Abstract
Investigations are performed to explore high-repetition-rate femtosecond laser ablation effects on the physical and chemical properties of poly(methyl methacrylate) (PMMA). A scanning electron microscopy (SEM) is used to characterize the morphology change in the laser-ablated regions. The infrared and Raman spectroscopy reveals that the fundamental structure of the PMMA is altered after laser ablation. We demonstrate the cumulative heating is much greater during high-repetition-rate femtosecond laser ablation, supporting a photothermal depolymerization mechanism during the ablation process.Poly(methyl methacrylate) (PMMA) has been used in many technological fields due to its excellent optical transparency, light weight, and good mechanical properties. Recently, femtosecond laser micromachining has attracted great attention for microdevice fabrication, as it provides excellent materials with high precision and few heat-affected zones[1–3]. The mechanism of the femtosecond laser ablation of polymers has been thoroughly studied in the past decades[4,5]. Suriano et al. examined the ablation of PMMA with a Ti:sapphire femtosecond laser, and the chemical functional groups of PMMA were found to remain unaffected, suggesting a thermal depolymerization process[6]. Morikawa et al. investigated the 800 nm femtosecond laser processing of PMMA, and observed the breaking of bonds and the formation of defects[7]. Lee et al. reported that the chemical bond was less decomposed during infrared (IR) femtosecond laser micromachining, suggesting the optical-thermal effect was more significant than the optical-chemical effect[8]. In most cases, chirped pulse amplification technology was used to generate femtosecond lasers with pulse repetition rates ranging from a few kilohertz up to 100 kHz, and the corresponding processing speeds were too low for industrial applications, due to their weak average power and low repetition rates[9,10]. On the other hand, high-repetition-rate pulse lasers could improve the processing speeds, but could also cause heat to accumulate in the surrounding material. Thus, there were very few studies on polymer micromachining with a high-repetition-rate femtosecond laser[11].
In this study, we applied high-repetition-rate, ultrashort pulse lasers for the precise micromachining of PMMA. The morphological character was observed with a scanning electron microscope (SEM). To better understand the process of chemical modification, an IR spectrometer and a micro-Raman spectrometer were used.
The laser source was a homemade large-mode-area photonic crystal fiber amplifier, which delivered pulses with a duration of 115 fs (FWHM) and had a center wavelength at 1040 nm and a repetition rate of 57 MHz. The laser power was continuously adjusted with a combination of a half-wave plate and a polarization beam splitter. The laser beam was tightly focused by a long working distance objective lens with a numerical aperture of 0.40. In order to void the cross section of any contaminants, the sample was linearly scratched with a sharp knife on the back surface before laser ablation. Then, the sample was mounted on a precision three-dimensional translation stage at a position with respect to the incident laser beam by a computer, and the reflected laser beam from the sample was monitored using a CCD camera. An electronic shutter was placed in the incident beam path for the exact adjustment of the ablation time. The direction of the laser scanning was perpendicular to the scratched line. After laser ablation on the front surface, the sample was fractured so we could observe the cross-section profile. Therefore, the fracture was always perpendicular to the grooves. The features of the craters and grooves ablated with the femtosecond laser were determined by field emission scanning electron microscopy (Nova NanoSEM 430, FEI, USA). The specular reflection Fourier transform IR (FTIR) spectra of PMMA both before and after the laser ablation were acquired using a Bio-Rad FTS 6000 FTIR spectrometer. Raman spectroscopy, measured with an InVia-Reflex system, was carried out to obtain further insight into chemical changes induced by the femtosecond laser micromachining of the PMMA.
Sign up for Chinese Optics Letters TOC. Get the latest issue of Chinese Optics Letters delivered right to you!Sign up now
Figure 1 illustrates the morphology evolution of the laser-irradiated areas produced by a laser power of 1.3 W on a PMMA plate. Figure 1(a) shows the swelling of the focal spot of the sample after 5 ms of laser exposure. A volcanic crater encircled by a ruptured dome-like structure was observed after 40 ms of laser exposure, as shown in Fig. 1(b). Their formation could be explained by the porosity increase due to hydrodynamic expansion. The laser heating of the polymer causes the generation and propagation of a thermoelastic wave. The laser pulse duration is much less than the characteristic propagation time of the thermoelastic wave in the polymer. The thermoelastic stress is confined within the laser focal spot during the laser pulse, leading to a significant rise in pressure. The tensile stress wave is produced together with the thermal or chemical dissociation of the polymer into a small volatile species, which resulted in the bubble nucleation and growth. After the repetitive laser irradiation of the surface, heat and mechanical stresses would accumulate. With a high-repetition-rate, ultrashort pulse laser, a temperature rise can be expected of several tens of times that of a single pulse[11,12]. As a result, the high-repetition-rate, ultrashort pulse laser ablation of the PMMA was heterogeneous with the formation of the porous structures. The surface of the laser focal spot swelled. As the number of pulses increased, the crater occurred in the center of laser spot.
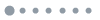
Figure 1.SEM images of the femtosecond laser-ablated craters with (a) 5 and (b) 40 ms exposure time on the PMMA.
Figure 2 shows the SEM images of the groove morphology and the cross-section profile ablated with a linearly polarized laser. The laser power and scanning speed were 4.7 W and 1 mm/s, respectively. We found that the groove machined with the high-repetition-rate, ultrashort pulse laser is straight and clear. The fracture image reveals that single-scan laser ablation produced a narrow and deep groove, and a few pieces of debris and burrs are seen at the edges of the profile contours. This indicated that thermal degradation dominated in the laser ablation. However, there is still the signature of the heat effect. The edge of the laser-ablated groove is smooth. This was the result of the re-solidification of the molten materials that occurred during the laser ablation of the PMMA. Although a linearly polarized femtosecond laser was applied in this case, there was no sign of polarization dependence in the ablation features. However, the quasi-periodic structures induced by the linearly polarized, near-IR femtosecond laser at repetition rates of 5 and 1 kHz were observed inside the ablated region of the polymer[12–15]. Ezquerra et al. reported that the accumulation of laser pulses on the focal spot could induce subsequent cycles of heating and cooling[16], and recorded the interference pattern between the incident laser beam and the scattered surface of polymer, i.e., the quasi-periodic structures. Moreover, Eaton et al. found the cumulative heating was much stronger at repetition rates greater than 200 kHz in femtosecond laser micromachining[17,18]. Therefore, we assume that the cumulative heating at a repetition rate of 57 MHz would lead to the melting and breaking of the quasi-periodic structure.
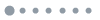
Figure 2.SEM images of (a) the single-scan line ablation and (b) its cross-section profile on the PMMA.
The IR spectra of the PMMA before and after the femtosecond laser ablation are overlapped for comparison in Fig. 3. A new weak absorption at , due to the stretching vibration, is usually related to unconjugated unsaturated groups[19] (usually ) or a methyl methacrylate (MMA) monomer[20]. Such functional groups could be formed by either photochemical or photothermal decomposition. Suriano et al.[6] reported that the absorption peak did not appear at all after the femtosecond laser ablation (, ). Moreover, the cumulative heating was more common at repetition rates greater than 200 kHz in the femtosecond laser micromachining[17,18]. Therefore, the absorption peak in our case likely resulted from a photothermal effect. However, the change in the FTIR spectra after micromachining with a high-repetition-rate, ultrashort pulse laser is limited, equivalent to an ultraviolet, nanosecond laser micromachining.
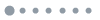
Figure 3.FTIR spectra of the pristine (black) and the laser-ablated (red) PMMA surface.
Interestingly, the absorption of the stretching band at and the stretching band at was significantly reduced after the laser ablation, suggesting a side-chain scission of PMMA[21]. The breakage of chemical bonds, the formation of free radicals, and unsaturation could result in a decrease of the peak heights in the IR spectra[22]. On the other hand, oxidation could cause the increase of IR band intensities of polar groups such as carbonyl one ()[21]. Therefore, we assume the degradation in our case went through a thermal non-oxidative process[23,24].
The Raman spectra of the laser-ablated and pristine PMMA samples are compiled in Fig. 4. One prominent spectral change was the strong background photoluminescence in the laser-ablated regions (see Fig. 4). Since the femtosecond laser-ablated PMMA experienced ultrafast heating and cooling, structural defects and voids were produced. A large concentration of defects was left over after a quick thermal quenching and re-solidification[7]. However, the intensity of the background photoluminescence was limited compared with that of Ref. [7] (it was strong enough to make the characteristic peaks disappear). This indicated that the number of defects is lower during high-repetition-rate, ultrashort pulse laser micromachining. Perhaps this is because their ablated threshold is lower than that of ultrashort laser with pulse repetition rates of a few kilohertz. High-repetition-rate, ultrashort pulse laser micromachining would affect the mechanical strength less.
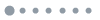
Figure 4.Raman spectra of the pristine (red) and the laser-ablated (black) PMMA surface.
The weak, broad peak at could be the stretching mode of the bond, associated with the end-groups of the oligomer chains and MMA monomer. This is consistent with what we observed in IR absorption spectra.
One additional Raman band at was observed in the laser-ablated samples. This weak peak probably corresponds to the second-order feature. A second-order Raman peak is related to the zone boundary contributions and the disorder-induced scattering[25]. Raimondi et al. reported that the laser could induce carbonization on polymer surfaces[26]. Tsvetkova et al. confirmed the formation of the presence of amorphous and microcrystalline graphite in PMMA implanted with low-energy ions[27]. The peak at likely resulted from nanoscale carbon, which has a higher degree of crystallinity. The second-order Raman feature in our case is probably associated with the crystal sizes and the defects induced by laser ablation.
In conclusion, we describe the surface and physico-chemical properties of PMMA ablated by a high-repetition-rate femtosecond fiber laser. The SEM images show that the quasi-periodic structure induced by the linear polarization is not formed on the laser-ablated region, suggesting cumulative heating on the surface during high-repetition-rate femtosecond laser ablation. However, the heat effect is limited. The photo-oxidation does not occur in spite of the laser ablation at the ambient atmosphere. Additionally, the mechanical strength modification by the high-repetition-rate, ultrashort pulse laser micromachining is also limited. Therefore, a high-repetition-rate, ultrashort pulse laser is most appropriate for PMMA micromachining.
References
[1] X. Ni, K. K. Anoop, M. Bianco, S. Amoruso, X. Wang, T. Li, M. Hu, Z. Song. Chin. Opt. Lett., 11, 093201(2013).
[2] G. Tang, J. Wei, W. Zhou, R. Fan, M. Wu, X. Xu. Chin. Opt. Lett., 12, 090604(2014).
[3] W. Dong, J. Wei, X. Wang, Z. Kang, X. Xu. Chin. Opt. Lett., 12, 090601(2014).
[4] T. Lippert. Plas. Proc. Polym., 2, 525(2005).
[5] W. Jia, Y. Luo, Y. Song, B. Liu, M. Hu, C. Wang. Nanotech. Prec. Eng., 13, 205(2015).
[6] R. Suriano, A. Kuznetsov, S. M. Eaton, R. Kiyan, G. Cerullo, R. Osellame, B. N. Chichkov, M. Levi, S. Turri. Appl. Surf. Sci., 257, 6243(2011).
[7] J. Morikawa, A. Orie, T. Hashimoto, S. Juodkazis. Appl. Phys. A, 98, 551(2010).
[8] C. Y. Lee, T. C. Chang, S. C. Wang, C. W. Chien, C. W. Cheng. J. Laser Micro/Nanoeng., 6, 87(2011).
[9] S. Nolte, S. Döring, A. Ancona, J. Limpert, A. Tünnermann. Proceedings of Advances in Optical Materials(2011).
[10] A. Ancona, K. Rademaker, F. Röser, J. Limpert, S. Nolte, A. Tünnermann. Proceedings of Conference on Lasers and Electro-Optics and Conference on Quantum Electronics and Laser Science(2008).
[11] S. Gaspard, M. Forster, C. Huber, C. Zafiu, G. Trettenhahn, W. Kautek, M. Castillejo. Phys. Chem. Chem. Phys., 10, 6174(2008).
[12] F. Baset, A. Villafranca, J.-M. Guay, R. Bhardwaj. Appl. Surf. Sci., 282, 729(2013).
[13] J.-M. Guay, A. Villafranca, F. Baset, K. Popov, L. Ramunno, V. R. Bhardwaj. New J. Phys., 14, 085010(2012).
[14] E. Rebollar, J. R. V. de Aldana, J. A. Perez-Hernandez, T. A. Ezquerra, P. Moreno, M. Castillejo. Appl. Phys. Lett., 100, 041106(2012).
[15] M. Castillejo, T. A. Ezquerra, M. Martín, M. Oujja, S. Pérez, E. Rebollar. AIP Conf. Proc., 1464, 372(2012).
[16] I. Martín-Fabiani, E. Rebollar, S. Pérez, D. R. Rueda, M. C. García-Gutiérrez, A. Szymczyk, Z. Roslaniec, M. Castillejo, T. A. Ezquerra. Langmuir, 28, 7938(2012).
[17] S. M. Eaton, H. Zhang, P. R. Herman. Opt. Express, 13, 4708(2005).
[18] S. M. Eaton, H. Zhang, M. L. Ng, J. Li, W. Chen, S. Ho, P. R. Herman. Opt. Express, 16, 9443(2008).
[19] B. J. Holland, J. N. Hay. Polym., 42, 4825(2001).
[20] S. J. Duray, J. L. Gilbert, E. P. Lautenschlager. Dent. Mater., 13, 240(1997).
[21] S. Beauvois, D. Renaut, R. Lazzaroni, L. D. Laude, J. L. Bredas. Appl. Surf. Sci., 109/110, 218(1997).
[22] S. Z. Szilasi, R. Huszank, D. Szikra, T. Váczi, I. Rajta, I. Nagy. Mater. Chem. Phys., 130, 702(2011).
[23] F. Namouchi, H. Smaoui, N. Fourati, C. Zerrouki, H. Guermazi, J. J. Bonnet. Alloys Comp., 469, 197(2009).
[24] M. E. Fragalà, G. Compagnini, L. Torrisi, O. Puglisi. Nucl. Instr. Meth. Phys. Res. B, 141, 169(1998).
[25] R. J. Nemanich, S. A. Solin. Phys. Rev. B, 20, 392(1979).
[26] F. Raimondi, S. Abolhassani, R. Brütsch, F. Geiger, T. Lippert, J. Wambach, J. Wei, A. Wokaun. J. Appl. Phys., 88, 3659(2000).
[27] T. Tsvetkova, S. Balabanov, L. Bischoff, V. Krastev, P. Stefanov, I. Avramova. J. Phys. Conf., 253, 012070(2010).