Mingxiao Shi, Yan Xiao, Heyu Sun, Weihua Wang, Jiugong Chen, Xiaojie Yang. Fluid Flow Behavior in the Molten Pool of 5083 Aluminum Alloy During Oscillating Laser Wire‑Filling Welding[J]. Chinese Journal of Lasers, 2025, 52(12): 1202106

Search by keywords or author
- Chinese Journal of Lasers
- Vol. 52, Issue 12, 1202106 (2025)

Fig. 1. Schematic diagram of oscillatory laser welding system

Fig. 2. Relationship between thermophysical property parameters of 5083 aluminum alloy and temperature. (a) Specific heat capacity; (b) density; (c) thermal conductivity
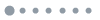
Fig. 3. Schematic of meshing of computational domain
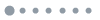
Fig. 4. Comparison of the simulated molten pool cross-sectional morphology and the actual weld cross-sectional morphology obtained under the action of an oscillating laser beam (f=100 Hz)
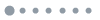
Fig. 5. Temperature distributions of the free surfaces of molten pools at four equally spaced moments in one oscillation cycle.
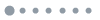
Fig. 6. Temperature distributions of free surfaces of molten pools at t=100 ms. (a) Conventional laser welding; (b) oscillating laser welding (f=100 Hz); (c) temperature gradient distribution curves of the molten pools extracted along the red lines
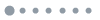
Fig. 7. A comparison of the cross-sectional morphology of molten pools at t=100 ms. (a) Conventional laser welding; (b) oscillating laser welding (f=100 Hz)
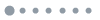
Fig. 8. Fluid flow patterns at the molten pool surfaces at four equally spaced moments during an oscillating period. (a)‒(d) Conventional laser welding; (e)‒(h) oscillating laser welding (f=100 Hz)
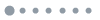
Fig. 9. Fluid flow patterns at the longitudinal section through the center of the keyhole of the molten pool at four equally spaced moments during an oscillating period. (a)‒(d) Conventional laser welding; (e)‒(h) oscillating laser welding (f=100 Hz)
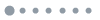
Fig. 10. Weld X-ray flaw detection images
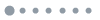
Fig. 11. Porosity of the weld obtained at different oscillation frequencies
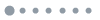
Fig. 12. Microstructures of different areas in the welds
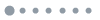
Fig. 13. Microstructures of the welds obtained at different oscillation frequencies
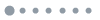
Fig. 14. XRD analysis of the oscillating laser welded joint at f=100 Hz
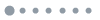
Fig. 15. Precipitation phase contents in the welds obtained at different oscillation frequencies
|
Table 1. Chemical composition of base metal and welding wire
|
Table 2. Some thermophysical property parameters of 5083 aluminum alloy

Set citation alerts for the article
Please enter your email address