
- Chinese Optics Letters
- Vol. 21, Issue 1, 011406 (2023)
Abstract
Keywords
1. Introduction
Wideband tunable semiconductor lasers (TSLs) have played significant roles in many optical measurement and communication applications, including fiber sensing interrogators[1], gas-leaking detection systems[2,3], biomedical imaging systems[4], light detection and ranging (LiDAR) measurements[5,6], and wavelength division multiplexing (WDM) transmission systems[7]. Up to now, several TSLs with different structures have been developed, including the external cavity wavelength-tunable laser (ECTL), the wavelength-tunable vertical cavity surface emitting laser (VCSEL), the tunable laser based on distributed Bragg reflector (DBR) structure, and the tunable multi-wavelength laser array (MLA) based on multiple distributed feedback (DFB) lasers. The mechanical scheme of ECTL leads to relatively large footprint and slow tuning speed[8]. The tunable VCSEL has relatively wide spectral linewidth and low output power because of the mechanical microelectromechanical system (MEMS)[9]. The tunable DBR laser is mainly based on the Vernier effect, which has poor mode stabilization and mode hopping during the tuning process[10]. Among them, the tunable DFB-MLA has the advantages of good single-longitudinal-mode operations, narrow spectral linewidth, feasible monolithic integration, and simple wavelength-tuning scheme. The conventional tunable DFB-MLA is tuned by switching different lasers for coarse wavelength selection and then finely tuned by thermal-electric cooler (TEC) to realize continuous wavelength tuning. However, the TEC-based wavelength-tuning scheme is power-consuming, and its tuning speed is severely restricted[11]. Both the wavelength-tuning range and the tuning speed are critical features for TSLs in reducing complexity and cost and improving the performance of optical systems.
In this work, a novel DFB-MLA scheme with wide and fast wavelength-tuning capability is proposed and experimentally demonstrated. We present a
2. Principle and Design
The conventional tunable DFB-MLA consists of multiple DFB lasers, placed in parallel and monolithically integrated with an optical combiner[12]. However, the optical combiner introduces extra optical power loss and increases the chip size. Furthermore, it needs a heterogeneous integration technique and causes great complexity for the fabrication process. The in-series structure of the DFB-MLA can omit the combiner. However, the single-mode properties of the in-series MLA are vulnerable and easily deteriorated by the grating crosstalk and the reflections of other lasers[13]. Therefore, the designed wavelength spacing of the neighboring lasers needs to be larger than the stopband of the grating, which is typically 3.2 nm, to avoid grating interference[14].
Sign up for Chinese Optics Letters TOC. Get the latest issue of Chinese Optics Letters delivered right to you!Sign up now
In this Letter, we propose a 20-channel tunable laser array. The gratings of the 20 lasers are monolithically integrated into one chip using
Figure 1.Schematic of the 4 × 5 interleaving matrix-grating REC-DFB MLA (SCH-MQW, separate confinement hetero-structure multiple quantum well; BG, Bragg grating).
We use the REC technique to fabricate the DFB laser, which can precisely control the designed lasing wavelength and simplify the grating fabrications[13]. With this method, only one step of traditional micrometer (µm)-level photolithography and holographic exposure are needed to fabricate the laser gratings. High-order subgratings can be used to obtain equivalent phase shifts, and we choose the
We can use different sampling periods with the uniform seed grating to achieve different target lasing wavelengths. Then,
Transmission spectra of the five in-series element lasers (LD1, LD5, LD9, LD13, and LD17) on the same waveguide of the proposed
Figure 2.Transmission spectra of the designed five in-series gratings (LD1, LD5, LD9, LD13, and LD17) and the five transmission peaks marked with red triangles corresponding to the lasing modes of the five in-series element lasers.
Figure 3.Schematic of the (a) DFB laser packaging configuration and the (b) top view of the 4 × 5 interleaving matrix-grating REC-DFB laser array mounted on the submount integrated with heaters (NTC thermistor, negative temperature coefficient thermistor).
The thermal conductivity of submount and the thermal contact between the submount and the heatsink can both significantly influence the temperature of the laser chip via thermal simulations and heat conduction analysis[20]. To cover the 2.5 nm wavelength spacing of the proposed REC-DFB MLA, the lasing element laser’s temperature needs to increase by at least 25 K. We then adjust the currents of the integrated thin-film heaters on the AlN submount to study the wavelength-tuning effect through thermal simulations. The thin-film heaters on the submount are fabricated by sputtering a high-resistance film of tantalum nitride (TaN) under the conductor layer and selectively etching the resistor elements. The sizes of the standard AlN submount without heaters and the AlN submount integrated with 10 TaN thin-film heaters are both set as
Figure 4.Thermal simulations of the REC-DFB MLA chip’s steady-state temperature on the (a) standard AlN submount and the (b) optimized submount integrated with thin-film heaters, with laser injected current of 80 mA and heater injected current of 190 mA. Enlarged view of the temperature distributions for the REC-DFB MLA chip on the (c) standard AlN submount and the (d) submount integrated with thin-film heaters.
3. Experiment and Discussion
Figure 5 shows the microscopic photos of the fabricated
Figure 5.(a) Microscopic view of the 4 × 5 interleaving matrix-grating REC-DFB laser array chip; (b) top view and (c) magnified view of the fabricated 4 × 5 matrix-grating REC-DFB laser array chip on AlN submount integrated with TaN film heaters.
Figure 6(a) depicts the superimposed spectra of the 20 lasing element lasers when the SOA current, Y-branch optical combiner current, and laser current are 40, 50, and 80 mA, respectively. For the in-series element lasers, the 30 mA transparency currents were applied to all the lasers in front of the lasing element laser to suppress the material absorption. With the linear fitting results of the lasing wavelengths shown in Fig. 6(b), the proposed REC-DFB MLA chip has a nearly uniform wavelength spacing of 2.49 nm, and the maximum wavelength deviation is less than 0.37 nm.
Figure 6.(a) Superimposed lasing spectra of all 20 lasers when the laser current is 80 mA and (b) the lasing wavelength fitting for the 20 element lasers of the REC-DFB MLA, with the wavelength-fitting deviations of the 20 lasers depicted in the inset of (b).
Figure 7(a) shows the typical PI and IV diagram of the first four in-parallel lasers when the laser current (
Figure 7.(a) Typical PI and IV diagram of the four in-parallel lasers with SOA and optical combiner injection current of 20 mA and 50 mA. (b) Output powers of all 20 lasers with the SOA current varied from 0 to 100 mA as well as the optical combiner injection current of 50 mA and laser current of 80 mA (ILD, the injection current of laser; ISOA, the injection current of the semiconductor optical amplifier).
The tuning ranges of all 20 lasers of the REC-DFB MLA mounted on the standard AlN submount were subsequently measured. We recorded the corresponding wavelengths when the injection currents of each lasing element laser varied from 40 to 120 mA. The superimposed tuning spectra for the 20 lasers are shown in Figs. 8(a) and 8(b), with an average wavelength tuning of approximately 1.2 nm per laser.
Figure 8.Measured tuning spectra and current-wavelength relationships for the 20 lasers of the REC-DFB MLA mounted on the standard submount and the optimized submount with thin-film heaters, respectively.
As a comparison, we also measured the tuning ranges of the 20 lasers of the
Besides, we examined the repeatability of the proposed wavelength-tuning method using a narrowband fiber Bragg grating (FBG) by monitoring the reflection peak while sweeping the laser’s wavelength repeatedly. As shown in Fig. 9, the repeatability is measured to be approximately 0.003 nm after 16 measurements.
Figure 9.Experimentally measured central reflection wavelength of the same FBG for repeating wavelength-tuning experiments by 16 times.
Furthermore, we compared the tuning speeds based on TEC and based on the film heater on the submount for one element laser. The wavelength tuning was measured with a Mach–Zehnder interferometer (MZI)-based system[17]. The measured optical intensity fluctuations can indicate the real-time wavelength changes of the laser. As shown in Fig. 10, compared with the traditional wavelength-tuning scheme based on TEC, whose tuning speed is 1.8 s, the proposed scheme needs only 250 ms.
Figure 10.Experimentally measured tuning speed of the (a) TEC tuning scheme and (b) submount heater tuning scheme for 2.5 nm wavelength variations of one element laser using the MZI-based system.
4. Conclusion
In this work, we propose and experimentally demonstrate a wideband and fast tunable DFB laser array. The proposed DFB-MLA achieves good single-mode operation and uniform wavelength spacing via the REC technique, which can precisely control the grating phase. With the film heater on the submount, the wavelength-tuning range is widened to 2.5 nm for each element laser and realizes a whole 50 nm continuous wavelength-tuning range. The tuning speed is 7.2 times faster than that of TEC. The proposed wavelength-tuning mechanism is simple and compatible with existing DFB lasers. Furthermore, the wide wavelength tuning of the interleaving matrix DFB-MLA maintains good single-mode properties, which is promising for future distributed multi-sensor measuring applications.
References
[1] D. Liu, Q. Sun, P. Lu, L. Xia, C. Sima. Research progress in the key device and technology for fiber optic sensor network. Photonic Sens., 6, 1(2016).
[2] M. Lackner. Tunable diode laser absorption spectroscopy (TDLAS) in the process industries: a review. Rev. Chem. Eng., 23, 65(2007).
[3] Y. Fan, J. Xiao, Z. Shen, Y. Hao, J. Liu, K. Yang, Y. Yang, Y. Huang. 1.65 µm square-FP coupled cavity semiconductor laser for methane gas detection. Chin. Opt. Lett., 20, 061401(2022).
[4] J. G. Fujimoto, C. Pitris, S. A. Boppart, M. E. Brezinski. Optical coherence tomography: an emerging technology for biomedical imaging and optical biopsy. Neoplasia, 2, 9(2000).
[5] J. M. C. Amann. Phase noise limited resolution of coherent LIDAR using widely tunable laser diodes. Electron. Lett., 28, 1694(1992).
[6] C. Wang, Y. Zhang, J. Zheng, J. Li, Z. Sun, J. Shi, L. Li, R. Xiao, T. Fang, X. Chen. Frequency-modulated continuous-wave dual-frequency LIDAR based on a monolithic integrated two-section DFB laser. Chin. Opt. Lett., 19, 111402(2021).
[7] F. Delorme. Widely tunable 1.55-um lasers for wavelength-division multiplexed optical fiber communications. IEEE J. Quantum Electron., 34, 1706(1998).
[8] B. Mroziewicz. External cavity wavelength tunable semiconductor lasers: a review. Opto-Electron. Rev., 16, 347(2008).
[9] M. C. Y. Huang, K. B. Cheng, Y. Zhou, A. P. Pisano, C. J. Chang-Hasnain. Monolithic integrated piezoelectric MEMS-tunable VCSEL. IEEE J. Sel. Top. Quantum Electron., 13, 374(2007).
[10] M. Gotoda, T. Nishimura, Y. Tokuda. Widely tunable SOA-integrated DBR laser with combination of sampled-grating and superstructure grating. IEEE 19th International Semiconductor Laser Conference, SaA5(2004).
[11] L. A. Coldren, G. A. Fish, Y. Akulova, J. S. Barton, L. Johansson, C. W. Coldren. Tunable semiconductor lasers: a tutorial. J. Light. Technol., 22, 193(2004).
[12] H. Ishii, K. Kasaya, H. Oohashi, Y. Shibata, H. Yasaka, K. Okamoto. Widely wavelength-tunable DFB laser array integrated with funnel combiner. IEEE J. Sel. Top. Quantum Electron., 13, 1089(2007).
[13] Z. X. Sun, R. Xiao, Z. Su, K. Liu, Z. Hu, P. Dai, J. Lu, J. Zheng, Y. Zhang, Y. Shi, Y. Chiu, X. Chen. High single-mode stability tunable in-series laser array with high wavelength-spacing uniformity. J. Light. Technol., 38, 6038(2020).
[14] L. Li, S. Tang, J. Lu, Y. Shi, B. Cao, X. Chen. Study of cascaded tunable DFB semiconductor laser with wide tuning range and high single mode yield based on equivalent phase shift technique. Opt. Commun., 352, 70(2015).
[15] Y. Shi, S. Li, L. Li, R. Guo, T. Zhang, L. Rui, W. Li, L. Lu, T. Song, Y. Zhou, J. Li, X. Chen. Study of the multi-wavelength DFB semiconductor laser array based on the reconstruction-equivalent-chirp technique. J. Light. Technol., 31, 3243(2013).
[16] X. Chen. Precision photonic integration for future large-scale photonic integrated circuits. J. Semicond., 40, 050301(2019).
[17] K. Xu, P. Dai, Z. Sun, J. Lu, R. Xiao, Z. Su, T. Fang, Y. Shi, X. Chen. Improved range tunability of DFB lasers based on REC technique under injection current. IEEE J. Quantum Electron., 57, 2200107(2021).
[18] M. C. Amann, J. Buus. Tunable Laser Diodes(1998).
[19] G. Morthier, P. Vankwikelberge. Handbook of Distributed Feedback Laser Diodes(2013).
[20] P. Dai, Z. Sun, Z. Chen, J. Lu, F. Wang, H. Tong, R. Xiao, X. Chen. Enhanced tuning performance of in-series REC-DFB laser array. IEEE Photon. Technol. Lett., 33, 1337(2021).
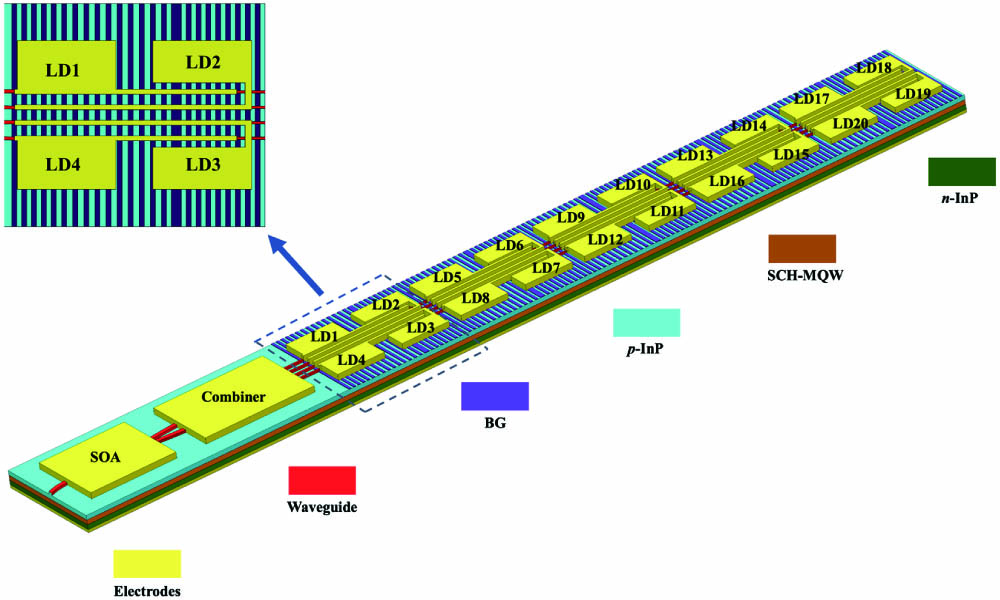
Set citation alerts for the article
Please enter your email address