
- Photonics Research
- Vol. 2, Issue 3, A19 (2014)
Abstract
1. INTRODUCTION
An optical interconnect with silicon photonics is thought to be a promising solution to the problem of bandwidth bottleneck in LSI chips [
In this system, the integrated CW light source must be multichannel, high density, and high power. Although integrated light sources formed on silicon-on-insulator (SOI) substrates have previously been reported [
We demonstrated a hybrid integrated light source with a configuration in which an LD array is mounted on a silicon optical waveguide platform for interchip optical interconnection [
Sign up for Photonics Research TOC. Get the latest issue of Photonics Research delivered right to you!Sign up now
In this paper, we discuss our multichannel and high density hybrid integrated light source. The paper is organized as follows. In Section
2. CONCEPT OF INTEGRATED LIGHT SOURCE
The integrated light source in the photonics-electronics convergence system is shown in Fig.
Figure 1.Schematic of integrated light source in photonics-electronics convergence system.
Requirements | Target | |
---|---|---|
High density | Narrow pitch | |
Small footprint/ch | ||
Multichannel | Multichannel/chip | 13 ch |
Multi-chip | 10–20 chip | |
splitter | ||
High power | High laser power | |
Low coupling loss | 2–3 dB |
Table 1. Requirements of Integrated Light Source for
3. STRUCTURE DESIGN AND FABRICATION
To meet these system requirements, a hybrid integrated light source with an LD array on a silicon waveguide platform was developed. The main structure is shown in Fig.
Figure 2.Hybrid integration structure with an LD array on a silicon waveguide platform.
A. LD Structure
Each LD in the array is a Fabry–Perot type LD with a spot size converter (SSC) including an inverse taper at the waveguide facet side and has a structure consisting of an InGaAsP base strained multiquantum well buried heterostructure (lasing wavelength of about 1.55 μm). The LD array has 13-channel stripes at a pitch of about 20 or 30 μm and alignment marks, as shown in Fig.
Figure 3.Photograph of 13-channel LD array. Cavity length is 400 μm, and array pitch is 30 μm.
B. Silicon Waveguide Platform Structure and Fabrication
The platform consists of waveguides with SSCs and an LD mounting stage. At the SSC, SiON and silicon optical waveguides are connected with a SiON core surrounding an inversely tapered silicon tip. The silicon optical waveguides have a core section size 440 nm wide and 220 nm high, and the SiON waveguides have a core section size of
The fabrication technology was based on a previous report [
Figure 4.Scanning electron microscope image of waveguide facet made by dry etching.
C. Hybrid Integration
The LD array is mounted on the silicon optical waveguide platform with AuSn solder bumps by flip-chip bonding, as shown in Fig.
Figure 5.(a) Schematic of LD mounting structure and (b) LD mounting image focused on alignment marks by transmission infrared light.
4. THIRTEEN-CHANNEL INTEGRATED LIGHT SOURCE AND ITS OPTICAL CHARACTERISTICS
A 13-channel light source was fabricated on the basis of the structure design. The fabricated hybrid integrated light source is shown in Fig.
Figure 6.(a) Schematic and (b) photograph of 13-channel hybrid integrated light source.
A. LD Performance
Figure
Figure 7.Dependence of light output of 13-channel LD array on operating current at room temperature without cooling.
B. Optical Coupling Tolerance
The optical coupling tolerance between the LD and the SiON waveguide along the horizontal and vertical directions was measured, as shown in Fig.
Figure 8.Optical coupling tolerance between LD and SiON waveguide along horizontal and vertical directions.
C. Output Uniformity
The relative light intensity of the 13-channel LD array and waveguide output ports in the light source are shown in Fig.
Figure 9.Relative light intensity of 13-channel LD array and waveguide output ports on integrated light source.
5. HIGH DENSITY AND MULTICHANNEL HYBRID INTEGRATED LIGHT SOURCE
A. Reducing Footprint per Channel by Introducing Waveguide Splitter
The bandwidth density of the photonic integrated circuits depends on the footprint per channel of the optical components [
Figure 10.(a) Schematic and (b) photograph of integrated light source with 52 output ports made possible by introducing waveguide splitter.
B. Increasing Number of Output Ports with Multichip Bonding Technology
The number of output ports was increased by using waveguide splitters and multichip bonding [
Figure 11.Schematic showing multichip bonding technology. (a) Mounting structure and (b) illustration of diffusion of Au on surface of electrodes into AuSn bump at soldering.
The Au composition of the AuSn solder we used is 80 wt. %. This composition is eutectic composition and the melting point is 280°C. When the Au content is over 80 wt. %, the melting point of AuSn increases dramatically, as shown in the phase diagram of AuSn alloy [
By using a waveguide splitter and this multichip bonding, we fabricated a light source with 104 output ports in which the silicon optical waveguides are split in four by double cascade
Figure 12.(a) Schematic and (b) photograph of integrated light source with 104 output ports with two LD array chips.
Figure
Figure 13.Near-field pattern of outputs in integrated light source with 104 output ports.
Figure
Figure 14.Histogram of relative intensity of output ports. (a) 1st–52nd channel port and (b) 53rd–104th channel port.
These results show that multichannel, high density, and high power operation can be demonstrated with a hybrid integrated light source with an LD array on a silicon optical waveguide platform.
6. CONCLUSION
We developed a hybrid integrated light source with a configuration in which an LD array was mounted on a silicon optical waveguide platform for interchip optical interconnection. Experimental results demonstrated a high density (20- or 30-μm pitch) and 13-channel uniform operation with the integrated light source as well as a low loss coupling due to the SiON waveguides with SSCs (coupling loss of 1 dB at zero deviation). The integrated light source including 52 output ports demonstrated a reduction in the footprint per channel. We also demonstrated a light source with more than 100 output ports in which the number of output ports was increased by using a waveguide splitter and multichip bonding. We expect the multichannel, high-density hybrid integrated light source to be easily adapted to the photonics-electronics convergence system for interchip interconnection.
References
[4] Y. Urino, S. Akiyama, T. Akagawa, T. Baba, T. Usuki, D. Okamoto, M. Miura, J. Fujikata, T. Shimizu, M. Okano, N. Hatori, M. Ishizaka, T. Yamamoto, H. Takahashi, Y. Noguchi, M. Noguchi, M. Imai, M. Yamagishi, S. Saitou, N. Hirayama, M. Takahashi, E. Saito, D. Shimura, H. Okayama, Y. Onawa, H. Yaegashi, H. Nishi, H. Fukuda, K. Yamada, M. Mori, T. Horikawa, T. Nakamura, Y. Arakawa. Demonstration of 30-Tbps/cm2 bandwidth density by silicon optical interposers fully integrated with optical components. 39th European Conference and Exhibition on Optical Communication, Mo.4.B.2(2013).
[5] J. Liu, X. Sun, R.-C. Aguilera, Y. Cai, L. C. Kimerling, J. Michel. Monolithic Ge-on-Si lasers for integrated photonics. Proceedings of IEEE 7th International Conference on Group IV Photonics, 1-3(2010).
[7] K. Tanabe, K. Watanabe, S. Faure, Y. Arakawa. 1.3 μm InAs/GaAs quantum dot lasers on Si substrates with current injection across direct-bonded GaAs/Si heterostructures. 37th European Conference and Exhibition on Optical Communication, Tu.6.LeSaleve.1(2011).
[8] S. Saito. Silicon and germanium quantum well light-emitting diode. Proceeding of IEEE 8th International Conference on Group IV Photonics, 166-168(2011).
[9] N. Kimura, K. Shinozaki, N. Kitamura, Y. Fukutomi, Y. Minota, H. Tanaka, A. Sato, H. Ando. Receptacle transceiver module using silica waveguide for bi-directional transmission over single fiber. Proceeding of 53th Electronic Components and Technology Conference, 290-295(2003).
[11] M. Shishikura, T. Ban, H. Ichikawa, T. Ido, M. Takahashi, K. Nakahara, E. Nomoto, Y. Matsuoka, K. Ishikawa, K. Ito, R. Takeyari, H. Sano, T. Hirose, H. Takahashi, T. Nagara, H. Chiba, S. Irikura. 10 Gbit/s per channel parallel optical transmitter and receiver modules for high-capacity interconnects. Proceeding of 53th Electronic Components and Technology Conference, 1040-1045(2003).
[12] T. Shimizu, N. Hatori, M. Okano, M. Ishizaka, Y. Urino, T. Yamamoto, M. Mori, T. Nakamura, Y. Arakawa. High density hybrid integrated light source with a laser diode array on a silicon optical waveguide platform for inter-chip optical interconnection. Proceeding of IEEE 8th International Conference on Group IV Photonics, 181-183(2011).
[13] T. Shimizu, N. Hatori, M. Okano, M. Ishizaka, Y. Urino, T. Yamamoto, M. Mori, T. Nakamura, Y. Arakawa. High density hybridly integrated light source with a laser diode array on a silicon optical waveguide platform. Integrated Photonic Research, Silicon and Nano Photonics, ITu4B.5(2012).
[14] T. Shimizu, M. Okano, N. Hatori, M. Ishizaka, Y. Urino, T. Yamamoto, M. Mori, T. Nakamura, Y. Arakawa. Multi-channnel and high density hybrid integrated light source on a silicon optical waveguide platform. Asia Communications and Photonics Conference, AF3B.2(2012).
[15] N. Fujioka, T. Chu, M. Ishizaka. Compact and low power consumption hybrid integrated wavelength tunable laser module using silicon waveguide resonators. J. Lightw. Technol., 28, 3115-3120(2010).
[16] T. Shimizu, Y. Akimoto, K. Kurata. An opto-electronic hybrid integrated platform with a polymer optical waveguide for high performance and low cost modules. Proceeding of 54th Electronic Components and Technology Conference, 1042-1045(2004).
[17] T. Sugimoto, T. Shimizu, Y. Akimoto, M. Noguchi, J. Sone, T. Watanabe, Y. Urino. A small and low cost bidirectional transceiver module with polymer waveguide for G-PON/Ge-PON. Proceeding of 57th Electronic Components and Technology Conference, 707-711(2007).
[18] J. Ciulik, M. R. Notis. The Au-Sn phase diagram. J. Alloys Compd., 191, 71-78(1993).
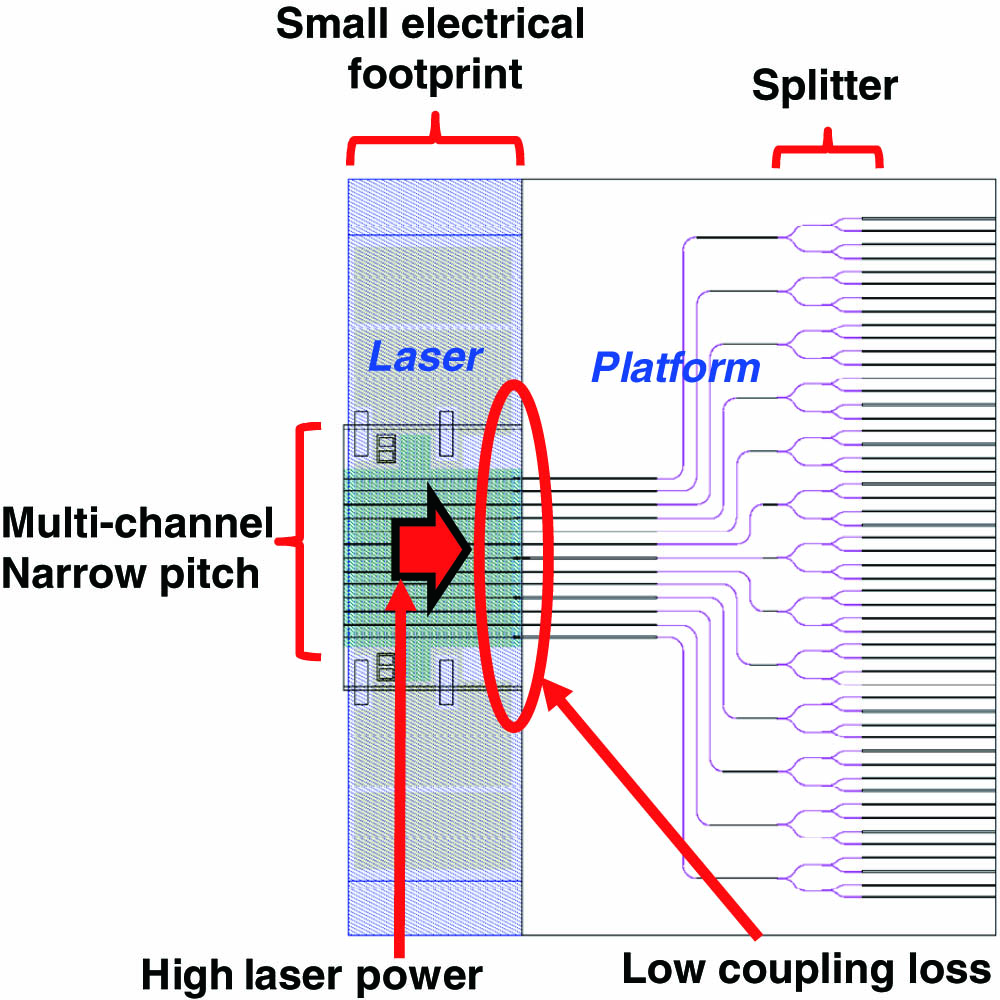
Set citation alerts for the article
Please enter your email address