
- High Power Laser and Particle Beams
- Vol. 36, Issue 1, 013014 (2024)
Abstract
Keywords
Microwave heating is widely used in food health care, wood processing, ceramic sintering[1] and other fields. It makes polar molecules in the heated medium interact rapidly in a short time through electromagnetic field to generate a large amount of heat, thus it has the advantages of fast heating rate, green environmental protection, etc. However, it also has the uneven temperature heating and local overheating caused by the simultaneous existence of hot spots and cold spots[2]. Due to the huge power required by industrial microwave heating equipment, one microwave source can not meet the requirements, hence there are usually multiple microwave sources working together.
Chan T et al[3] analyzed that the symmetrical distribution of feed ports can improve the coupling degree of feed ports by microwave heating model of four feed ports. Kusturee Jeni et al[4] and Wang Shunmin et al[5] proposed that the microwave heating equipment with multiple feed ports could make the internal temperature of microwave oven more uniform. Zhou Mingchang[6] used COMSOL to simulate a cylindrical microwave resonator with ten feed ports. The results show that the increase of the number of feed ports can greatly improve the uniformity of dielectric heating. However, nonuniformity of microwave heating still exists. Dai Chengjun[7] analyzed the heat energy change in the microwave heating device, and obtained the unsteady differential equation and the first-order inertial transfer function with delay by Laplace transform simulation, which simulated the real-time process of coal microwave heating. Yang Biao et al[8] proposed a numerical calculation model for microwave heating of moving materials by distribution relationship between voltage and current on the transmission line, which could effectively suppress the sudden change of microwave heating temperature. Based on the microwave heating mechanism model, Zhong Jiaqi et al[9] verified the effectiveness of its temperature tracking control strategy by microwave heating short waveguide model.
Because of the non-uniformity of microwave heating and the unknown loss of actual circuit, this paper chooses water with good quality and low price as the heated medium. First, the power of magnetron is roughly determined by differential static modeling, which is used for COMSOL simulation and calculation of heat source in MATLAB simulation. Microwave non-uniform heating, that is, the distribution of heat source, can be reasonably assumed according to the electric field distribution in water medium in COMSOL simulation. Moreover, the temperature distribution simulated by MATLAB is roughly consistent with that simulated by COMSOL, which verifies the effectiveness of the model. Assuming that the temperature in the heated medium can be obtained by MATLAB simulation, the temperature in the edge of the water medium decreases, and the temperature in the center part is about T, so the temperature T can be regarded as its steady state. That is, after stopping heating, the temperature in all parts of the water medium tends to be neutral, and the microwaves that have not yet reacted with water also react with water at this time, and the temperature at all points in the water reaches the same after a period of time. According to the COMSOL simulation of uneven microwave heating point temperature, some representative points near the temperature T are found, and the actual temperature changes of these points in the heating process are compared to find out the best point as the control object. After that, the point that can best reflect the temperature change trend in the microwave heating device and any other points in the medium are controlled by expert PID, which verifies the advantages of taking the temperature rise equilibrium point as the research object for microwave controlled heating.
1 Establishment of static difference model
1.1 Composition of microwave resonator
The microwave heating system consists of an electromagnetic wave generator and a metal microwave resonant cavity which can reflect microwave to the surface of the heated object. Microwave resonator is a space geometry composed of a cylinder with a height of 0.8 m and a bottom diameter of 0.8 m; The contact area between the internal stainless steel bracket and the inner wall of the microwave oven is
Figure 1.Microwave resonator diagram
1.2 Combined heat transfer in microwave oven
In actual industrial production, the way of heat transfer does not exist alone, but has a combination of various ways of heat transfer. The compound heat transfer process of microwave oven is divided into three parts:
(1) The outer wall of the ceramic cup transfers heat to the inner surface of microwave oven through natural convection and heat radiation in limited space.
(2) The inner surface of microwave oven diffuses heat to the outer surface of microwave oven by heat conduction.
(3) Heat diffuses into the air by heat convection on the outer surface of microwave oven.
One-dimensional schematic diagram of heat loss of microwave oven equipment during operation is shown in Fig.2.
Figure 2.Schematic diagram of heat loss
According to the Fourier Law, the Newton’s cooling formula[10] and Stefan-Boltzmann Law, the heat loss
In Eq. (1),
The difference model of medium temperature at any time when microwave oven works is:
Where
Because the purity of stainless steel on the outer wall of microwave oven is unknown in the actual equipment environment, the actual heat transfer coefficient K and magnetron power
Randomly take 5.4 kg of water medium for the Bang-Bang control heating at a set temperature of 70 ℃. The practical results obtained by the Bang-Bang control heating, the theoretical results obtained by MATLAB based on the difference model (Eq. (2)) of medium temperature, are all shown in Fig.3. Fig.3 shows that the static difference model is consistent with the actual heating and cooling process, and the actual input power
Figure 3.Temperature error analysis chart of 5.4 kg water
In Eq. (4),
2 Establishment and verification of dynamic difference model
2.1 Finite difference modeling
To observe the temperature at any time and at any position in the microwave oven and understand the heating situation, the finite difference method is used to simplify the model (the thermal convection and radiation of the air in the device are ignored). Because the experimental device is a cylinder, it matches the three dimensions of the device and has an internal heat source. Taking the element control body(
In Eq. (5),
Because of the circular symmetry, the 3D problem is simplified to a 2D problem:
Taking the half section of a cylinder as the research object, different materials are partitioned, and the 2D schematic diagram is shown in Fig.4.
Figure 4.Partition diagram of different materials
In Fig.4, W, G, A and B respectively represent different medium of water, ceramic, air and stainless steel, and the material parameter (density, specific heat capacity and thermal conductivity) values of each layer are shown in Table 1; their subscripts represent different areas meshed by use of finite difference method. The boundaries in the direction r are
material | |||
W | 1000 | 4200 | 0.59 |
G | 2600 | 850 | 2 |
A | 1.18 | 1005 | 0.028 |
B | 7930 | 1260 | 16.2 |
Table 1. Material parameter values of each layer
The outside air temperature is
① There is an internal heat source in the water medium (that is, the water medium absorbs microwave), so the differential heat conduction equation in
Make
Where j is the number of grid nodes in the r direction; k is the number of grid nodes in the z direction; n is the number of time nodes;
② The left boundary in the r direction of the area is adiabatic, and the right boundary is ceramic. Make
Differentiation and simplification are carried out to obtain:
In the z direction of water region, a difference equation is established to solve it.
According to steps ① and ②, difference equations are established and simplified according to different points in each region. The heat transfer between the stainless steel wall and the outside air is heat convection, and the boundary differential equation is slightly different. The rightmost boundary is:
Make
2.2 Stability conditions
The stability limits of internal node discrete equation and boundary node discrete equation are as follows[11]:
Because the ceramic cup wall and stainless steel wall are only about 5mm, 2.5mm is the most suitable for
2.3 Comparison of MATLAB and COMSOL simulation
Set the mass of water to 5 kg, since the ceramic cup is a cylindrical container with a radius of 0.08 m and a height of 0.33 m. the height of the water medium is 0.24 m, the volume
In COMSOL, the space geometric model is designed according to the size and material of the actual device, and the 1/2 full-size model (Fig.5) is taken, that is, three feed ports are fed with
Figure 5.1/2 full scale model
Figure 6.Temperature distribution at 465 s
Figure 7.COMSOL simulation of electric field distribution in water medium
In Fig.7, L is the distance from origin O in r and z directions. As can be seen from Fig.7, the electric field in z direction decreases rapidly from the edge of water medium (the two blue points represent the upper edge position and the lower edge position of the water medium respectively) to 40 mm inside, and the middle part tends to be roughly stable. The electric field in r direction is always in a weak state.
To correspond with the coordinates in MATLAB simulation, the coordinates in the following text are expressed in the form of (x/mm, y/mm, z/mm). In MATLAB, the internal heat source distribution is adjusted according to the electric field intensity, and the simulation time is 465 s and the heating step is 0.1 s. Taking the three-bit section between the point (0, 0, 520) and the point (0, 395, 520) in the r direction, and taking the three-bit section between the point (0, 65, 0) and the point (0, 65, 795) in the z direction (based on Fig.5), when simulating 465 s, the temperature pairs of each 3D section point are shown in Fig.8.
Figure 8.Temperature comparison in
The main reason the water medium simulation exceeds 100 ℃ in Fig.8 is highlighting the inhomogeneity of microwave heating, thus the temperature is not limited in simulation. Due to the complexity of the electromagnetic field distribution inside the microwave resonant cavity, MATLAB simulation cannot truly simulate irregular electromagnetic fields. Therefore, the simulation results of MATLAB and COMSOL are relatively similar in the r direction and slightly different in the z direction, but the overall trends are similar, which verifies the correctness of the finite difference model.
After stopping heating, because the water medium is liquid, the uneven temperatures will eventually neutralize each other, so that the temperature of the water medium will eventually tends to T. It can be assumed that the heat source is uniformly distributed in the water medium in MATLAB simulation, and the MATLAB temperature distribution is shown in Fig.9(a). The temperature distribution of MATLAB when the heat source is unevenly distributed is introduced in Fig.9(b).
Figure 9.Temperature distribution of microwave uniform heating and uneven heating in
As can be seen from Figure 9, assuming uniform microwave heating, the temperature distribution of water medium is uniformly T, and the temperature at the boundary is slightly lower than that at the central part. At this point, the coordinates of the three-dimensional cutoff points similar to temperature T can be found in the simulation results of uneven heating in MATLAB and COMSOL, such as A (20, 0, 475) and B (20, 0, 455). These 3D intersections are called the equilibrium points of temperature rise in the heating process of water medium, which can reflect the temperature change trend of the whole water medium in the microwave heating process to the greatest extent.
3 Experimental verification
To better demonstrate the particularity of temperature rise balance point in control, a microwave heating experimental device was set up for experimental verification. In the experimental equipment, three-phase AC power supply provides input voltage for the normal operation of high voltage transformer (GAL-800E-4). The output end of the high-voltage transformer outputs about 4 V and 2000 V AC voltages, in which 4 V AC supplies power to the filament of the magnetron. The output end of 2000 V AC and 1
Figure 10.Block diagram of microwave heating control system
3.1 Characteristic embodiment of temperature rise equilibrium point
In a real microwave heating experiment, the peripheral point C (40, 0, 520), the central point D (0, 0,420) and the temperature rise equilibrium points A and B in the water medium were selected as the research objects, and K-type thermocouples of the same model were placed near these four points. When 5 kg tap water was heated to the set temperature of 70 ℃, the magnetron was disconnected and the temperature change trend at different points during this process was observed, as shown in Fig.11.
Figure 11.Temperature change trend at each point
As can be seen from Fig.11, the temperature of water medium varies from place to place due to the inhomogeneity of microwave heating. After the heating process of about 465 s, the water medium absorbs the residual microwave, and the neutralization of water temperature is dominant. At about 675 s, the overall temperature in all parts of the water medium is about 83.5 ℃, and then the heat dissipation occupies a dominant position. Point C is located in the periphery of water medium, absorbing more microwave energy and heating up quickly. Point D, which is in the center of water medium, absorbs less microwave, and mainly depends on the neutralization reaction of water to heat up after stopping heating. There is still a small amount of overshoot when heating is stopped at point A, which is roughly stable at about 83.5 ℃ compared with when heating is stopped at Point B. The temperature rise equilibrium point B is selected as the control object in the follow-up experiment, which can best reflect the overall uniform temperature of the heated liquid medium at each time.
3.2 Control advantages of temperature rise equilibrium point
In three microwave heating experiments, temperature rise equilibrium point B, peripheral point C and central point D are taken as control objects, and incremental expert PID is used to control them. The control rules are shown in Table 2, in which u represents the control quantity output by the controller, and the temperature change trend of each point is shown in Fig.12.
No. | if | then |
1 | u>1.00 | all five magnetrons run |
2 | 1.00≥u>0.75 | four magnetrons run randomly |
3 | 0.75≥u>0.50 | three magnetrons run randomly |
4 | 0.50≥u>0.25 | two magnetrons run randomly |
5 | 0.25≥u>0.00 | one magnetron run randomly |
6 | u≤0.00 | all magnetrons stop running |
Table 2. Empirical rule table of incremental expert PID control
Figure 12.Temperature change trend of each point under expert PID control
It can be seen from Fig.12 that the overshoot at peripheral point C is about 1.4 ℃, and the time to reach the set temperature is about 260 s. The B-ultrasound adjustment of temperature rise equilibrium point is about 1.9 ℃, and the time to reach the set temperature is about 400 s. The D overshoot at the center point is about 3.7 ℃, and the time to reach the set temperature is about 500 s. According to the analysis of microwave input power and water medium quality, when the temperature at point C reaches the designated temperature of 70 ℃, temperatures at other locations within the water medium have not yet attained the preset temperature. Likewise, when the temperature at point D reaches the designated temperature, the peripheral regions of the water medium have already exceeded the preset temperature. Consequently, the desired control outcome cannot be achieved in either case. However, when the temperature at the equilibrium point of temperature rise, denoted as point B, reaches the preset temperature, the phenomenon of liquid diffusion ensures that temperatures at other points within the water medium closely approximate the set temperature of 70 ℃. Therefore, designating the temperature rise equilibrium point B as the heating target offers the most effective means of reflecting the overall temperature trend of the heated liquid medium. Furthermore, when the controller engages in its control operation, the magnetron switching frequency is moderate, contributing to an extended operational lifespan of the magnetron, compared to frequent switching.
4 Conclusion
Due to the inherent non-uniformity of microwave heating, the approach of haphazardly positioning temperature sensors for the measurement of the heated medium's temperature is deemed imprudent. Hence, this paper introduces a dynamic finite difference model as a methodology to identify temperature rise equilibrium points. Multiple such points are identified and subsequently tested to discern the most optimal equilibrium point for microwave heating control. The principal research focus of this paper can be segmented into three primary components:
(1) According to the physical structure of the microwave heating device, the static differential modeling is carried out to obtain the actual power of the magnetron in full operation, which provides data support for the later simulation.
(2) The temperature distribution of multi-media in 3D space is modeled, and the distribution of microwave heat source is obtained by simulating the distribution of electric field in water medium in COMSOL. The accuracy of the 3D finite difference model is verified by comparing MATLAB with COMSOL simulation of microwave heating. After that, assuming that the uniform temperature of water medium is obtained by 3D finite difference model when microwave heating is uniform (microwave heat source is uniformly distributed), the 3D cross-section points close to the temperature in COMSOL simulation model are found out, and these temperature equilibrium points can reflect the whole temperature change trend of medium in microwave heating device to the greatest extent.
(3) Subsequently, through a series of straightforward microwave heating experiments, the equilibrium point of temperature rise exhibiting the most favorable performance characteristics is selected for microwave heating control. In conclusion, this selected point, when employed as the control object, is subjected to intelligent control alongside other control objects to validate its superiority in the context of microwave heating control.
The experimental results show that the microwave heating control method based on the dynamic finite difference method can transform the non-uniformity problem of microwave heating into the problem of finding the best place to replace the uniform heating point of the whole medium, and then it can be solved visually by MATLAB and COMSOL. This method has a good application prospect for the medium with good thermal conductivity (especially liquid medium) in the actual industrial production of microwave heating.
References
[3] Chan T V C T, Reader H C. Computational design of a multiplex magron cavity[C]Proceedings of IEEE AFRICON’96. 1996: 523527.
[6] Zhou Mingchang. Study on numerical simulation of microwave heating temperature control[D]. Mianyang: Southwest University of Science Technology, 2020.
[7] Dai Chengjun. The design development of the microwave activation equipment on the industry[D]. Mianyang: Southwest University of Science Technology, 2012.
[8] Yang Biao, Wang Shili, Guo Linjia, et al. Numerical calculation of temperature uniformity in microwave heating based on moving mesh[J]. Control and Decision, 34, 113-120(2019).
[9] Zhong Jiaqi, Liang Shan, Xiong Qingyu.
[10] Zheng Hongfei. Fundamentals of thermodynamics heat transfer[M]. Beijing: Science Press, 2016.
[11] Liu Yanfeng, Liang Xiujun, Gao Zhengyang, et al. Heat transfer[M]. Beijing: China Electric Power Press, 2021.
[12] Zhou Mingchang, Li Shaofu. Multi-feed microwave heating temperature control system based on numerical simulation[J]. Journal of Microwaves, 35, 92-96(2019).
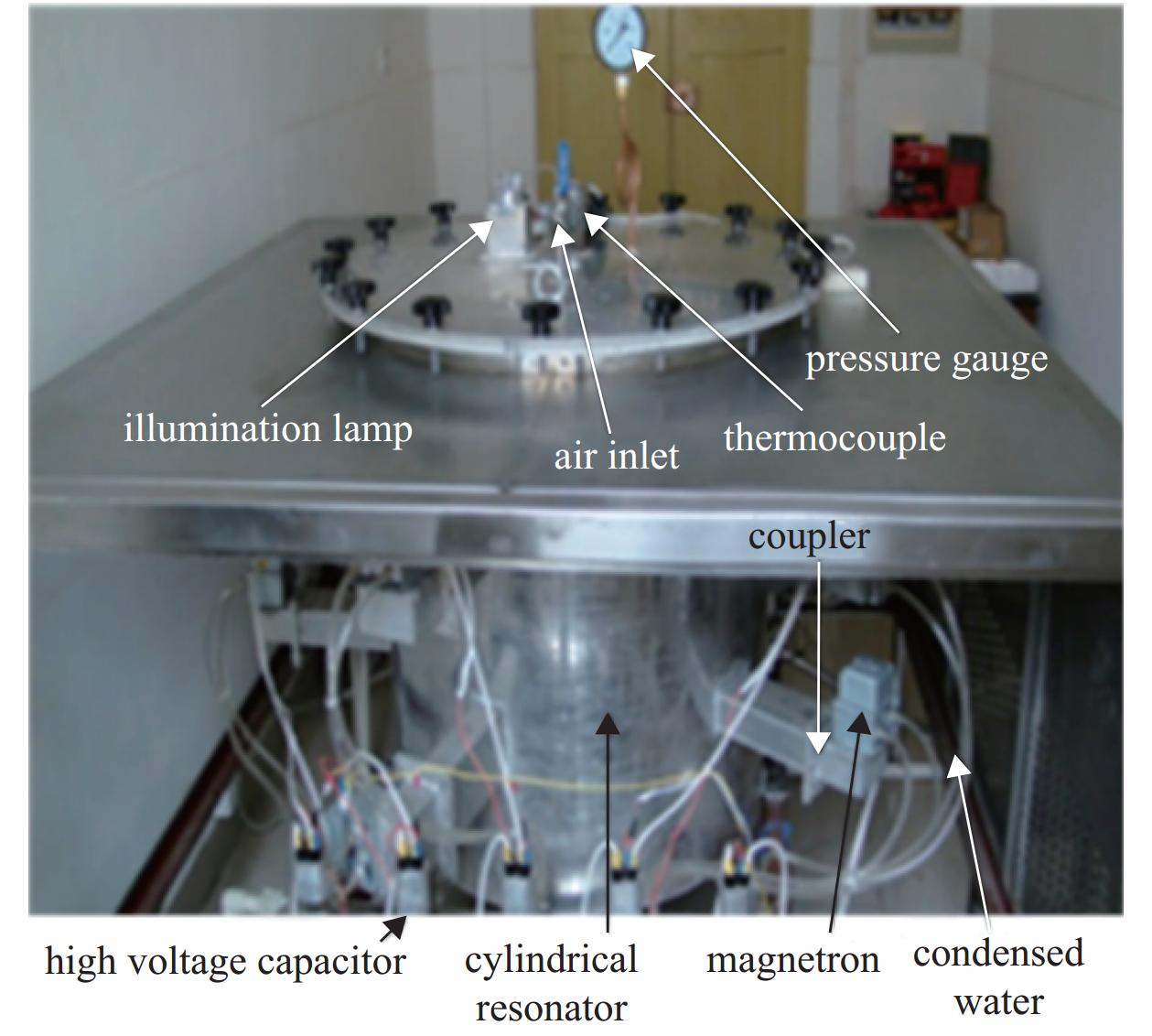
Set citation alerts for the article
Please enter your email address