experimentally, the BioMFOS can detect forces in the μN range, making it promising in a wide range of critical applications. By analyzing four radial element’s signals, the spatial resolution is about 0.02 mm. Compared with inertial measurement unit, the BioMFOS achieved a correlation coefficient higher than 0.9, indicating the capability of the orientation detection in 3D plane, such as movement analysis and classification applications. For example, when a BioMFOS is positioned on the top of the user’s hand, the finger positions can be recognized based on the sensors’ signal variations. As it does not need additional accessories and is not directly connected to the user’s joints, the BioMFOS provides comfort for the user. Moreover, the authors demonstrate an application of cloth integrated BioMFOS for trunk’s orientation and respiration rate sensing. This advantageous result indicates that the BioMFOS can be employed on the continuous assessment of elderly with fall risk as well as activity monitoring in different healthy or injured subjects. To mitigate the impact of transverse forces or pressures applied in the top plane of the BioMFOS on the 3D orientation assessment, a protective cover was added to the sensor structure, which makes the BioMFOS robust and reliable for practical applications. Therefore, the BioMFOS opens new avenues for developing novel human-machine interface, high performance robotic tactile units, compact biomechanical analysis devices, and remote healthcare systems.
In a recently published paper in Opto-Electronic Advances, Carlos Marques and his colleagues at University of Aveiro and Federal University of Espírito Santo report a bioinspired multifunctional flexible optical sensor (BioMFOS) as an ultrasensitive tool for force (intensity and location) and orientation sensing20. Inspired by the spider web, the authors design and fabricate a frame structure with radial and frame elements using so-called micro-opto-electro-mechanical systems. In this work, polydimethylsiloxane (PDMS) and photocurable resins that have high refractive index contrast (1.43 vs. 1.50), excellent viscoelasticity and high transparency over a wide spectral range, are used as the cladding and core, respectively. As shown in Fig. 1(a), the photocurable resin core is fabricated using stereolithography 3D printing technique. To form a core/cladding structure, the photocurable resin core was placed inside a container filled with the PDMS resin, and followed by a thermal curing. As shown in Fig. 1(b), the core/cladding structure with eight radial elements is integrated with a PDMS packaged battery-LED assembly, which works as both light source and proof mass. In this case, the force applied at different locations of the BioMFOS can be detected through the optical signal variation on the sensor due to its viscoelastic response. The as-fabricated BioMFOS has a small dimension (around 2 cm) and a light weight (0.8 g), making it suitable for wearable application and clothing integration.
Recently, flexible optical waveguides made from elastic polymer have been intensively explored owing to their excellent physiomechanical properties and sensing performance together with low cost, reliability and potential for large scale fabrication4, 11-14. Typically, elastic polymer waveguides with a core-cladding structure are fabricated using molding, coextrusion or dip coating methods15. By measuring the output intensity of the waveguide, the exerted force or deformation can be obtained. For instance, a soft prosthetic hand equipped with multiple flexible optical sensors can feel the shape and softness of tomatoes16. The other prominent example is a stretchable distributed fiber-optic sensor enabled glove, which can reconfigure all types of finger joint movements and external presses simultaneously17. It is worth noting that most of the reported flexible optical sensor using a one-dimensional structure, which is difficult to sense the force and orientation simultaneously. To address this issue, one can employ fiber array to construct a diffuse light field, which can be decoupled through machine learning techniques18, or use two flexible fibers with a crossed-over layout, to form a multiaxis sensor19. However, the relatively large size of these sensors may limit their practical applications in wearable sensors or space confined scenarios.
Over the past decade, we have witnessed the rapid development in the flexible sensor for applications in personal healthcare, smart robots, and human–machine interfaces1-3. As an alternative to electronic skin (e-skin) sensors, considerable efforts have been made to develop the flexible optical sensor due to the high sensitivity, fast response, electrical safety, free of electromagnetic interferences, and potential for miniaturization4, 5. For example, optical micro/nanofiber (MNF) enabled flexible sensors have achieved a pressure sensitivity of 1870 kPa−16, a fast temporal frequency response up to 30 kHz7, and a small footprint suitable for minimally invasive surgery8. Based on the MNF tactile sensors, smart textiles for human–machine interaction9, and soft robotic skin for multifunctional humanoid tactility10 have been realized. Usually, the fabrication of these MNF sensors relies on individual micromanipulation of tiny MNFs, posing a challenge to their mass production and applications in daily life.
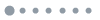
Figure 1.(a) Schematic representation of the core/cladding fabrication using stereolithography 3D printing technique. (b) Representation of the batteries and μLED assembly in the structure.