LIU Hong-xi, CAI Chuan-xiong, JIANG Ye-hua, ZHANG Xiao-wei, WANG Chuan-qi. Influence of alternative magnetic field on macro morphology and microstructure of laser cladding Fe-based composite coating[J]. Optics and Precision Engineering, 2012, 20(11): 2402

Search by keywords or author
- Optics and Precision Engineering
- Vol. 20, Issue 11, 2402 (2012)
Abstract
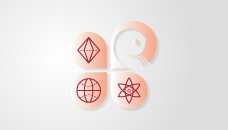
Set citation alerts for the article
Please enter your email address