
- Journal of Resources and Ecology
- Vol. 11, Issue 4, 388 (2020)
Abstract
Keywords
1 Introduction
Shipping carries about 90% of the world’s cargo annually and plays an important role in international trade and the world economy (
To comply with the IMO requirements for SOx and NOx emissions, China’s Ministry of Transport (MOT) issued a document concerning regulations for domestic emission control areas (DECAs) in 2015; this document requires shipowners to adopt new emission reduction technologies.
Currently, two technological options are available for sulphur removal: switching to low-sulphur fuel or installing exhaust gas cleaning systems (EGCS). There are also two technological options available for nitrogen removal: selective catalytic reduction (SCR) uses a catalyst to reduce nitrogen oxides to nitrogen and water, while exhaust gas recirculation (EGR) redirects exhaust gas back into the combustion chamber to lower the engine combustion temperature and control NOx emissions. Beyond these alternatives, the substitution of conventional fuels with LNG and shore power application are highly recommended. In conclusion, this paper estimates the abatement costs of these six reduction measures: low-sulphur fuel, EGCS, SCR, EGR, shore power application, and LNG.
2 Brief comparison of emission reduction alternatives
2.1 Switching to low-sulphur fuel
Compared with after-treatment technologies, switching to low-sulphur fuel is the easiest abatement technique to adopt. There are two aspects to abatement costs for switching to low-sulphur fuel. Firstly, existing boiler and diesel engine systems, involving but not limited to fuel supply systems, combustion devices, and monitoring and display systems, have to be retrofitted to be compatible with low-sulphur fuel, and this might entail expenses for shipowners. Second, abatement costs can also result from price differences between fuels with different sulphur content.
2.2 Installing exhaust gas cleaning systems
Installing a sulphur scrubber in an EGCS can reduce sulphur emissions by 98% (
2.3 Installing selective catalytic reduction system
Installation of a SCR system offers a method for nitrogen oxides abatement that complies with Tier III emission standards. SCRs use urea as a reducing agent to catalytically reduce nitrogen oxides to nitrogen and water. The China Classification Society (CCS) has published the Preset Guide for Selective Catalytic Reduction of Ship Systems to provide technical guidance for SCR system presets. Because they have high removal efficiency of 70% to 90%, create less secondary pollution and rely on mature technology, SCRs are cost effective and increasingly applied to vessels, especially vessels with four-stroke engines and auxiliaries.
2.4 Installing exhaust gas recirculation system
EGR is based on redirecting a part of the exhaust gas back into the combustion chamber to lower the combustion temperature and reduce the nitrogen emissions to meet Tier III emission standards. Because it can be installed in a small space, it is possible to integrate an EGR with a desulfurization device on the ship to reduce nitrogen as well as sulphur dioxide emissions.
2.5 Installing shore power application
China’s Port Coastal Power Layout Plan states that more than 50% of the passenger roll berths, cruise ship berths, containership berths and specialized berths with dry bulk of 50000 tons or more in major ports and ECA should have the capability to supply shore power by the end of 2020. Ports with high demand and good conditions are encouraged to achieve 100% shore power coverage of berths. There will be a total of 493 specialized berths with the capacity to supply shore power in major ports and ECA by the end of 2020, including 366 in coastal areas and 127 along inland rivers.
2.6 Liquefied natural gas ships
As an alternative to conventional fuels, clean-energy LNG can significantly reduce the amount of nitrogen and sulphur pollutants emitted by ships. Substituting LNG for fuel oil as a ship’s power source results in almost no sulphur emissions and a 35% to 85% reduction of nitrogen emissions (
3 Cost estimates of emission reduction alternatives
3.1 Cost of switching to low-sulphur fuel
Coastal and ocean-going vessels normally use heavy fuel oil (HFO) #180 or blended oil. This means shipowners have to retrofit their vessels with special low-sulphur oil tanks and fuels pipelines to switch to a low-sulphur fuel. Documentation for the North American ECA indicates that the use of low-sulphur oil equipment results in a 0.5%-2% cost increment (
Switching costs are generated by calculating the price difference between fuels with 0.5% sulphur content (0.5% S) and 0.1% sulphur content (0.1% S) fuels. This paper calculates switching costs based on the average daily fuel price at Shanghai Port. The average price difference between 0.1% S fuel and 0.5% S fuel is USD 137.20 t-1.
3.2 The cost of exhaust gas cleaning systems
The cost of retrofitting a ship varies depending on the degree of modification required, and generally costs 40% more than a new build (
3.3 The cost of selective catalytic reduction systems
The principal costs of installing an SCR include the costs of the reactor, the monitoring system and the control system, all of which vary in price depending on ship type and size. The operating cost of a system depends on the amount of urea used and the cost of catalyst regeneration. Different agencies quoted different prices, as shown in
Source | Equipment cost | Installation cost | Operating cost | Urea cost |
---|---|---|---|---|
ECA | USD 40-135 kW-1 | - | 7%-10% of the fuel cost | - |
NRDC | USD 50 kW-1 | USD 15-20 kW-1 | USD 0.08 kWh-1 | 10-15 L MWh-1 |
DMA | USD 30-70 kW-1 | USD 6-15 kW-1 | USD 5-12 MWh-1 | - |
Table 1.
The cost of selective catalytic reduction system
In conclusion, our estimates of SCR costs are based on data from a range of agencies as well as from a series of field studies of different manufacturers. Based on the above research and analysis, this study determines the equipment cost for an SCR system is USD 30 kW-1 to USD 80 kW-1, installation fee is 30%-40% of equipment cost, operating costs is 7%-10% of fuel cost.
3.4 The cost of exhaust gas recirculation systems
The European Union produced EGR cost estimates at the 66th meeting of the Marine Environment Protection Committee (MEPC) (
3.5 The cost of installing shore power application
The cost of using shore power includes construction costs for shore power facilities, shipboard equipment retrofitting costs, the berthing time of inbound vessels and cost of electricity consumed during berthing. Transmission costs for port berths are generally between USD 300000 and USD 4 million; these are determined by port location, electricity demand, voltage and frequency, and ship type. The electricity fee charged by the port of Rotterdam is USD 4.3 million per berth, while the cost of two berths in the port of Gothenburg is only USD 276088. The cost of one shore power facility in Long Beach is between USD 10 million and USD 150 million, and the cost of a European cruise ship berth ranges from USD 1.84 million to USD 86.6 million (
4 Results and discussion
4.1 The cost of Sulphur Oxides abatement
4.1.1 The cost of switching to low-sulphur fuel
The result here is based on the assumption that the price differences between fuels in 2030 will be roughly similar to current price differences. Given that assumption, the cost of using low sulphur oil has been calculated by using the average difference in fuel prices paid by ships using fuels with different sulphur contents in Shanghai in January 2017 and May 2018. Therefore, the cost of switching to low sulphur oil can be expressed as:
where ${{P}_{L}}$ is the price of low-sulphur oil and ${{P}_{H}}$ of high-sulphur oil, ${{Q}_{N}}$ is the oil consumption, and W is other costs.
Based on VECC data, oil consumption in the ECA in 2030 will be 33.86 million tons, with Chinese ships accounting for 60% of the consumption. It is assumed that all ships sailing and berthing in the ECA have switched to 0.1%S fuel; thus, the cost of changing oil increases from USD 2.25 billion to USD 6.029 billion, with the average increase USD 2.787 billion. Details are listed in
As of 2017, there were 12624 shipping vessels in China, of which 10318 were coastal vessels and 2306 were ocean- going vessels. We assume that the cost of retrofitting ranges from USD 14139 to USD 21207 per ship. The cost of retrofitting to comply with ECA regulations is shown in
Costs | Highest | Lowest | Average |
---|---|---|---|
Switching oil cost | 6.029 | 2.250 | 2.787 |
Retrofit cost | 0.095 | 0.063 | 0.079 |
Total | 6.124 | 2.331 | 2.866 |
Table 2.
The cost of switching to low sulphur oil (unit: billion USD)
4.1.2 The cost of installing an exhaust gas recirculation system
Two-stroke diesel engines are the principal pieces of equipment for EGCSs and these are installed on ocean- going vessels and coastal vessels of over 6000 tons. Our estimate of the cost of installing EGCS is based on the quantity of Chinese ocean-going vessels and coastal vessels of more than 6000 tons and less than 8 years old, excluding foreign vessels, and is expressed as:
where K is the total power of installed vessels, ${{P}_{M}}$are the equipment costs, I stands for installation fees, and M stands for maintenance costs.
By the end of 2017, the total power of the main engines on oceangoing ships and coastal ships of 6000 tons or more and less than 8 years old was about 21790887 kW. Assuming that the lifespan of the EGCS is 20 years, the fuel consumption of a medium speed diesel engine is about 200 g kWh-1 with sailing time of approximately 180 days per year. The cost of using EGCSs is shown in
Year | Costs | Highest | Lowest | Average |
---|---|---|---|---|
20 years | Equipment costb | 5.615 | 1.743 | 3.679 |
Installation cost | 1.307 | 0.697 | 1.002 | |
Maintenance cost | 0.160 | 0.019 | 0.090 | |
Total cost | 7.082 | 2.459 | 4.771 | |
2030 | Equipment costc | 0.281 | 0.087 | 0.184 |
Installation costc | 0.065 | 0.035 | 0.050 | |
Maintenance cost | 0.160 | 0.019 | 0.0895 | |
Total cost | 0.510 | 0.141 | 0.324 |
Table 3.
The cost of using EGCS (unit: billion USD)
4.2 The cost of Nitrogen Oxide abatement
4.2.1 The cost of installing selective catalytic reduction systems
According to China’s requirements for the control of Nitrogen Oxide from ships, new ships with engine power greater than 37 kW must meet Tier III requirements. That is, new ships with engine power greater than 37 kW must be equipped with an SCR or alternative equipment to meet the nitrogen oxide control requirements. The cost of an SCR is expressed as:
where ${{K}_{s}}$ is the total power of vessels installed with SCRs, ${{P}_{Ms}}$is equipment costs, ${{I}_{s}}$stands for installation fees, and ${{M}_{s}}$ stands for maintenance costs.
In China, there were approximately 86670 ships with 37 kW or more of engine power in 2018; the total power was 424245568 kW. AIS data shows that there were 5596 ships berthing and navigating in China, Europe and United States in 2016 and 2017, including 832 Chinese ships. The cost of using SCRs is shown in
Costs | Highest | Lowest | Average |
---|---|---|---|
Equipment cost c | 1.109 | 0.416 | 0.763 |
Installation costc | 0.444 | 0.125 | 0.285 |
Maintenance cost | 0.037 | 0.010 | 0.024 |
Total cost | 1.591 | 0.551 | 1.071 |
Table 4.
The cost of using SCR (unit: billion USD)
4.2.2 The cost of installing exhaust gas recirculation systems
Installing a SCR system with an EGCS requires a lot of space, so this is not a preferred solution for ship owners. In such cases owners choose to install an EGR. Thus the proportion of ships with EGRs installed in this scenario is the same as the proportion of ships with EGCSs installed. The cost of using an EGR is shown in
Costs | Highest | Lowest | Average |
---|---|---|---|
Equipment costc | 0.068 | 0.056 | 0.062 |
Installation costc | 0.020 | 0.011 | 0.016 |
Maintenance cost | 0.385 | 0.264 | 0.325 |
Total cost | 0.474 | 0.330 | 0.402 |
Table 5.
The cost of using EGR (unit: billion USD)
4.3 The cost for LNG vessels
Costs | Highest | Lowest | Average |
---|---|---|---|
Retrofit costc | 0.296 | 0.148 | 0.222 |
New-build costc | 0.013 | 0.007 | 0.010 |
Total cost | 0.309 | 0.155 | 0.232 |
Table 6.
The cost for LNG vessels (unit: billion USD)
4.4 The cost for installing shore power facilities
China’s Port Power Distribution Plan requires that the construction of shore power facilities be completed at 257 berths in China’s major ports and the ports within ECA before 2030. According to the Statistical Bulletin on the Development of the Transportation Industry in 2017, as of 2017, China had 10318 coastal transportation vessels and 2306 ocean-going vessels, a total of 12624. We assume that 80% of the ships will install equipment to access shore power by 2030, and that the cost of upgrading is USD 0.3 million to USD 1 million per ship. The cost of applying shore power application is shown in
Costs | Highest | Lowest | Average |
---|---|---|---|
Construction costc | 0.012 | 0.012 | 0.012 |
Retrofitted cost | 0.505 | 0.151 | 0.328 |
Total cost | 0.517 | 0.163 | 0.340 |
Table 7.
The cost for applying shore power (unit: billion USD)
5 Conclusions
Based on our calculations: a total of USD 2.331 billion to USD 6.124 billion will be invested to switch to low sulphur fuel; a total of USD 0.141 billion to USD 0.51 billion will be invested for EGCSs, a total of USD 0.551 billion to USD 1.591 billion will be invested for SCR systems; and a total of USD 0.33 billion to USD 0.474 billion will be invested for EGR systems if a DECA is established. The cost for of building LNG vessels or converting existing vessels will be USD 0.155 billion to USD 0.309 billion, and investments in shore power applications will amount to USD 0.163 billion to USD 0.517 billion.
References
[1] Baltic Sea NECA application. Baltic Marine Environment Protection Commission, Finland., 1-95(2016).
[2] C Deniz, B Zincir. Environmental and economical assessment of alternative marine fuels. Journal of Cleaner Production, 113, 438-449(2016).
[3] Partners Incentive. Economic impact assessment of a non-emission control area in the North Sea. Ministry of the Environment,. Environmental Protection Agency, Denmark, 6-105(2012).
[4] Organization International Maritime. Information about the application status of Tier III compliant technologies. International Maritime Organization, England, 4-18(2014).
[5] Organization International Maritime. Special area under MARPOL. International Maritime Organization, England, 1-56(2018).
[6] O Kristensen.H. Energy demand and exhaust gas emissions of marine engines. Clean Shipping Currents, 1, 18-26(2012).
[7] P Jiang L, K Jacob, C Leise P. The costs and benefits of sulphur reduction measures: Sulphur scrubbers versus marine gas oil. Transportation Research, D, 19-27(2014).
[8] Report on how to develop powerful transportation(2018).
[10] I Panasiuk, S Lebedevas. The comparison of technologies to reduce the toxicity of ship exhaust gas. The 8th International Conference on Transbaltica 2013, Vilnius, 153-158(2013).
[11] Group Starcrest Consulting. Global LNG bunkering infrastructure as of January 2014(2012).
[12] Proposal to designate an emission control area for nitrogen oxides, sulphur oxides and particulate matter. Environmental Protection Agency, USA, 1-74(2009).
[13] Proposal to designate an emission control area for Nitrogen Oxides, Sulphur Oxides and Particulate matter, technical support document, chapter 2: Emission Inventory. Environmental Protection Agency, USA, 8-63(2019).
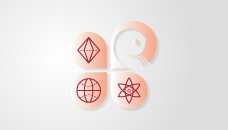
Set citation alerts for the article
Please enter your email address