QIN Na, ZHENG Liang, LIU Ya-long, KONG Chun-lei. Subsurface damage detection of RB-SiC and its subsurface damage characteristics in rotating ultrasonic grinding[J]. Optics and Precision Engineering, 2017, 25(10): 2714

Search by keywords or author
- Optics and Precision Engineering
- Vol. 25, Issue 10, 2714 (2017)
Abstract
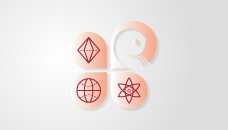
Set citation alerts for the article
Please enter your email address