Guolong Wu, Yujie Huang, Zhenzhen Yang, Ye Wang, Liang Wang, Jianhua Yao. Electrochemical Anodic Dissolution Characteristics and Polishing Behavior Analysis of LDEDed 316L Stainless Steel in Different Forming Directions[J]. Chinese Journal of Lasers, 2025, 52(12): 1202204

Search by keywords or author
- Chinese Journal of Lasers
- Vol. 52, Issue 12, 1202204 (2025)

Fig. 1. Laser directed energy deposition (LDED) system

Fig. 2. Laser directed energy deposition. (a) Schematic; (b) physical drawing
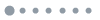
Fig. 3. Jet electrochemical polishing device diagram
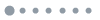
Fig. 4. Microstructures of different faces of 316L stainless steel formed by laser directed energy deposition. (a) Front face; (b) top face; (c) side face
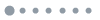
Fig. 5. XRD patterns of three different faces of 316L stainless steel formed by laser directed energy deposition
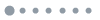
Fig. 6. EBSD maps of three faces of 316L stainless steel formed by laser directed energy deposition
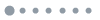
Fig. 7. OCP curves of three different faces of 316L stainless steel formed by laser directed energy deposition and the substrate
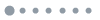
Fig. 8. Tafel polarization curves of three faces of 316L stainless steel formed by laser directed energy deposition and the substrate
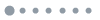
Fig. 9. EIS curves of three faces of 316L stainless steel formed by laser directed energy deposition and the substrate. (a) Nyquist diagram; (b) Bode diagram; (c) equivalent circuit diagram
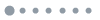
Fig. 10. Surface sweep strategy and polished images of three faces. (a) Surface sweep strategy; (b) polished front face image; (c) polished top face image; (d) polished side face image
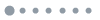
Fig. 11. 3D topography. (a) Initial face; (b) polished front face; (c) polished top face; (d) polished side face
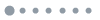
Fig. 12. Metallography and three-dimensional topography of bright and dark zones. (a) Metallographic image of bright zone; (b) three-dimensional topography of bright zone; (c) metallographic image of dark zone; (d) three-dimensional topography of dark zone
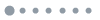
Fig. 13. Forming mechanism of bright and dark regions. (a) Mechanism of jet electrochemical polishing; (b) schematic diagram of light reflection in the dark zone; (c) schematic diagram of light reflection in the bright area
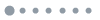
Fig. 14. SEM micrographs of laser directed energy deposited 316L stainless steel and EDS line scan results. (a) Dark zone of the front face; (b) bright zone of the front face; (c) dark zone of the top face; (d) bright zone of the top face; (e) dark zone of the side face; (f) bright zone of the side face; (g)(h) EDS line scan results
|
Table 1. Chemical composition of 316L stainless steel powder
|
Table 2. Laser directed energy deposition parameters
|
Table 3. Polarization curve fitting results of three faces of 316L stainless steel formed by laser directed energy deposition and the substrate
|
Table 4. EIS fitting results of three faces of 316L stainless steel formed by laser directed energy deposition and the substrate
|
Table 5. EDS point scan results of each point in Fig. 14

Set citation alerts for the article
Please enter your email address