
- Chinese Optics Letters
- Vol. 21, Issue 4, 041205 (2023)
Abstract
1. Introduction
In recent years, torsion sensors have been extensively studied and developed due to the increasing demand for structural health monitoring. So far, various torsion sensors have been reported, including mechanical, electromagnetic, and all-fiber types. Among them, fiber-optic sensors have attracted wide attention due to their excellent characteristics, such as compact size, high sensitivity, strong immunity to electromagnetic interference, corrosion resistance, and compatibility with fiber-optic systems. However, ordinary fibers are almost insensitive to torsion due to their symmetrical structure. Therefore, special fibers such as polarization-maintaining fibers (PMFs)[1], photonic crystal fibers (PCFs)[2,3], and multicore fibers (MCFs)[4–6] are widely used for torsion measurements. Liu et al. fabricated a torsion sensor using a seven-core fiber (SCF) with a torsion sensitivity of 0.4 nm/(rad/m)[4]. The cylindrically symmetric fiber sensors have similar responses to clockwise (CW) and counterclockwise (CCW) twists.
To achieve direction recognition, efforts have been devoted to three main processes. One is to apply the asymmetric destructive processes on optical fibers using a femtosecond laser or
In this Letter, we present a directional torsion sensor composed of a sandwiched helical SCF taper (MHSTM). The MHSTM structure is fabricated by a homemade fiber fusion tapering and rotating platform supported by a graphite heating unit. By tapering the SCF, the photoelastic effect in the cladding is enhanced when torsion is applied to the sensor. Thus high sensitivity and the ability to distinguish torsion directions are obtained. The torsion sensitivities of the proposed sensor in CW and CCW directions are 2.253 and
Sign up for Chinese Optics Letters TOC. Get the latest issue of Chinese Optics Letters delivered right to you!Sign up now
2. Fabrication and Principle
The schematic diagram of the MHSTM structure is displayed in Fig. 1(a). The lead-in and lead-out fibers are all SMFs (SMF-28e+, Corning). The core and cladding diameters of the multimode fiber (MMF) (YOFC Co., Ltd.) are 105 and 125 µm, respectively. The SCF used is the commercially available product (SM-7C1500, Fibercore). The cross section of the SCF is shown in Fig. 1(c). The SCF has a central core and six satellite cores, where all the cores have identical diameters d of 8 µm and core distances of 35 µm. The cladding diameter is 125 µm.
Figure 1.(a) Schematic diagram of the MHSTM structure; (b) micrograph of the MHSTM structure under phase contrast microscope; (c) cross-sectional micrograph of the SCF.
There are two steps to fabricate an MHSTM structure. First, we spliced the SCF between two segments of MMFs by a fiber cleaver (FC-6S, Sumitomo) and a fusion splicer (FSM-62C, Fujikura). The length of the MMF and SCF is 0.5 mm and 3 mm, respectively. Second, we fix the structure on the helically tapered device, which consists of one rotating motor and two translation stages (Fig. 2). An “
Figure 2.Configuration of the homemade fiber fusion tapering and rotating platform.
As shown in Fig. 1(b), only the six outer cores are helical, while the center core stays straight. When fiber is rotated, according to the optic-elastic effect, the effective refractive index (ERI) increases, which is expressed as
The torsion sensitivity
For interference dips generated from CCM and CM, the torsion sensitivity is expressed as
3. Experimental Results and Discussions
As shown in Fig. 1(b), the total length
Figure 3.(a) Transmission spectrum of the MHSTM; (b) FFT spectrum of the transmission spectrum.
To measure the torsion sensitivity, the proposed sensor is connected to a supercontinuum source (SC, YSL Photonics SC-5) by the lead-in fiber. The lead-out fiber is connected to an optical spectrum analyzer (OSA, Yokogawa AQ6370D). A pair of fiber rotators (HFR-007, Thorlabs) holds the sensor, as shown in Fig. 4. One rotator is fixed, and another rotates 30° each step. The distance between the two rotators is 37.0 cm. It is worth noting that we define the CW direction as the consistent torsion direction with the HST, while the opposite direction is defined as the CCW direction.
Figure 4.Experimental setup for torsion sensitivity measurement.
The spectrum evolution as the torsion rate changes from 14.15 rad/m to
Figure 5.(a) Changing spectrum as the torsion force is applied; (b) piecewise linear fit of dip wavelength as a function of twist rate.
Figure 6.Piecewise linear fitting curves of wavelength of the (a) dip B and (b) dip C to the torsion rate.
In order to obtain the optimal sensing characteristics, we optimized the helical pitch
Figure 7.Linear fits of the dip wavelength to the torsion rate. (a) Under different taper waists w; (b) under different helical pitches Λ.
Figure 8.(a) Transmission spectrum evolution as temperature changes; (b) linear fit of the dip wavelength as a function of temperature.
Table 1 compares the characteristics of several sensors proposed previously and in this work. The proposed MHSTM structure exhibits distinct advantages in sensing performance. Moreover, light weight, compact size, and low fabrication cost all provide greater potential for the practical application of our structure.
Type | Bidirectional Discrimination | Max Torsion Sensitivity (nm/(rad/m)) | Ref. |
---|---|---|---|
SCF | No | 0.4 | [ |
Squared coreless fiber | No | 1.286 | [ |
Tapered SCF | No | 1.89 | [ |
Helical SCF | Yes | −0.118 | [ |
Helical PMF taper | Yes | −3.191 | [ |
Table 1. Comparison of Torsion Sensors
4. Conclusion
In conclusion, theoretical analysis and experimental demonstration of a high-sensitivity fiber torsion sensor based on MHSTM structure are presented. Our structure, fabricated by a graphite heater, is relatively low-cost compared to a
References
[1] Y. Q. Zhu, Y. S. Yu, Y. Zhao, Q. Guo, X. Y. Ming, C. X. Lei, H. B. Sun. Highly sensitive directional torsion sensor based on a helical panda fiber taper. IEEE Photon. Technol. Lett., 31, 1009(2019).
[2] F. Zhang, S. Liu, Y. Wang, Y. J. Huang, X. Z. Xu, C. L. Fu, T. S. Wu, C. R. Liao, Y. P. Wang. Highly sensitive torsion sensor based on directional coupling in twisted photonic crystal fiber. Appl. Phys. Express, 11, 042501(2018).
[3] P. St.J. Russell, R. Beravat, G. K. L. Wong. Helically twisted photonic crystal fibres. Philos. Trans. R. Soc. A, 375, 20150440(2017).
[4] C. Liu, Y. J. Jiang, B. B. Du, T. Wang, D. Y. Feng, B. Q. Jiang, D. X. Yang. Strain-insensitive twist and temperature sensor based on seven-core fiber. Sens. Actuator A Phys., 290, 172(2019).
[5] H. L. Zhang, Z. F. Wu, P. P. Shum, X. G. Shao, R. X. Wang, X. Q. Dinh, S. N. Fu, W. J. Tong, M. Tang. Directional torsion and temperature discrimination based on a multicore fiber with a helical structure. Opt. Express, 26, 544(2018).
[6] G. L. Yin, L. Lu, L. Zhou, C. Shao, Q. J. Fu, J. D. Zhang, T. Zhu. Distributed directional torsion sensing based on an optical frequency domain reflectometer and a helical multicore fiber. Opt. Express, 28, 16140(2020).
[7] G. L. Yin, Q. J. Fu, P. X. Yang, T. Zhu. Direction-discriminating torsion sensor based on optical fiber Mach-Zehnder interferometer. Opt. Laser Technol., 156, 108461(2022).
[8] R. Ulrich, A. Simon. Polarization optics of twisted single-mode fibers. Appl. Opt., 18, 2241(1979).
[9] Y. Y. Zhao, S. Liu, J. X. Luo, Y. P. Chen, C. L. Fu, C. Xiong, Y. Wang, S. Y. Jing, Z. Y. Bai, C. R. Liao, Y. P. Wang. Torsion, refractive index, and temperature sensors based on an improved helical long period fiber grating. J. Light. Technol., 38, 2504(2020).
[10] X. B. Cao, D. D. Tian, Y. Q. Liu, L. Zhang, T. Y. Wang. Sensing characteristics of helical long-period gratings written in the double-clad fiber by CO2 laser. IEEE Sens. J., 18, 7481(2018).
[11] P. Wang, H. P. Li. Helical long-period grating formed in a thinned fiber and its application to a refractometric sensor. Appl. Opt., 55, 1430(2016).
[12] Y. J. Jiang, T. Wang, C. Liu, D. Y. Feng, B. Q. Jiang, D. X. Yang, J. L. Zhao. Simultaneous measurement of refractive index and temperature with high sensitivity based on a multipath fiber Mach-Zehnder interferometer. Appl. Opt., 58, 4085(2019).
[13] S. J. Duan, X. Y. Bai, X. Y. Kang, H. Du, W. L. Liu, T. Geng, C. G. Tong, C. T. Sun, X. R. Jin, C. L. Lu, Y. X. Li, W. M. Sun, L. B. Yuan. High sensitive torsion sensor based on cascaded pre-twisted taper and multi-mode fiber sheets. IEEE Photon. Technol. Lett., 31, 1588(2019).
[14] J. M. Hsu, C. L. Lee, H. P. Chang, W. C. Shih, C. M. Li. Highly sensitive tapered fiber Mach-Zehnder interferometer for liquid level sensing. IEEE Photon. Technol. Lett., 25, 1354(2013).
[15] L. A. Wang, C. Y. Lin, G. W. Chern. A torsion sensor made of a corrugated long period fibre grating. Meas. Sci. Technol., 12, 793(2001).
[16] B. B. Song, Y. P. Miao, W. Lin, H. Zhang, J. X. Wu, B. Liu. Multi-mode interferometer-based twist sensor with low temperature sensitivity employing square coreless fibers. Opt. Express, 21, 26806(2013).
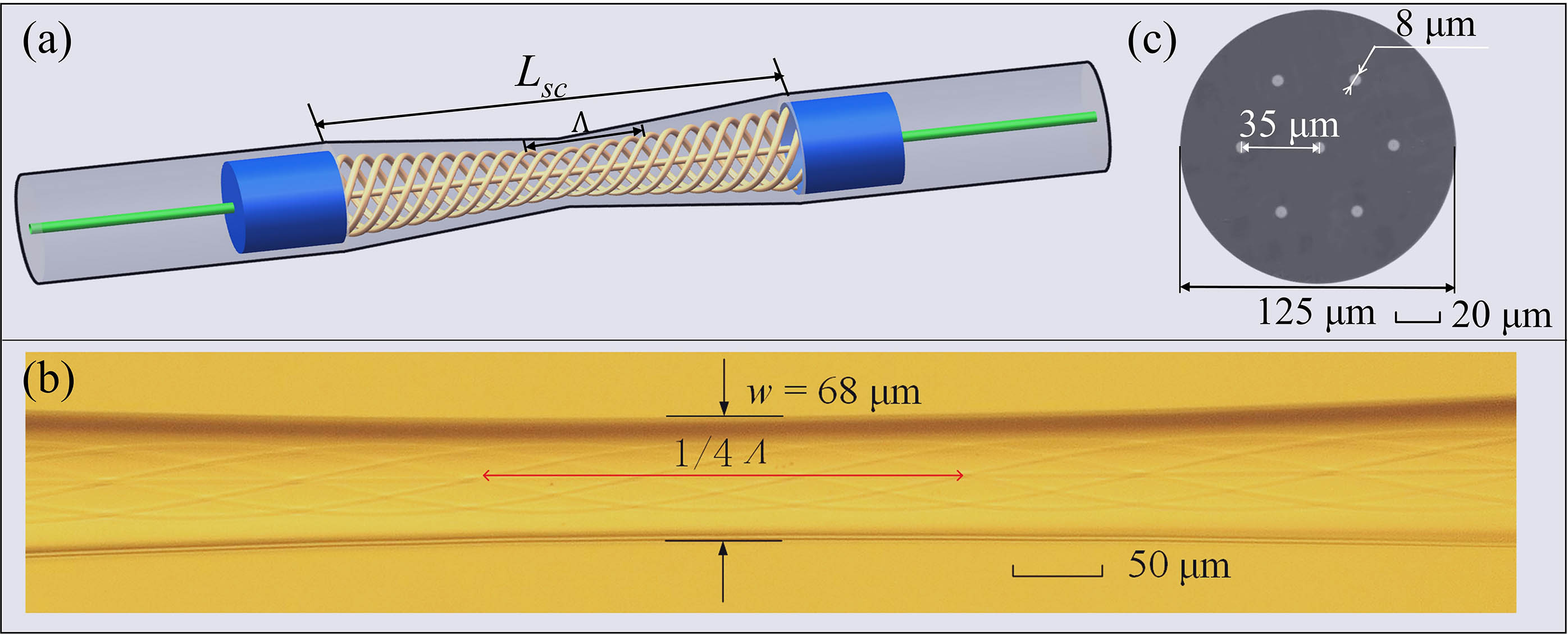
Set citation alerts for the article
Please enter your email address