
- High Power Laser and Particle Beams
- Vol. 32, Issue 5, 054004 (2020)
Abstract
LEBT is one of the key components of C-ADS proton linac. It starts from the exit of the ECR and ends with the RFQ entrance. LEBT mainly consists of two groups of solenoid with two steering magnets, two diagnostic chambers, a limited cone, an electron trap, and a beam chopper[
During the online beam commissioning of the superconducting cavity from low power to high power in the continuous-wave (CW) mode, the beam from the ECR is required to be continuously adjustable. In addition, the focusing of solenoid at the LEBT requires a round beam and the aberrations of the solenoid to the beam should be eliminated[
At 2011, Chinese Academy of Sciences (CAS) started the “Strategic Priority Research Program (Category A)” project named “Future Advanced Nuclear Fission Energy”[
1 The principle and structure design of the adjustable aperture
Beam matching between different acceleration segments is important to reduce beam losses and emittance growth. The mismatch from the LEBT is one of the main sources of beam losses in the RFQ. The beam losses lead to the thermal deformation of the RFQ electrode surface and then causes radio frequency arcing, which reduces the stability of the long-term operation of the RFQ[
1) The adjustable aperture needs to satisfy the round beam.
2) The beam current can be adjusted continuously on line.
3) Although for the beam commissioning, the beam power at the LEBT was determined to be 350 W (35 keV, 10 mA), the adjustable aperture should be able to withstand a heat load of 1 kW to allow for equipment upgrades in future.
Based on the above requirements, a novel core component of the adjustable aperture with cooling water made of 304 stainless steel was designed, the schematic diagram of the core component is shown in
Figure 1.The schematic diagram of the core component for adjustable aperture
The adjustable aperture is scheduled to install on the CF100 flange of C-ADS LEBT test chamber. The whole aperture structure is very compact and includes a CF100 flange, a bearing seat, a support frame, two rotating cores, water-cooling stepped shaft components and driving parts. The detailed structure is shown in
Figure 2.The structure diagram of the adjustable aperture
1.1 Vacuum seal
The operation of the accelerator is inseparable from the vacuum environment. Thus, the assembly of adjustable aperture to vacuum chamber must meet the high vacuum requirement for accelerator, and the vacuum inside the LEBT should be 10−4~10−5 Pa. Since the two stepped shafts of the aperture transfer relative rotation from the atmosphere to the vacuum chamber, the design for a dynamic seal for such high vacuum is always challenging. As a solution, a J-shaped dynamic seal structure was adopted, as shown in
1.2 Actuating device
The actuating device consists of a servo motor, an absolute rotary encoder, a synchronous pulley, a synchronous belt, a taper-lock, a straight spur gear and a transmission shaft. The servo motor transmits the power to the transmission shaft through synchronous belt, the taper-locks are installed on the transmission shafts, and the taper-locks are equipped with gears, which drive the mirror rotation of the transmission shafts through gear engagement. The rotation of the rotating cores is under control of servo motor, the system adopts closed-loop control, the positioning accuracy of rotation can be 0.5° without repeating location accumulation error.
1.3 Design and strength analysis of support
The support is bolted onto the CF100 flange for supporting and fastening the adjustable aperture components. Its material is 304 stainless steel, the thickness of the round plate on the mounting surface, the side plates, the middle rib plate and the end bearing seat are 12 mm, 6 mm, 4 mm and 12 mm, respectively. The load of the support mainly comes from its own weight, the weight of two rotating cores, and the weight of the water-cooling shaft components. According to the statics analysis and calculation, the equivalent weight on the support is about 6 kg, and the static load is about 60 N. The end bearing seat is connected to the ends of two side plates by screws. Its loads consist of radial pressure p1 and uniform axial pressure p2 and concentrate on the two bearing bores. p0 is the uniform radial load of two bearing bores. The specific calculation is shown in the following three equations.
Where
Figure 3.ANSYS simulation result of support
1.4 Thermo-mechanical analysis and manufacturing
The proton beam bombards the rotating cores and the beam power is dissipated on them as heat. Without proper cooling, the temperature of the rotating cores would rise continuously and eventually cause the deformation of the rotating cores. Due to the tight fitting between the two cores, thermal deformation will cause the two cores to be stuck and unable to rotate. Thus, it is important to analyze the heat flow on the cores with the beam power and water cooling taken into consideration.
On the transverse directions, the proton beam from ECR of C-ADS proton linac follows the Gaussian distribution. Calculated by the software SRIM, it was found that the penetration depth of 35 keV proton beam in 304 stainless steel is about 0.2 μm. Therefore it can be assumed that the beam power would be completely deposited on the surface of the rotating cores. The Gaussian surface heat source model is used as the heat source model of the proton beam bombarding the cores, the expression is
where q(r) is the heat flow of formation at radius r, P is beam power, R is beam spot radius.
Reynolds number is the characterization for the dimensionless number of fluid flow situation, used to determine laminar or turbulent, as
where ρ is fluid density, v is fluid flow velocity, d is the channel diameter and µ is viscosity coefficient.
The average speed of cooling water flow in the LEBT is 3 m/s, resulting in a turbulent flow in the water pipe. In this case, ANSYS Fluent was employed to calculate the cooling process, and the standard k-ε model in the turbulence model analysis was used for simulation.
In the worst scenario, the boundary conditions for heat simulation go as follows: 1) The beam power is 1 kW (current value is 350 W, may upgrade to 1 kW in the near future); 2) The 3 times of RMS beam radius is 20 mm, the aperture is completely closed; 3) The water temperature at inlet is 20 ℃; 4) The average velocity of cooling water is 3 m/s; 5) The Gaussian heat source distribution was added with user-defined program UDF.
As shown in
Figure 4.Temperature distribution and thermal deformation of the rotating core
2 Simulation and test of the adjustable aperture
For the superconducting linear accelerator of C-ADS, it is necessary to realize beam commissioning from low power to high power in CW mode. In practice, increasing the beam loading from low beam current to high beam current is an effective commissioning scheme. The LEBT is the main section for controlling the beam current and beam quality, the beam dynamics of the LEBT was studied in Ref.[
2.1 Simulation of the adjustable aperture
The beam dynamics simulation of the LEBT with aperture in the CW mode was carried out. The adjustable aperture was located at the 0.6 m of the LEBT from the ion source beam extraction aperture. The space charge compensation (SSC) was considered in beam dynamics simulation, and the SSC factor was 90%. In
Figure 5.The envelope diagram and beam reduction of LEBT with adjustable aperture
The beam phase space and real space plots at the adjustable aperture are shown in
Figure 6.Beam phase space and real space plots at the adjustable aperture
The beam parameters at the outlet of the LEBT are shown in
emittance | Twiss | Twiss | emittance | Twiss | Twiss | |
before scraping | 0.207 | 0.908 | 0.047 | 0.207 | 0.910 | 0.047 |
after scraping | 0.173 | 1.120 | 0.058 | 0.173 | 1.110 | 0.058 |
Table 1. The beam parameters at the outlet of the LEBT
2.2 Test of the adjustable aperture
Figure 7.The adjustable aperture
Figure 8.Test site of the aperture
The actual beam transmission through the adjustable aperture was tested at the LEBT of C-ADS with continuous beam of 35 keV and 10 mA. The test site is shown in
Figure 9.Test results of the aperture
3 Conclusion
The mechanical design, simulation and test of an adjustable aperture, which will be installed in the low energy beam transport line of C-ADS, were performed at Institute of Modern Physics (IMP). The aperture structure is able to realize continuous modulation of beam current during the online accelerator tuning and to satisfy the round beam shape. The mechanical and heat analyses show the aperture is capable of long time stable operation under 1 kW CW proton beam. In general, this adjustable aperture provides a convenient beam tuning method for the proton linear accelerator, which can satisfy the stable and reliable operation of C-ADS linear accelerator online.
References
[1] Zhan Wenlong, Xu Hushan. Advanced fission energy program-ADS transmutation system[J]. Bulletin of Chinese Academy of Sciences, 27, 375-381(2012).
[6] Yang Yao, Zhang Zimin, Zhang Wenhui. Study on beam emittance growth induced by spherical aberration of solenoid lens[J]. Atomic Energy Science and Technology, 47, 2336-2340(2013).
[7] Celona L, Allegra L, Amato A, et al. Preliminary commissioning results of the proton source f ESS at INFNLNS[C] Proc of IPAC. 2016: 26282631.
[8] Eshraqi M, Danared H, Jansson A, et al. ESS linac beam physics design update[C] Proc of IPAC. 2016: 947950.
[9] Weissman L, Berkovits D, Arenshtam A. SARAF phase I linac in 2012[J]. Journal of Instrumentation, T05004(20149).
[10] Kai D, Flian K, Christian P. Perfmance of the SARAF ion source[C] Proc of PAC07, 2007, TUPAN009: 14071409.
[11] Weissman L, Berkovits D, Eliyahu I, et al. The state of the SARAF LINAC Project[C] Proc of LINAC. 2010: 679683.
[12] Wu Qi, Jia Huan, Ma Hongyi. Research of emittance matching on the low energy beam transport line for ADS proton LINAC[J]. Nuclear Physics Review, 32, 5-9(2015).
[13] Chen Weilong. LEBT design based on beam loss control[D]. Beijing: University of Chinese Academy of Sciences, 2016
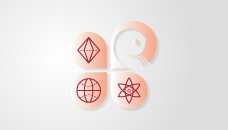
Set citation alerts for the article
Please enter your email address