Author Affiliations
Center for High Pressure Science (CHiPS), State Key Laboratory of Metastable Materials Science and Technology, Yanshan University, Qinhuangdao, Hebei 066004, Chinashow less
Abstract
Diamonds may not be forever, but research interest in diamond has never ebbed. Owing to its highly symmetric crystal structure and strong covalent C–C bonds, diamond possesses an exceptional combination of physical properties. Its hardness and thermal conductivity are the highest among covalent materials. It also has a large bandgap and electric breakdown field, as well as optical transparency over a wide range of wavelengths. All of these are essential for a wide range of applications in both industrial and scientific areas. Despite these outstanding advantages, however, diamond is extremely brittle, with inferior toughness and poor deformability. These shortcomings have caused undesired tool breakage and have imposed severe constraints on technological innovations. To surmount these intrinsic deficiencies, tremendous research effort has been dedicated to developing advanced diamond products, with great progress being achieved in the past few years.
The hardness of diamond can be enhanced via extrinsic hardening effects from grain or twin boundaries and dislocations. The Hall–Petch effect provides a general pathway to harden diamond by decreasing the characteristic length scale of the continuous crystal lattice. Grain boundaries and twin boundaries break the lattice continuity, thereby effectively preventing the motion of dislocations. Compared with grain boundaries, twin boundaries have a much lower excess energy. Nanotwinning is therefore more effective in reducing the characteristic length scale. Furthermore, with decreasing twin thickness, the quantum confinement effect (due to broadening of the bandgap at a deep nanometer scale) plays an increasingly important role in hardening diamond.1 With suitably selected carbon precursors such as carbon onion nanoparticles, nanotwinned diamond (nt-diamond) with an average twin thickness of ∼5 nm has been synthesized at high pressure and high temperature (HPHT) and exhibits an unprecedented hardness of up to 200 GPa.2 Usually, an increase in diamond hardness is accompanied by a decrease in toughness,2 a well-known trade-off between hardness and toughness of materials. In nt-diamond, coherent twin boundaries guide moving dislocations to change directions and glide along the twin boundaries, leading to a simultaneous improvement in fracture toughness.2
The microstructure of nt-diamond can be further tailored at a nanoscale through optimizing HPHT conditions, providing further enhancement of the mechanical properties of diamond-related materials.3 The synthesized nt-diamond composite possesses a unique structure in which coherently interfaced diamond polytypes, interwoven nanotwins, and interlocked nanograins are assembled in a hierarchical manner with increasing length scale.3 The architecture of this composite offers multiple toughening mechanisms, including nanotwin toughening, laminated composite toughening, and transformation toughening. As a result, an exceptional toughness as high as 26.6 MPa m1/2 has been achieved in nt-diamond composite, even higher than that of magnesium alloys. Meanwhile, the hardness of ∼200 GPa is maintained for this composite, identical to that of pure nt-diamond.
In addition to the mechanical performance enhancements achieved through microstructure engineering, progress has also been made in clearing up several long-standing puzzles about diamond, such as its poor deformability, its low tensile strength, and the existence of room-temperature plasticity,4–6 thanks to advances in sample preparation and characterization techniques.7 By reducing the dimensions of diamond crystals to minimize the influence of internal defects, high elastic tensile strain and tensile strength approaching the theoretical elasticity and Griffith theoretical strength (122 GPa) of diamond can be achieved in single-crystal diamond nanoneedles.4,5 For example, a 〈100〉-oriented 60-nm-diameter diamond nanoneedle deforms elastically to a tensile strain of 13.4% with a tensile strength of 125 GPa.5 This astonishing performance can be further improved with better control of minute surface defects such as steps caused by discontinuous atomic layers. Dislocation plasticity at room temperature has been confirmed in single-crystal diamond nanopillars, with clearly resolved spatiotemporal features of dislocation generation and propagation.6 State-of-the-art transmission electron microscope observations have also revealed orientation-dependent dislocation behavior in diamond crystals. For example, under uniaxial compression along the 〈111〉 and 〈110〉 directions, the {001}〈110〉 slip systems are activated, whereas under 〈100〉 compression, the {111}〈110〉 slips are activated. This behavior is strikingly different from that of face-centered cubic metals and silicon, where close-packed {111} planes are the primary slip planes.6 Remarkably large plastic strains of up to 5.8% have been achieved in nt-diamond sub-micropillars.7 In comparison, no significant plastic deformation was observed in single-crystal diamond nanopillars,8 suggesting a significant contribution from the polycrystalline nature of nt-diamond.
In the past decade, diamond materials with greatly enhanced mechanical performance have been successfully synthesized via microstructure engineering.2,3Figure 1 summarizes the hardness, toughness, and plasticity of different diamond materials.2,3,7 The advantages of nt-diamond and its composite suggest many innovative applications, such as durable diamond anvil cells (DACs) and high-performance machining tools with better efficiency, precision, and lifetime. As an ideal DAC material, nt-diamond composite, with its exceptionally high hardness and toughness, may provide pressures in excess of 1000 GPa, which are critical in the quest for metallic hydrogen and room-temperature superconductors. The strategy of structural architecture demonstrated in diamond can also be implemented in other ceramics with a cubic structure, to enhance their hardness, toughness, and plasticity. On the other hand, the improved understanding of diamond plasticity and deformability can further promote research on diamond and other brittle ceramic materials.4–6 The {001}〈110〉 slip systems identified as playing a role in diamond plasticity stimulate reconsideration of the basic deformation mechanism in brittle covalent crystals. The electronic and optical properties of diamond can be dramatically changed under significant lattice strains, and the ultrahigh elastic strain demonstrated in diamond nanoneedles may thus open up new opportunities in electronics applications.
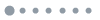
Figure 1.Comparison of room-temperature mechanical properties of different diamond materials. Note that for plasticity, the cross-hatched bar indicates the near-absence of plasticity in a diamond single crystal, while the striped bar indicates the expected plasticity in an nt-diamond composite.
References
[1] Z. Zhao, B. Xu, Y. Tian. Microscopic theory of hardness and design of novel superhard crystals. Int. J. Refract. Met. Hard Mater., 33, 93-106(2012).
[2] D. Yu, B. Xu, W. Hu, Y. Ma, Q. Huang, Z. Zhao, J. He, Y. Tian, B. Wen, Z. Liu, Y. Wang. Nanotwinned diamond with unprecedented hardness and stability. Nature, 510, 250-253(2014).
[3] B. Ge, Y. Wang, L. Guo, Y. Gao, X.-F. Zhou, Z. Wang, Z. Li, Y. Yue, B. Wei, X. Zhang, W. Hu, Y. Tian, Z. Yang, B. Xu, D. Yu, J. Wang, Q. Zhang, X. Liu, P. Ying. Hierarchically structured diamond composite with exceptional toughness. Nature, 582, 370-374(2020).
[4] M. Dao, H. Zhang, F. Ding, A. Banerjee, Y. Lu, M.-F. Yuen, J. Dong, S. Suresh, D. Bernoulli, J. Lu, J. Liu, W. Zhang. Ultralarge elastic deformation of nanoscale diamond. Science, 360, 300-302(2018).
[5] H. Wang, Y. Tian, A. Nie, J. He, Y. Zhang, Y. Bu, P. Li, W. Yang, T. Jin, Z. Liu, Y. Wang, J. Liu, Z. Su. Approaching diamond’s theoretical elasticity and strength limits. Nat. Commun., 10, 5533(2019).
[6] A. Nie, Y. Zhang, B. Xu, Y. Tian, W. Hu, Y. Shao, Y. Wang, Y. Bu, J. Huang, J. Liu, W. Yang, H. Wang, Z. Liu. Direct observation of room-temperature dislocation plasticity in diamond. Matter, 2, 1222-1232(2020).
[7] A. Nie, J. Huang, H. Wang, Y. Bu, Y. Tian, T. Jin, Y. Zhang. Atomic-scale observation of the deformation and failure of diamonds by in situ double-tilt mechanical testing transmission electron microscope holder. Sci. China Mater, 63, 2335-2343(2020).
[8] J. Michler, R. Raghavan, Y. Zhang, J. M. Wheeler, J. Wehrs, R. Erni. Approaching the limits of strength: Measuring the uniaxial compressive strength of diamond at small scales. Nano Lett., 16, 812-816(2016).