
- Chinese Optics Letters
- Vol. 20, Issue 5, 051401 (2022)
Abstract
1. Introduction
The generation of short
A free-running
2. Experimental Apparatus
The experimental devices used in this study are illustrated in Fig. 1. The
Sign up for Chinese Optics Letters TOC. Get the latest issue of Chinese Optics Letters delivered right to you!Sign up now
Figure 1.Schematic of the experimental device.
A generated pulse was split using a spectroscope (
3. Theoretical Model
3.1. Six-temperature model
The theoretical models describing the
According to the 6-T model, the magnitudes of energy density in the
The laser light intensity consists of three parts: the contribution of stimulated radiation, the contribution of spontaneous radiation, and the attenuation caused by loss.
The detailed rate equations describing energy relaxation between different levels can refer to the works by former researchers[
The output power can be expressed as
3.2. Theoretical simulation
Because it is difficult to achieve analytical solutions of rate equations, the fourth-order Runge–Kutta algorithm was adopted to calculate the numerical values balancing the accuracy and efficiency. The specific algorithm appropriate for pulsed
The simulated weighted forms are presented as follows:
The main parameters (the gas pressure was considered as a variable) used in the program include:
4. Statistics and Discussion
Pulse width is closely related to factors such as total injection, pre-ionization intensity, gas pressure, and mixture proportion. Limited experimental conditions can be adopted for achieving a uniform glowing discharge in a large area at high atmospheric pressure. Thus, suitable mixture proportions and discharge parameters were determined through a series of statistical filtrations. In this work, the mixture proportion was
4.1. Waveform
Figures 3 and 4 depict the experimental and theoretical pulse forms, respectively, of 10P(20) at different pressures. In the vertical axis, the amplitude cell spacing is set as 20 mV in Fig. 3(a), 50 mV in Figs. 3(b) and 3(c), and 100 mV in Fig. 3(d). In the horizontal axis, the time cell spacing is set as 100 ns. Clearly, there was a significant increase in peak power with an increase in pressure and a reduction in pulse width. According to the formula
Figure 2.Six-temperature model CO2-N2-CO gas pump energy-level diagram.
Figure 3.Experimental pulse forms and amplitudes at different pressures: (a) 4 atm, 130 mV, (b) 5 atm, 280 mV, (c) 6 atm, 370 mV, and (d) 7 atm, 550 mV.
Figure 4.Simulated pulse forms at different pressures.
The theoretical results reflect the same tendency and predict an increase in pulse energy (see Table 1).
Gas pressure (atm) | Pulse width (ns) | Energy (mJ) |
---|---|---|
4 | 48.8 | 196.2 |
5 | 39.2 | 272.7 |
6 | 36.7 | 403.4 |
7 | 30.4 | 493.7 |
Table 1. Pulse Widths and Corresponding Energy Values at Different Gas Pressures
A comparison of the pulse compression effects at different pressures is plotted in Fig. 4. The experimental compression ratio at 4 atm was 56% of that at 7 atm, whereas the theoretical ratio was 55%.
The experimental pulse forms exhibited a tail-free shape unlike the theoretical forms, which probably causes a difference in the calculated pulse width. It should be noted that an empirical equation representing the density of pumping electrons was adopted in the 6-T model[
Experimental values of pulse width are related to many factors. Three main factors are mentioned below. Firstly, this uncertainty is owing to the electrical desynchrony of the discharging process controlled by high-voltage capacitors and switches. On the other hand, density of electrons has unavoidable fluctuations in the discharging process due to the stochastic plasma diffusion. Thirdly, theoretical models considered an ideal system without thermal deposition, while it commonly exists in real discharging cavities. These factors closely affect the rising and falling edges in the laser gain curve so that the pulse widths do have different values (see Fig. 5).
Figure 5.Theoretical and experimental pulse widths at different pressures [10P(20)].
The differences of the pulse shapes and widths between simulated and experimental ones may be a limitation of the current 6-T model.
4.2. Pulse width and pulse energy
As shown in Fig. 6, the pulse width varied with the frequencies of different output bands. This is essentially affected by the stimulated emission cross section of the upper and lower levels. The oscillating frequencies in the central portion exhibited a higher gain than those at the two ends of the same band. The threshold conditions for laser output are highly available at these preponderant frequencies and also at the abrupt rising edge of the pulse form and higher pulse energy. Consequently, the distributions of the pulse width and energy over the entire spectrum presented opposite-shaped graphs resembling a regular “V” and an inverted “V,” respectively.
Figure 6.Normalized pulse width and energy versus wavelength (7 atm).
4.3. Pulse width at different pressures
Figure 7 depicts the pulse width distributions for different output bands at various mixture pressures. With an increase in pressure, four statistical observations were made.
Figure 7.Pulse widths of 9R, 9P, 10R, and 10P versus wavelength.
5. Conclusion
In this work, by increasing the working pressure of a
In addition, three types of differences were discussed in the previous section, namely the statistical differences between the experimental and theoretical data, differences between the pulse width and pulse energy distributions, and differences between the pulse widths at different bands and different frequencies. First, it was revealed that the experimental results and theoretical simulations demonstrated corresponding regularity. Second, the distributions of pulse width and pulse energy exhibited opposite graph shapes. Third, the pulse width was compressed, and the differences between bands and frequencies diminished with an increase in the working pressure.
The scope of future work includes conducting more specific theoretical expressions connecting basic parameters with spectral distribution properties of pulse width, and a series of parametric optimizations to be carried out at higher pressures. Results of this paper will make further improvements in aspects such as mode selecting technique in continuously wavelength tunable single longitudinal mode lasers,
References
[1] D. Holder, A. Leis, M. Buser, R. Weber, T. Graf. High-quality net shape geometries from additively manufactured parts using closed-loop controlled ablation with ultrashort laser pulses. Adv. Opt. Technol., 9, 101(2020).
[2] H. Büttner, K. Michael, J. Gysel, P. Gugger, S. Saurenmann, G. de Bortoli, J. Stirnimann, K. Wegener. Innovative micro-tool manufacturing using ultra-short pulse laser ablation. J. Mater. Process. Technol., 285, 116766(2020).
[3] B. Huis in ’t Veld, L. Overmeyer, M. Schmidt, K. Wegener, A. Malshe, P. Bartolo. Micro additive manufacturing using ultra short laser pulses. CIRP Ann. Manuf. Technol., 64, 701(2015).
[4] P. P. Geiko, A. Tikhomirov. Remote measurement of chemical warfare agents by differential absorption CO2 lidar. Opt. Mem. Neural Netw., 20, 71(2011).
[5] D. C. Dumitras, S. Banita, A. M. Bratu, R. Cernat, D. C. A. Dutu, C. Matei, M. Patachia, M. Petrus, C. Popa. Ultrasensitive CO2 laser photoacoustic system. Infrared Phys. Technol., 53, 308(2010).
[6] P. P. Geiko, A. Tikhomirov. Remote measurement of chemical warfare agents by differential absorption CO2 lidar. Opt. Mem. Neural Netw., 20, 71(2011).
[7] S. Nikiforov, Y. Simanovsky, A. Pento, K. Moshkunov, N. Gorbatova, S. Zolotov, S. Alimpiev. Pulsed transverse discharge CO2 laser for medical applications. International Conference Laser Optics (LO)(2016).
[8] R. H. M. A. Schleijpen, F. J. M. van Putten. Using a CO2 laser for PIR-detector spoofing. Proc. SPIE, 9989, 99890K(2016).
[9] Y. Zhang, H. Wang, L. Liu, Y. Ma, B. Shen, G. Zhang, M. Huang, A. Bonasera, W. Wang, J. Xu, S. Li, G. Fan, X. Cao, Y. Yu, C. Fu, J. He, S. Zhang, X. Hu, X. Li, Z. Hao, J. Wang, H. Xue, H. Fu. Primary yields of protons measured using CR-39 in laser-induced deuteron–deuteron fusion reactions. Nucl. Sci. Tech., 31, 62(2020).
[10] S. S. Perrotta, A. Bonasera. Fusion hindrance effects in laser-induced non-neutral plasmas. Nucl. Phys. A, 989, 168(2019).
[11] R. Snyder. A proliferation assessment of third generation laser uranium enrichment technology. Sci. Glob. Sec., 24, 68(2016).
[12] V. K. Saini, S. Talwar, V. V. V. Subrahmanyam, S. K. Dixit. Laser assisted isotope separation of lithium by two-step photoionization using time of flight mass-spectrometer. Opt. Laser Technol., 111, 754(2019).
[13] J. C. Balzer, T. Schlauch, A. Klehr, G. Erbert. High peak power pulses from dispersion optimized mode-locked semiconductor laser. Electron. Lett., 49, 838(2013).
[14] Y. R. Yuzaile, N. A. Awang, N. U. H. H. Zalkepali, Z. Zakaria, A. A. Latif, A. N. Azmi, F. S. Abdul Hadi. Pulse compression in Q-switched fiber laser by using platinum as saturable absorber. Optik, 179, 977(2019).
[15] H. V. Bergmann, F. Morkel. Continuously wavelength tunable high pressure CO2 lasers. Proc. SPIE, 9255, 92551Y(2015).
[16] J. Gilbert, J. L. Lachambre, F. Rheault, R. Fortin. Dynamics of the CO2 atmospheric pressure laser with transverse pulse excitation. Can. J. Phys., 50, 2523(1972).
[17] K. J. Andrews, P. E. Dyer, D. J. James. A rate equation model for the design of TEA CO2 oscillators. J. Phys. E, 8, 493(1975).
[18] O. Richter, R. Seppelt, D. Sndgerath. Computer Modeling(2006).
[19] J. N. Elgin. Computer modeling of gas lasers. Electron. Power UK, 25, 441(1979).
[20] M. Kimmit. Book Review: The CO2 laser. By W. J. Witteman. Springer Series in Optical Sciences, Vol. 53. Springer-Verlag, 1987. 309 pp. Price: DM 98 (hard cover). Opt. Lasers Eng., 11, 66(1989).
[21] A. R. Davies, K. Smith, R. M. Thomson. TLASER—a CO2 laser kinetics code. Comput. Phys. Commun., 10, 117(1975).
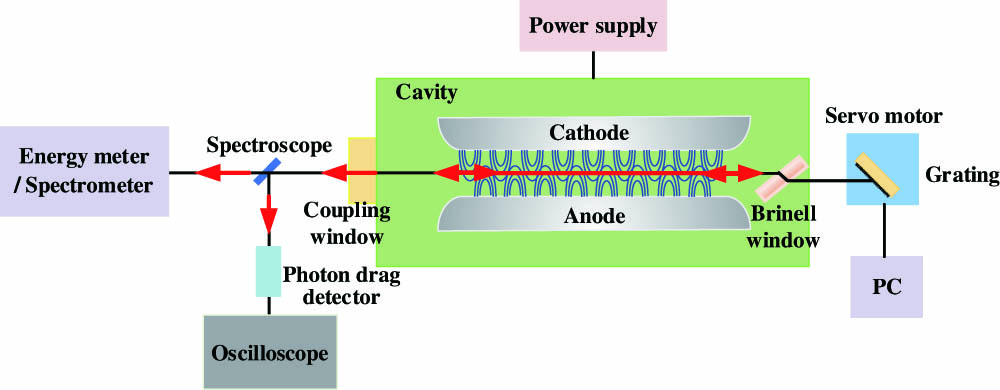
Set citation alerts for the article
Please enter your email address