Yunqiao Zhang, Bohan Li, Guosheng Duan, Yingwei Zhang. Effect of Processing Parameters on Densification and Mechanical Properties of Additively Manufactured Inconel 738 Alloy[J]. Chinese Journal of Lasers, 2025, 52(12): 1202309

Search by keywords or author
- Chinese Journal of Lasers
- Vol. 52, Issue 12, 1202309 (2025)

Fig. 1. Powder morphology (left) and particle size distribution (right)

Fig. 2. Samples. (a) During the forming process of the test blocks; (b) after the test block is taken out and the powder is cleared; (c) the size of tensile samples
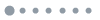
Fig. 3. Microstructures of Inconel 738 printed samples under SEM. (a) XY-plane; (b) Z-plane
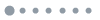
Fig. 4. Characterization of porosity defects in Inconel 738 printed samples. (a) OM image; (b) SEM image
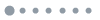
Fig. 5. Characterization of crack defects in Inconel 738 printed samples. (a) E=65 J/mm3; (b) E=67.5 J/mm3; (c) E=70 J/mm3;
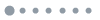
Fig. 6. Characterization of unfused defects in Inconel 738 printed samples. (a) E=61.36 J/mm3; (b) E=58.44 J/mm3;
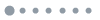
Fig. 7. Laser energy density versus densification
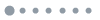
Fig. 8. Relationship between scanning speed and densification under different conditions. (a) Under the conditions of laser power of 280 W and pitch of 0.10 mm; (b) under the conditions of laser power of 260‒300 W and pitch of 0.10 mm
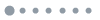
Fig. 9. Relationship between laser power and densification under different conditions. (a) Under the conditions of scanning speed of 1050 mm/s and pitch of 0.10 mm; (b) under the conditions of scanning speed of 950‒1150 mm/s and pitch of 0.10 mm
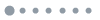
Fig. 10. Tensile properties of formed samples at different laser energy densities. (a) Engineering stress-engineering strain curves;
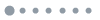
Fig. 11. SEM images of tensile samples. (a) Group 1; (b) Group 2; (c) Group 3; (d) Group 4; (e) Group 5
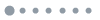
Fig. 12. Fracture morphology of tensile samples. (a) Group 1; (b) Group 2; (c) Group 3; (d) Group 4; (e) Group 5
|
Table 1. Chemical composition of Inconel 738 high-temperature alloy powders
|
Table 2. Forming parameters of Inconel 738 high-temperature alloy blocks

Set citation alerts for the article
Please enter your email address