Zikun Xia, Yucong Huang, Yongyue Huang, Long Wen, Qin Chen. Recent Progress in Optical Hydrogen Sensing Technology (Invited)[J]. Acta Optica Sinica (Online), 2024, 1(4): 0402001

Search by keywords or author
- Acta Optica Sinica (Online)
- Vol. 1, Issue 4, 0402001 (2024)

Fig. 1. Optical hydrogen gas sensing technologies
![Comparison of absorption spectra of different gases at a volume fraction of 1000×10-6 [31]. (a) Absorption spectrum of H2; (b) absorption spectra of H2O, CO2, CH4, CO, and NH3](/richHtml/aos_ol/2024/1/4/0402001/img_02.jpg)
Fig. 2. Comparison of absorption spectra of different gases at a volume fraction of 1000×10-6 [31]. (a) Absorption spectrum of H2; (b) absorption spectra of H2O, CO2, CH4, CO, and NH3
![TDLAS-based H2 sensing technology. (a) Mechanism of TDLAS-based gas sensing; (b) the first H2 sensing system based on TDLAS technique[50]](/Images/icon/loading.gif)
Fig. 3. TDLAS-based H2 sensing technology. (a) Mechanism of TDLAS-based gas sensing; (b) the first H2 sensing system based on TDLAS technique[50]
![PAS-based H2 sensing technology. (a) Mechanism of PAS-based gas sensing; (b) PAS-based H2 sensor with acoustic excitation[61]; (c) PAS-based H2 sensor with photoexcitation[62]](/Images/icon/loading.gif)
Fig. 4. PAS-based H2 sensing technology. (a) Mechanism of PAS-based gas sensing; (b) PAS-based H2 sensor with acoustic excitation[61]; (c) PAS-based H2 sensor with photoexcitation[62]
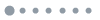
Fig. 5. Mechanism of Raman spectroscopy based H2 sensing technology
![Enhanced Raman spectroscopy based H2 sensing technology. Schematics of (a) V-shaped optical cavity[68] and (b) ultra-fine resonant cavity[70] used in the CERS techniques; (c) tapered optical fiber[71] and (d) hollow optical fiber[74] used in the FERS technique](/Images/icon/loading.gif)
Fig. 6. Enhanced Raman spectroscopy based H2 sensing technology. Schematics of (a) V-shaped optical cavity[68] and (b) ultra-fine resonant cavity[70] used in the CERS techniques; (c) tapered optical fiber[71] and (d) hollow optical fiber[74] used in the FERS technique
![Remote Raman spectroscopy based H2 sensing technology. (a) Mechanism of remote Raman spectroscopy technology; (b) compact remote Raman spectroscopy based H2 sensing system[81]; (c) multi-channel remote Raman spectroscopy based H2 sensing system with a photon counter[83]](/Images/icon/loading.gif)
Fig. 7. Remote Raman spectroscopy based H2 sensing technology. (a) Mechanism of remote Raman spectroscopy technology; (b) compact remote Raman spectroscopy based H2 sensing system[81]; (c) multi-channel remote Raman spectroscopy based H2 sensing system with a photon counter[83]
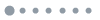
Fig. 8. Diagram of the interaction process between Pd and H2. (a) Distribution of H atoms in the Pd interstitial sites for different phases; (b) Pd hydride formation and desorption process under different H2 pressures
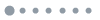
Fig. 9. Principle of H2 sensor based on SPR effect. (a) Mechanism of SPR H2 sensor based on metallic nanostructures; (b) schematic of direct and indirect nanoplasmonic sensing schemes
![Pd-based direct SPR sensors for H2 detection. (a) The first prism-coupled SPR H2 sensor[103]; (b) the first nanostructured SPR H2 sensor[104]; (c) SPR H2 sensor optimized with inverse design algorithms for nanostructures[110]](/Images/icon/loading.gif)
Fig. 10. Pd-based direct SPR sensors for H2 detection. (a) The first prism-coupled SPR H2 sensor[103]; (b) the first nanostructured SPR H2 sensor[104]; (c) SPR H2 sensor optimized with inverse design algorithms for nanostructures[110]
![Enhancement strategies for Pd-based direct SPR H2 sensors. (a) PdAu alloys based SPR H2 sensors[111]; (b) PdCo alloys based SPR H2 sensors[114]; (c) PMMA and PTFE polymer coated PdAu alloys based SPR H2 sensors[115]; (d) SPR H2 sensors consisting of Pd nanowire array and Au reflector[119]](/Images/icon/loading.gif)
Fig. 11. Enhancement strategies for Pd-based direct SPR H2 sensors. (a) PdAu alloys based SPR H2 sensors[111]; (b) PdCo alloys based SPR H2 sensors[114]; (c) PMMA and PTFE polymer coated PdAu alloys based SPR H2 sensors[115]; (d) SPR H2 sensors consisting of Pd nanowire array and Au reflector[119]
![Indirect Pd-based SPR H2 sensors. (a) SPR H2 sensors based on Pd nanocube‒Au nanosphere conbined structure[121]; (b) SPR H2 sensors with different Pd-Au nanodisk stacked structures[123]; (c) SPR H2 sensors based on Pd-Au core-shell structures[124]; (d) SPR H2 sensor composed of Pd film and Pd-Au nanograting structure[127]](/Images/icon/loading.gif)
Fig. 12. Indirect Pd-based SPR H2 sensors. (a) SPR H2 sensors based on Pd nanocube‒Au nanosphere conbined structure[121]; (b) SPR H2 sensors with different Pd-Au nanodisk stacked structures[123]; (c) SPR H2 sensors based on Pd-Au core-shell structures[124]; (d) SPR H2 sensor composed of Pd film and Pd-Au nanograting structure[127]
![Self-powered Pd-based SPR H2 sensors. (a) Miniaturized SPR H2 sensing system integrated with LED and detector[128]; (b) H2 sensor based on Pd-PUA nanogratings integrated with a photovoltaic cell[131]; (c) photovoltaic H2 sensor optimized by differential methods[132]](/Images/icon/loading.gif)
Fig. 13. Self-powered Pd-based SPR H2 sensors. (a) Miniaturized SPR H2 sensing system integrated with LED and detector[128]; (b) H2 sensor based on Pd-PUA nanogratings integrated with a photovoltaic cell[131]; (c) photovoltaic H2 sensor optimized by differential methods[132]
![H2 sensors based on other phase change materials. (a) H2 sensor based on Y-Mg alloy[138]; (b) H2 sensor based on nanoporous WO3 structure[144]; (c) H2 sensing system based on Pt nanoparticles decorated WO3 film[145]; (d) integrated H2 sensor based on a WO3 film[146]](/Images/icon/loading.gif)
Fig. 14. H2 sensors based on other phase change materials. (a) H2 sensor based on Y-Mg alloy[138]; (b) H2 sensor based on nanoporous WO3 structure[144]; (c) H2 sensing system based on Pt nanoparticles decorated WO3 film[145]; (d) integrated H2 sensor based on a WO3 film[146]
![Fabrication methods of various Pd nanostructures for H2 sensors. (a) Nanospheres lithography technology used in H2 sensing[112]; (b) Pd-decorated butterfly wing structure H2 sensor[148]; (c) H2 sensor based on one-dimensional nanograting structure on DVD[150]](/Images/icon/loading.gif)
Fig. 15. Fabrication methods of various Pd nanostructures for H2 sensors. (a) Nanospheres lithography technology used in H2 sensing[112]; (b) Pd-decorated butterfly wing structure H2 sensor[148]; (c) H2 sensor based on one-dimensional nanograting structure on DVD[150]
![FBG H2 sensors. (a) FBG H2 sensing detection principle diagram; (b) π-phase shift type FBG sensor with a local covered H2 sensitive layer[161]; (c) FBG sensor with straight trenches and spiral micro-pits structure[163]](/Images/icon/loading.gif)
Fig. 16. FBG H2 sensors. (a) FBG H2 sensing detection principle diagram; (b) π-phase shift type FBG sensor with a local covered H2 sensitive layer[161]; (c) FBG sensor with straight trenches and spiral micro-pits structure[163]
![Micromirror-based optical fiber H2 sensors. (a) Mechanism of micromirror-based optical fiber H2 sensing; (b) H2 sensor based on Mg70Ti30 alloy[167]; (c) H2 sensor based on polarization modulation[169]](/Images/icon/loading.gif)
Fig. 17. Micromirror-based optical fiber H2 sensors. (a) Mechanism of micromirror-based optical fiber H2 sensing; (b) H2 sensor based on Mg70Ti30 alloy[167]; (c) H2 sensor based on polarization modulation[169]
![M-Z interferometer H2 sensors. (a) Mechanism of M-Z interferometer sensor; (b) M-Z interferometer sensor with a tapered and expanded cone structure[177]; (c) M-Z interferometer sensor with an air microcavity[179]](/Images/icon/loading.gif)
Fig. 18. M-Z interferometer H2 sensors. (a) Mechanism of M-Z interferometer sensor; (b) M-Z interferometer sensor with a tapered and expanded cone structure[177]; (c) M-Z interferometer sensor with an air microcavity[179]
![H2 sensor based on F-P interferometer. (a) Sensor with a dual F-P cavity cascaded structure[183]; (b) F-P interferometer sensor based on Pd-decorated graphene structure[184]; (c) FBG and F-P cavity combined sensor[186]](/Images/icon/loading.gif)
Fig. 19. H2 sensor based on F-P interferometer. (a) Sensor with a dual F-P cavity cascaded structure[183]; (b) F-P interferometer sensor based on Pd-decorated graphene structure[184]; (c) FBG and F-P cavity combined sensor[186]
![Photoelectric H2 sensing technology. (a) Hedgehog-shaped SnO2-based resistive H2 sensor[189]; (b) Pd-decorated SnO2 nanoball resistive H2 sensor[190]; (c) FET-type sensor with dual ZnO and Pd catalytic layers[191]; (d) Schottky junction-type H2 sensor[192]](/Images/icon/loading.gif)
Fig. 20. Photoelectric H2 sensing technology. (a) Hedgehog-shaped SnO2-based resistive H2 sensor[189]; (b) Pd-decorated SnO2 nanoball resistive H2 sensor[190]; (c) FET-type sensor with dual ZnO and Pd catalytic layers[191]; (d) Schottky junction-type H2 sensor[192]
|
Table 1. Performance targets in stationary and automotive H2 safety sensors[20]
|
Table 2. Main performance parameters of various optical H2 sensors

Set citation alerts for the article
Please enter your email address