Liqun DU, Dejian KONG, Shuai WANG, Xiaoke CAI, Bingjiang GUO. Study on interfacial bonding strength during fabrication of micro inertial switch[J]. Optics and Precision Engineering, 2023, 31(10): 1464

Search by keywords or author
- Optics and Precision Engineering
- Vol. 31, Issue 10, 1464 (2023)

Fig. 1. Component diagram of microinertial switch

Fig. 2. Microelectroforming layer warped off
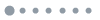
Fig. 3. Passivated film-Ni bonded layer system
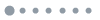
Fig. 4. Stainless steel -Ni bonded layer system
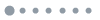
Fig. 5. Passivation film removal rate of 50% doping structure-Ni binding layer system
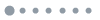
Fig. 6. Binding energy of the system varies with temperature under different passivation film removal rates
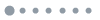
Fig. 7. Model of bonding layer system between transition metal and stainless steel substrate
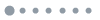
Fig. 8. Binding energy of the four systems varies with temperature
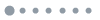
Fig. 9. Binding energy of Cu, Cr, Ti and Ni castings varies with temperature
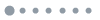
Fig. 10. Surface morphology of substrate at different time of electrolysis activation
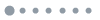
Fig. 11. Experimental structure of copper transition layer experiment
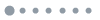
Fig. 11. Morphology of microelectroforming layer falls off is not fallingafter ultrasonic vibration
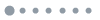
Fig. 12. Surface morphology of the substrate before and after Cu layer was prepared
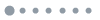
Fig. 13. Fabrication process of micro inertial switch
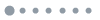
Fig. 14. Experimental apparatus for electrolytic activation
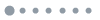
Fig. 15. Cu transition layer uniformly covering the surface of microstructure
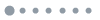
Fig. 16. Completed micro inertial switch
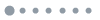
Fig. 17. Microswitch production process of the overall picture of the experimental piece
|
Table 1. Relationship between the mean value of binding energy of different systems
|
Table 2. Experimental parameters of electrolytic activation
|
Table 3. Measurement results of interface bonding strength in electrolysis activation experiment
|
Table 4. Measurement results of interface bonding strength of copper transition layer

Set citation alerts for the article
Please enter your email address