
- Chinese Optics Letters
- Vol. 14, Issue 12, 120007 (2016)
Abstract
Optical fiber communications experienced rapid development, particularly in the last 30 years, after Kao
The opportunities provided by FBGs inscribed in standard SMFs and specialty optical fibers are of huge importance to the communications, sensors, and industrial processing industries. FBGs are widely used as wavelength lockers, optical filters, dispersion compensators, reflectors, gain-flattening filters, add/drop devices, numerous kinds of sensors, and fiber lasers in these industries. FBGs are normally fabricated in SMFs by laterally irradiating the core of the fiber with intense UV light[
Figure 1.Schematic of FBG imprinted in an SMF by the phase-mask technique with a scanning UV laser beam.
When a broadband light source is launched into an FBG, a specific wavelength (Bragg wavelength) will be reflected back with a reflectance that depends on the strength of the FBG. The Bragg wavelength is determined by
Sign up for Chinese Optics Letters TOC. Get the latest issue of Chinese Optics Letters delivered right to you!Sign up now
The many unique features and advantages of FBGs allow FBG-based sensors to be deployed in numerous sensing applications, such as in structural health monitoring of civil structures, condition monitoring of railways, physical parameter measurements in oil and gas, and in medical devices. In this Review, we review some novel FBG sensors for oil and gas applications, successful applications of FBG sensing networks for railway monitoring, and polymer optical fiber Bragg grating (POFBG) sensors that have very promising prospects in wearable medical applications.
FBG sensors can be used in very harsh environments and are being deployed as down-hole sensors in the oil and gas industry to measure temperature, pressure, and flow rate. An FBG inscribed in an SMF is very sensitive to temperature (
With the advent of microstructured optical fibers (MOFs) in the 1990s, the capability of fiber-optic sensors has been greatly expanded in terms of sensitivity, resolution, and accuracy. Pressure sensitivity based on an FBG written in an MOF can be enhanced, for example, a higher pressure sensitivity of 12 pm/MPa using a grapefruit MOF[
Figure 2.(a) SEM photo of a single-ring supporting MOF and (b) the pressure response measured using an FBG on this fiber[
An FBG inscribed in a specially doped SMF was developed to measure liquid flow rate at elevated temperatures. We demonstrated that optical fibers doped with cobalt are very efficient in converting light energy to heat and exploited this effect to develop an anemometer. The resolution of the FBG-based anemometer to measure air flow is 0.012 m/s for flow rates of 2 to 8 m/s[
Figure 3.(a) Schematic figure of the fluidic flow sensor based on an FBG written on an SMF and
Obviously, long-distance pressure and flow measurements with these small FBG-based SMF sensors can be realized, which is an essential requirement in down-hole applications. Besides pressure and flow measurements, leakage detection of pipelines was successfully implemented with FBG sensing technology[
The increasing demands for safety, reliability, and efficiency in the railway industry around the world call for the adoption of proactive or preventive maintenance strategies. FBG sensors can be installed on the rail tracks[
Figure 4.Schematic figure of FBG sensors installed on the track of railway, where the inset shows the measured strain induced by the wheel.
Compared with the traditional axle counters used in the railway system, which is electrical, FBG sensors are immune to EMI. This is important for sensors employed in railway applications, where most of the equipment and trains operate at a very high voltage. The capability of multiplexing a large number of FBG sensors in a single strand of fiber over a long distance provides an important feature that no other type of sensor possesses. Furthermore, FBG sensors along the fiber can measure a wide variety of different parameters, such as temperature, strain, acceleration, vibration, and weight. The unique features of FBG sensing networks permit the realization of a flexible and cost-effective monitoring system for many railway applications[
Figure 5.Rail track-based FBG sensing network for monitoring of various critical conditions of moving trains[
A train-borne system using a network of FBG-based sensors was developed to monitor critical components of bogies, car bodies, etc. More importantly, conditions of overhead power lines and rail tracks of the entire railway links can be monitored by passenger trains, allowing monitoring to be carried out during service hours. Similar systems have been installed in the Netherlands and Singapore to monitor catenary systems and rail tracks, respectively.
FBG sensing technology has proven to be extremely effective for railway monitoring. The FBG sensing information is wavelength-coded, provides self-referencing, and is virtually immune to intensity fluctuations. FBGs are reflective sensors whose signals can be obtained at either end of the sensors, providing redundancy in the sensing networks. These unique features are particularly important for industries where safety and reliability are major concerns, such as railways.
FBGs are deployed in numerous medical applications because of their small size, non-electrical conductivity, and multi-point and multi-parameter-sensing capabilities. These features, coupled with the fibers’ immunity to EMI/radio frequency interference (RFI), make FBG sensors ideal for diagnostic imaging with magnetic resonance imaging (MRI) or computed tomography (CT) systems. FBGs are being used as force sensors to measure deflection and force on needles during MRIs[
Some of the latest development efforts are in smart fabrics to measure cardiac and respiratory rhythms and for the prevention of sudden infant death syndrome in newborns. A particularly interesting development being investigated by researchers at Shinshu University is the use of one FBG sensor attached on the wrist to measure the vital signs of humans[
The measured pulse wave in form of wavelength shift is shown in Fig.
Figure 6.(a) The pulse wave of filter processing in a wrist, (b) the predicted results of SBP, and (c) the predicted results of DBP in the wrist (© [2015] IEEE. Reprinted, with permission from Ref. [
However, the aforementioned FBG sensors employed in wearable medical applications are inscribed in glass optical fibers that are not easy to weave into fabrics and that break easily. On the other hand, FBGs inscribed in POFs would be an attractive option. POFs are highly flexible and tolerant of sharp bends, but the single-mode POF necessary for writing FBGs is not commercially available, and writing FBGs in POFs requires a much longer UV irradiation time than in silica fibers. A single-mode POF is difficult to fabricate due to the diffusion of the core dopant to the cladding, making it difficult to control the fiber core’s refractive index and diameter. New materials such as TOPAS and, more recently, ZEONEX were successfully used to make single-mode POFs[
In conclusion, the applications of optical fibers have extended beyond optical fiber communications since Charles Kao proposed the use of low-loss glass optical fibers in communications. The many unique features of optical fibers make them attractive to be used as sensors in many industrial applications. In this Review, we gave a review of the industrial applications of FBG sensors in oil and gas, railways, and medicine. These industries have benefitted tremendously from FBG sensors in providing continuous monitoring to ensure efficient, safe, and reliable operation. Research and development are needed to extend the fiber sensors’ capabilities, including sensitivity, stability, and multi-functional to other industries. As future prospects, for example, FBGs inscribed on special optical fibers with microstructures are supposed to extend the resonant frequency of vibration for accelerometers, which are vital to improving the performance of railway monitoring. Novel materials of fabricating optical fibers, such as photosensitive dopants for POFs, also provide the opportunity for utilizing POFBGs in biomedical detection; they show higher sensitivity and are more biocompatible compared with silica FBGs. Additionally, as the development of a miniature interrogation based on interferometry, the signal detection of FBGs can be implemented on tiny chips. It is possible to integrate the wireless modules on a chip, which enables the transmission of FBG signals via remote techniques and thus opens the door for wearable and movable devices based on FBGs. Optical fiber sensors coupled with wireless electronics sensors could form a ubiquitous sensor network to play an important role in smart cities to ensure resources are efficiently and effectively utilized.
References
[1] K. Kao, G. Hockham. Proc. IEE, 113, 1151(1966).
[2] K. O. Hill, Y. Fujii, D. C. Johnson, B. S. Kawasaki. Appl. Phys. Lett., 32, 647(1978).
[3] G. Meltz, W. W. Morey, W. H. Glenn. Opt. Lett., 14, 823(1989).
[4] Philip St. J. Russell. J. Lightwave Technol., 24, 4729(2006).
[7] Y. Koike, K. Koike. J. Polym. Sci. Part B Polym. Phys., 49, 2(2011).
[8] T. Hayashi, T. Taru, O. Shimakawa, T. Sasaki, E. Sasaoka. 2011 Optical Fiber Communication Conference and Exposition and the National Fiber Optic Engineers Conference, 1(2011).
[9] K. O. Hill, G. Meltz. J. Lightwave Technol., 15, 1263(1997).
[12] M. Xu, L. Reekie, Y. Chow, J. P. Dakin. Electron. Lett., 29, 398(1993).
[13] L. K. Cheng, W. Schiferli, R. A. Nieuwland, A. Franzen, J. J. den Boer, T. H. Jansen. Proc. SPIE, 7753, 77536V(2011).
[14] C. Wu, B.-O. Guan, Z. Wang, X. Feng. J. Lightwave Technol., 28, 1392(2010).
[15] L. Htein, Z. Liu, H.-Y. Tam. Proc. SPIE, 9916, 99161R(2016).
[17] S. Gao, A. P. Zhang, H.-Y. Tam, L. H. Cho, C. Lu. Opt. Express, 19, 10124(2011).
[18] Q. Hou, W. Jiao, L. Ren, H. Cao, G. Song. J. Loss Prev. Process Ind., 32, 144(2014).
[20] H. Y. Tam, T. Lee, S. Ho, T. Haber. International Workshop on Structural Health Monitoring, 1824(2007).
[21] A. Cusano, H. Y. Tam, A. Cutolo, S. Y. Liu, J. Albert, S. L. Ho, T. K. Ho. Fibre Bragg grating sensors for Railway systems. Fiber Bragg Grating Sensors: Recent Advancements, Industrial Applications and Market Exploitation, 197(2011).
[22] F. Taffoni, D. Formica, P. Saccomandi, G. Di Pino, E. Schena. Sensors, 13, 14105(2013).
[24] K. M. Chung, Z. Liu, C. Lu, H.-Y. Tam. IEEE Photon. Technol. Lett., 24, 700(2012).
[25] Y. Katsuragawa, H. Ishizawa. IEEE International Instrumentation and Measurement Technology Conference Proceedings, 511(2015).
[27] R. Oliveira, L. Bilro, R. Nogueira. Opt. Express, 23, 10181(2015).
[28] H.-Y. Tam. 2014 OptoElectronics and Communication Conference and Australian Conference on Optical Fibre Technology (OECC/ACROFT’2014)(2014).
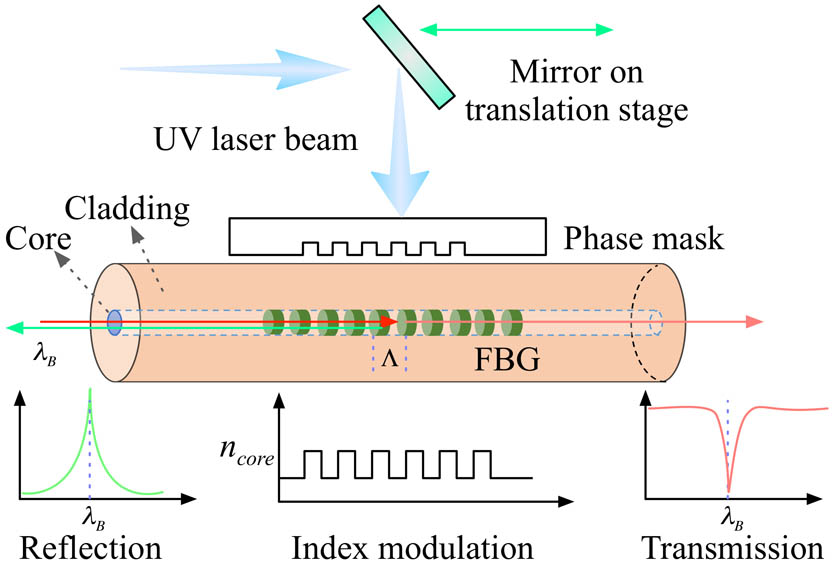
Set citation alerts for the article
Please enter your email address