
- Chinese Optics Letters
- Vol. 21, Issue 4, 041201 (2023)
Abstract
1. Introduction
As a low-cost, fast full-field measurement technique with high dynamic range[1], phase measuring deflectometry (PMD) is extensively used for wavefront measurement of transparent phase objects[2–8]. PMD has nanometer sensitivity at high spatial frequency; only a computer, a camera, and a screen are required when measuring. Currently, for transparent wavefront measurement, this technique is primarily used with three methods. Canabal and Alonso[5] proposed a method for testing a single thin lens by analyzing the difference between the deflection images and standard images. Petz and Tutsch[6] reported the movement of the screen twice in the axial direction to calculate the propagation direction of transmitted light rays. The third method was obtained by Dominguez et al.[7], i.e., a wavefront and aberration measurement work for three different thin lenses based on a software configurable optical test system[9–11]. In her measurement, additional measuring devices such as a laser tracker were used.
All the tested objects in these previous studies were single thin lenses, but multilens optical systems such as single-lens reflex (SLR) camera lenses, telescopes, or collimators were not applicable. A complex multilens optical system usually has a larger total length and multiple undetectable sublenses. The propagation direction of internal light rays cannot be calculated in the multilens optical system.
In this study, a wavefront measuring method for multilens optical systems based on PMD is presented. This method is demonstrated by the wavefront reconstruction of three different multilens optical systems, and the results are consistent with the interferometry results.
Sign up for Chinese Optics Letters TOC. Get the latest issue of Chinese Optics Letters delivered right to you!Sign up now
All results in this study are presented with the deviation between the real and ideal wavefronts.
2. Principle
The optical path of our method is shown in Fig. 1(a), comprising a screen, a camera, and the test multilens optical system (shown as an SLR camera lens). Computer-generated fringe patterns are sequentially displayed on the screen. The camera captures the deflection images of the displayed fringe patterns via the test multilens optical system. Light is assumed to be emitted from the camera plane. The camera is modeled by the usual pinhole.
Figure 1.Schematic of our method. (a) Layout of the setup; (b) the part from PP1 to PP2 is squeezed into a new paraxial plane, CPP, which plays the role of the camera lens in (b).
We use two paraxial planes to represent the camera lens and the test multilens optical system; they are noted as the camera lens paraxial plane (CLPP) and the test system paraxial plane (TSPP) in Fig. 1(a), respectively. We can consider all the refractions in the test multilens optical system as occurring on TSPP. The focal lengths of the CLPP and TSPP are
Furthermore, we use a new combined paraxial plane (CPP), to represent the combination of the TSPP and CLPP, as shown in Fig. 1(b). We can treat refractions on all the transparent phase elements as caused on the CPP.
In Fig. 1,
If the measurement setup is ideally aligned like interferometry, the gradients vector,
However, in the actual measurement setup, equipment usually cannot align ideally. Misalignments will bring systematic errors to the wavefront. The calculated wavefront
2.1. Calibration strategy of
From the perspective of Fig. 1(b), the focal length
Figure 2.Schematic of calibration strategy in our method.
Then, the wrapped phases in the
Finally, multiple groups of 2D world coordinates are obtained. The focal length
When calibrating, the screen must be put behind
2.2. Solution of
As to phase measuring deflectometry[17–19], the phase
The phase
2.3. Solution of
When
When
2.4. Solution of
When the measurement setup is ideally aligned,
2.5. Removal of systematic errors
To remove the systematic errors
In the end, we can now summarize our method. Rotationally asymmetric wavefront
3. Simulation
In this section, we simulate the wavefront reconstruction process. The simulated wavefront of the multilens optical system was expressed as 0.1 × amount of peaks (300) (unit: mm), as shown in Fig. 3(a).
Figure 3.Simulation of wavefront reconstruction. (a) Simulated wavefront of the multilens optical system; (b) schematic of the simulated measurement setup. (c)–(g) Results when the screen was expressed as (c) z = 0.1x + 0.2y + 1000, (d) z = 0.1x + 0.2y + 2000, (e) z = 0.1x + 0.2y + 8000, (f) z = 0.3x + 0.3y + 2000, and (g) z = 0.4x + 0.4y + 2000; (h) errors between (a) and (e).
Figure 3(b) is the schematic of the simulated measurement setup. The focal lengths of the CLPP and TSPP were 20 and 60 mm. The distance
From this simulation, we can draw these conclusions.
4. Experiment
Experiments were conducted to test the performance of our method. A measuring system was developed, including a CCD camera (IDS UI-2340SE-M-GL) and an LCD screen (ASUS MB169B+) with the diagonal length 396.24 mm and the resolution of
To calculate the unwrapped phase, the three-frequency temporal phase unwrapping[26,27] method was used. The screen displayed sequentially three groups of phase-shifting fringe patterns with different frequencies (
All the test multilens optical systems will be measured at five equally spaced angular positions rotating around the optical axis. These are the positions with the angle of 0°, 72°, 144°, 216°, and 288°, respectively.
4.1. Collimator
A commercial collimator was first selected as the test multilens optical system, where the focal length is 550 mm. Figure 4 shows the whole measurement process.
Figure 4.Measurement process. (a) Measurement setup and the test collimator; (b) pictures acquired when using the temporal phase unwrapping.
Figure 5 shows the test results. Because the rotation accuracy was limited, we removed the first eight Zernike terms. Figures 5(a)–5(e) are the wavefronts at the angular positions with the angle of 0°, 72°, 144°, 216°, and 288°. Figure 5(e) is the interferometry result at 288°.
Figure 5.Test results (the first eight Zernike terms removed). (a)–(e) Wavefronts at the positions with the angles of 0°, 72°, 144°, 216°, and 288°; (f) interferometry result at 288°.
In Figs. 5(a)–5(e), the wavefront maps at the angular positions with different rotation angles are consistent and rotate equally around the optical axis with 72° intervals. In terms of distribution and amplitude (RMS), the results using our proposed method are consistent with the interferometry result.
Moreover, the key aspect of the calibration in Section 2.1, i.e., placing the screen behind
Figure 6.Devices and simplified imaging models of the double calibration when the screen was put (a), (c) behind and (b), (d) in front of c′.
4.2. SLR prime lens
Another commercial optical system was selected to be the second test object: an F/1.8 Nikon Nikkor SLR prime lens, comprising six sublenses, with a focal length of 50 mm and total length of 39 mm. The whole measurement process is shown in Fig. 7.
Figure 7.Measurement process. (a) Measurement setup and the test SLR prime lens; (b) pictures acquired when using the temporal phase unwrapping.
Figure 8 shows the results of our method and interferometric test. Also, due to the limited rotation accuracy, the first eight Zernike terms were removed. The test results show an obvious secondary coma remains in the wavefronts. Wavefront maps at the angular positions with different rotation angles are still consistent, and rotate equally around the optical axis with 72° intervals. Results prove that the measurement accuracy is comparable with interferometric test. Certain blurred spots in Fig. 8 were attributed to the dust on the lens surface.
Figure 8.Test results (the first eight Zernike terms removed). (a)–(e) Wavefronts at the positions with the angles of 0°, 72°, 144°, 216°, and 288°; (f) interferometry result at 288°.
4.3. SLR zoom lens
In the last experiment, we selected an SLR zoom lens as the test multilens optical system: Nikon Nikkor SLR zoom lens, 18–55 mm focal length, comprising 12 sublenses, as shown in Fig. 9. The blue parts in Fig. 9 show the aspherical lens elements. The focal length of this test SLR zoom lens was sequentially set to 18 mm and 55 mm. Two measurements under different focal lengths were conducted to confirm this method. Figure 10 shows the results (the first eight Zernike terms removed).
Figure 9.Diagram of the internal sublenses in the test SLR zoom lens.
Figure 10.Test results (the first eight Zernike terms removed). (a)–(e) Wavefronts at the angular positions with five rotation angles (0°, 72°, 144°, 216°, and 288°) under 18 mm focal length; (f)–(j) wavefronts at the angular positions with five rotation angles (0°, 72°, 144°, 216°, and 288°) under 55 mm focal length.
In Fig. 10, wavefronts at different angular positions under 18 or 55 mm focal length were consistent, and rotated equally around the optical axis with 72° intervals. For the wavefronts with the same angular positions, the maps under 18 and 55 mm focal lengths were still consistent. The results in Fig. 10 confirm the feasibility of this method.
5. Summary
In this study, a wavefront measuring method for an optical system with multiple optics is presented based on PMD. The test multilens optical system and the camera lens are considered as two paraxial planes. Next, a new paraxial plane is used to represent these two separate paraxial planes. We introduced our calibration strategy and mathematical equations to calculate the distance parameters in the measurement setup. The simulations and experiments of three different types of multilens optical systems were performed, which confirm the proposed measuring method. Systematic errors are suppressed using the
In the past, PMD was primarily used to test a mirror or a single thin lens. The proposed method makes it possible for PMD to test a multilens optical system where the total length can reach 550 mm, similar to a collimator.
References
[1] L. Huang, M. Idir, C. Zuo, A. Asundi. Review of phase measuring deflectometry. Opt. Lasers Eng., 107, 247(2018).
[2] Z. Chen, W. Zhao, Q. Zhang. Wavefront measurement of membrane diffractive lens using line structured light deflectometry. Proc. SPIE, 11617, 116172W(2020).
[3] M. Z. Dominguez, J. Armstrong, P. Su, R. E. Parks, J. H. Burge. SCOTS: a useful tool for specifying and testing optics in slope space. Proc. SPIE, 8493, 84931D(2012).
[4] Y. Liu, X. Su, Q. Zhang. Wavefront measurement based on active deflectometry. Proc. SPIE, 6723, 67232N(2008).
[5] H. A. Canabal, J. Alonso. Automatic wavefront measurement technique using a computer display and a charge-coupled device camera. Opt. Eng., 41, 822(2002).
[6] M. Petz, R. Tutsch. Measurement of optically effective surfaces by imaging of gratings. Proc. SPIE, 5144, 288(2003).
[7] M. Z. Dominguez, L. Wang, P. Su, R. E. Parks, J. H. Burge. Software configurable optical test system for refractive optics. Proc. SPIE, 8011, 80116Q(2011).
[8] L. Jiang, X. Zhang, F. Fang, X. Liu, L. Zhu. Wavefront aberration metrology based on transmitted fringe deflectometry. Appl. Opt., 56, 7396(2017).
[9] P. Su, M. Khreishi, T. Su, R. Huang, M. Z. Dominquez, A. V. Maldonado, G. P. Butel, Y. Wang, R. E. Parks, J. H. Burge. Aspheric and freeform surfaces metrology with software configurable optical test system: a computerized reverse Hartmann test. Opt. Eng., 53, 031305(2014).
[10] R. Huang, P. Su, J. H. Burge, L. Huang, M. Idir. High-accuracy aspheric x-ray mirror metrology using software configurable optical test system deflectometry. Opt. Eng., 54, 084103(2015).
[11] P. Su, S. Wang, M. Khreishi, Y. Wang, T. Su, P. Zhou, R. E. Parks, K. Law, M. Rascon, T. Zobrist, H. Martin, J. H. Burge. SCOTS: a reverse Hartmann test with high dynamic range for giant Magellan telescope primary mirror segments. Proc. SPIE, 8450, 84500W(2012).
[12] L. Huang, A. Asundi. Improvement of least-squares integration method with iterative compensations in fringe reflectometry. Appl. Opt., 51, 7459(2012).
[13] H. Guang, Y. Wang, L. Zhang, L. Li, M. Li, L. Ji. Enhancing wavefront estimation accuracy by using higher-order iterative compensations in the Southwell configuration. Appl. Opt., 56, 2060(2017).
[14] Y. Surrel. Design of algorithms for phase measurements by the use of phase stepping. Appl. Opt., 35, 51(1996).
[15] C. Zuo, S. Feng, L. Huang, T. Tao, W. Yin, Q. Chen. Phase shifting algorithms for fringe projection profilometry: a review. Opt. Lasers Eng., 109, 23(2018).
[16] Z. Zhang. A flexible new technique for camera calibration. IEEE Trans. Pattern Anal., 22, 1330(2000).
[17] M. C. Knauer, J. Kaminski, G. Hausler. Phase measuring deflectometry: a new approach to measure specular free-form surfaces. Proc. SPIE, 5457, 366(2004).
[18] J. H. Massig. Measurement of phase objects by simple means. Appl. Opt., 38, 4103(1999).
[19] C. Faber, E. Olesch, R. Krobot, G. Husler. Deflectometry challenges interferometry: the competition gets tougher!. Proc. SPIE, 8493, 84930R(2012).
[20] D. C. Ghiglia, M. D. Pritt. Two-Dimensional Phase Unwrapping: Theory, Algorithms, and Software(1998).
[21] J. Tian, X. Peng, X. Zhao. A generalized temporal phase unwrapping algorithm for three-dimensional profilometry. Opt. Lasers Eng., 46, 336(2008).
[22] P. Banerjee, T. C. Poon. Principles of Applied Optics(2015).
[23] W. Song, F. Wu, X. Hou. Method to test rotationally asymmetric surface deviation with high accuracy. Appl. Opt., 51, 5567(2012).
[24] C. J. Evans, R. N. Kestner. Test optics error removal. Appl. Opt., 35, 1015(1996).
[25] W. H. Southwell. Wave-front estimation from wave-front slope measurements. J. Opt. Soc. Am., 70, 998(1980).
[26] H. O. Saldner, J. M. Huntley. Temporal phase unwrapping: application to surface profiling of discontinuous objects. Appl. Opt., 36, 2770(1997).
[27] C. Zuo, L. Huang, M. Zhang, Q. Chen, A. Asundi. Temporal phase unwrapping algorithms for fringe projection profilometry: a comparative review. Opt. Lasers Eng., 85, 84(2016).
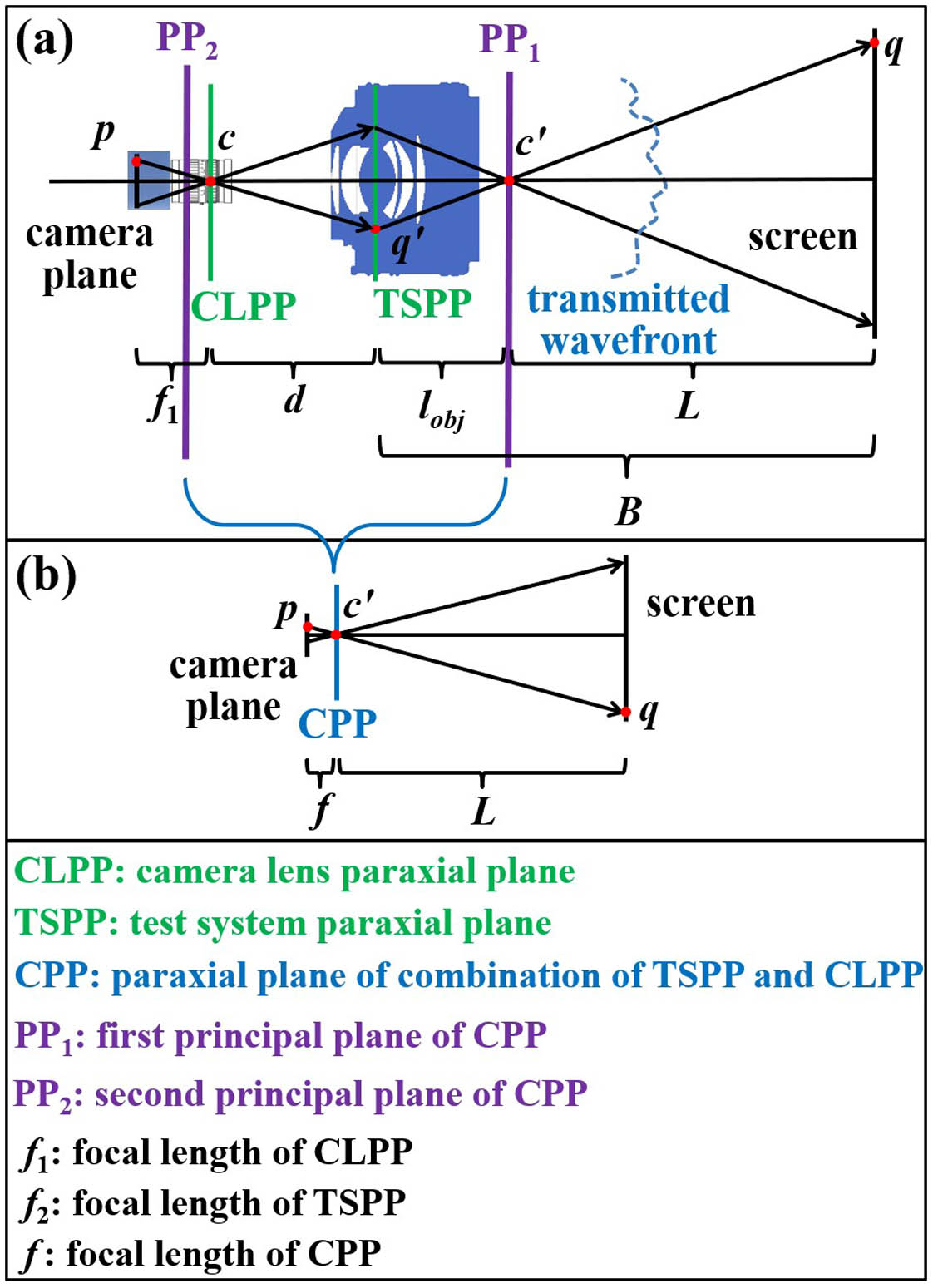
Set citation alerts for the article
Please enter your email address