Sheng Ye, Shangman Zhao, Zhongfu Xing, Zhiyong Peng, Yuting Zheng, Liangxian Chen, Jinlong Liu, Chengming Li, Junjun Wei. Research and application progress of laser technology in diamond processing[J]. Infrared and Laser Engineering, 2024, 53(2): 20230567

Search by keywords or author
- Infrared and Laser Engineering
- Vol. 53, Issue 2, 20230567 (2024)
![Schematic diagram of energy level structure of Nd:YAG crystal[18]](/richHtml/irla/2024/53/2/20230567/img_1.jpg)
Fig. 1. Schematic diagram of energy level structure of Nd:YAG crystal[18]
![Absorption behavior of diamond and graphite [21]](/richHtml/irla/2024/53/2/20230567/img_2.jpg)
Fig. 2. Absorption behavior of diamond and graphite [21]
![Microscopic morphology of non-bond end-face grinding wheel with conical abrasive array structure[24]](/Images/icon/loading.gif)
Fig. 3. Microscopic morphology of non-bond end-face grinding wheel with conical abrasive array structure[24]
![(a) Effect of pulse duration on diamond ablation threshold; (b) Incubation effect[25]](/Images/icon/loading.gif)
Fig. 4. (a) Effect of pulse duration on diamond ablation threshold; (b) Incubation effect[25]
![Effect of plating different absorption layers on the transmittance of processed diamond [31]](/Images/icon/loading.gif)
Fig. 5. Effect of plating different absorption layers on the transmittance of processed diamond [31]
![Fluorescence image of NV color center array[33]](/Images/icon/loading.gif)
Fig. 6. Fluorescence image of NV color center array[33]
![Scanning electron microscope images of diamond surface irradiated by 800 nm femtosecond laser. (a) 170 nm periodic structure formed at 3000 pulse laser energy density of 1.9 J/cm2; (b) 190 nm periodic structure formed at 8000 pulse laser energy density of 2.8 J/cm2[36]](/Images/icon/loading.gif)
Fig. 7. Scanning electron microscope images of diamond surface irradiated by 800 nm femtosecond laser. (a) 170 nm periodic structure formed at 3000 pulse laser energy density of 1.9 J/cm2; (b) 190 nm periodic structure formed at 8000 pulse laser energy density of 2.8 J/cm2[36]
![With the increase of pulse time delay, the evolution of diamond surface morphology array[37]](/Images/icon/loading.gif)
Fig. 8. With the increase of pulse time delay, the evolution of diamond surface morphology array[37]
![Interaction model between laser, electron and lattice[23]. (a) Nanosecond laser; (b) Femtosecond laser](/Images/icon/loading.gif)
Fig. 9. Interaction model between laser, electron and lattice[23]. (a) Nanosecond laser; (b) Femtosecond laser
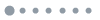
Fig. 10. FIB cross sections of PCD composites obtained by: (a) Lapping; (b) Wire EDM; (c) Laser when pulse width =10 ps; (d) Laser when pulse width =125 ns; (e) Laser when pulse width =450 μs
![Heat conduction and temperature distribution in the single crystal diamond at different scanning time, in which the arrowheads indicate the conductive heat flux direction[45]](/Images/icon/loading.gif)
Fig. 11. Heat conduction and temperature distribution in the single crystal diamond at different scanning time, in which the arrowheads indicate the conductive heat flux direction[45]
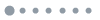
Fig. 12. Raman spectral images of machined pits under different laser fluxes
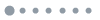
Fig. 13. Raman spectra of picosecond laser ablation of diamond micro-grooves at different laser energies
![(a) Schematic diagram of ps laser processing; (b) Optical picture of graphitized microstructure device; (c) Influence of orientation on machining morphology and machining threshold[52-53]](/Images/icon/loading.gif)
Fig. 14. (a) Schematic diagram of ps laser processing; (b) Optical picture of graphitized microstructure device; (c) Influence of orientation on machining morphology and machining threshold[52-53]
![Scanning electron microscope images of single crystal diamond surface processed by 200 fs laser. (a) Curved structure processed by laser pulse energy of 1.2 mJ; (b) The machined surface image when the laser pulse energy is 840 nJ; (c) An enlarged image of figure (b)[59]](/Images/icon/loading.gif)
Fig. 15. Scanning electron microscope images of single crystal diamond surface processed by 200 fs laser. (a) Curved structure processed by laser pulse energy of 1.2 mJ; (b) The machined surface image when the laser pulse energy is 840 nJ; (c) An enlarged image of figure (b)[59]
![Surface morphology of laser processing. (a) Nanosecond laser; (b) Femtosecond lasers[60]](/Images/icon/loading.gif)
Fig. 16. Surface morphology of laser processing. (a) Nanosecond laser; (b) Femtosecond lasers[60]
![Machining diamond through holes on silicon ball substrate by double pulse laser machining surface morpholog[68]](/Images/icon/loading.gif)
Fig. 17. Machining diamond through holes on silicon ball substrate by double pulse laser machining surface morpholog[68]
![The average aspect ratio obtained in diamond is 40∶1[69]](/Images/icon/loading.gif)
Fig. 18. The average aspect ratio obtained in diamond is 40∶1[69]
![Diamond microgrooves processed by process optimization parameters. (a) Surface morphology; (b) Cross-sectional morphology[26]](/Images/icon/loading.gif)
Fig. 19. Diamond microgrooves processed by process optimization parameters. (a) Surface morphology; (b) Cross-sectional morphology[26]
![Photos of manifold diamond microchannel[75]](/Images/icon/loading.gif)
Fig. 20. Photos of manifold diamond microchannel[75]
![Schematic diagram of laser ablation[79]](/Images/icon/loading.gif)
Fig. 21. Schematic diagram of laser ablation[79]
![Surface roughness of diamond with different scanning ranges. (a) 100 μm×100 μm; (b)10 μm×10 μm[85]](/Images/icon/loading.gif)
Fig. 22. Surface roughness of diamond with different scanning ranges. (a) 100 μm×100 μm; (b)10 μm×10 μm[85]
![The cross section SEM image of diamond sample after fs-laser treatment[87]](/Images/icon/loading.gif)
Fig. 23. The cross section SEM image of diamond sample after fs-laser treatment[87]
![CO2 laser/water-guided laser hybrid machining system[88]](/Images/icon/loading.gif)
Fig. 24. CO2 laser/water-guided laser hybrid machining system[88]
![Scanning electron microscope images of the ablation made with laser in silicon without. (a) And with water spray; (b) Both are made using 1000 pulses with 2.2 J energy per hole[93]](/Images/icon/loading.gif)
Fig. 25. Scanning electron microscope images of the ablation made with laser in silicon without. (a) And with water spray; (b) Both are made using 1000 pulses with 2.2 J energy per hole[93]
|
Table 1. Properties and applications of diamond
|
Table 2. Types of laser used in diamond processing
|
Table 3. Research progress of different processing types of laser processing diamond
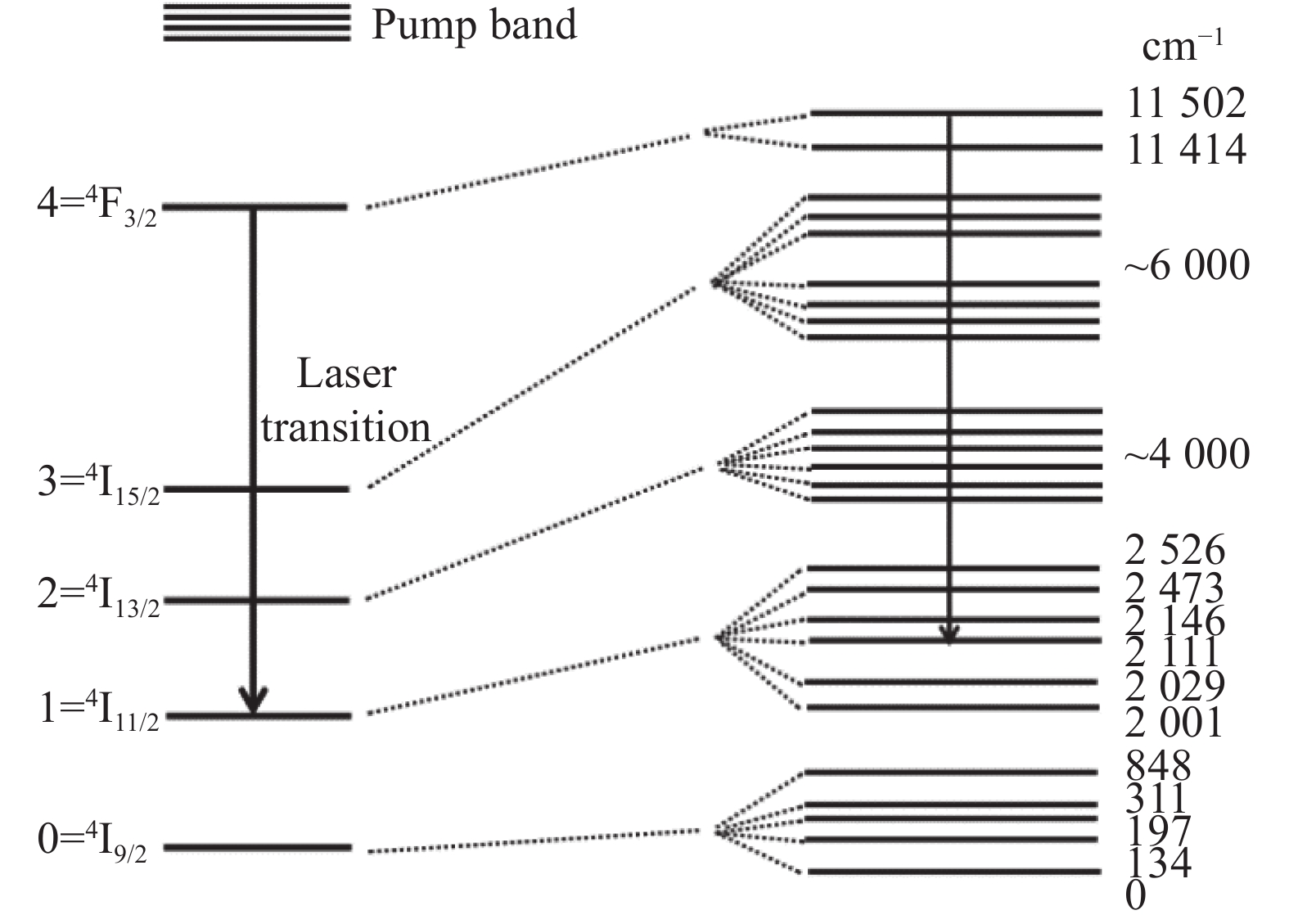
Set citation alerts for the article
Please enter your email address