Jinzhi Zhang, Anfeng Zhang, Hong Wang, Xiaoxing Zhang, Yuyue Wang. Microstructure and Anisotropy of High Performance TC4 Obtained by Micro Forging Laser Cladding Deposition[J]. Chinese Journal of Lasers, 2019, 46(4): 0402009

Search by keywords or author
- Chinese Journal of Lasers
- Vol. 46, Issue 4, 0402009 (2019)

Fig. 1. Schematic of micro forging assisted LCD system

Fig. 2. Relationships between micro-forging process parameters and surface residual stress of formed parts. (a) Forging speed and surface residual stress; (b) amplitude and surface residual stress; (c) forging times and surface residual stress
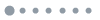
Fig. 3. Morphology of formed parts in different states. (a) Deposition state; (b) solution aging state; (c) micro forging-solution aging state
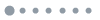
Fig. 4. Relationships between micro forging process parameters and equiaxed grain size. (a) Forging speed and equiaxed grain size; (b) amplitude and equiaxed grain size; (c) forging times and equiaxed grain size
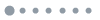
Fig. 5. Effect of amplitude on equiaxed grain size
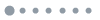
Fig. 6. Relationships between micro forging process parameters and surface roughness Ra of formed parts. (a) Forging speed and surface roughness; (b) amplitude and surface roughness; (c) forging times and surface roughness
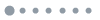
Fig. 7. Fracture morphology of formed parts in different directions after micro forging solution aging treatment. (a) xy direction; (b) z direction
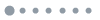
Fig. 8. Anisotropy of tensile properties of samples in different states
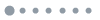
Fig. 9. Microstructures of formed parts in different states. (a) Deposition state; (b) solution aging; (c) micro forging-solution aging
|
Table 1. Main chemical composition of TC4 powder and TC4 substrate (mass fraction, %)
|
Table 2. Process parameters of micro forging
|
Table 3. Room-temperature tensile properties of formed parts in different states

Set citation alerts for the article
Please enter your email address